Apprentices progress at their own pace – they demonstrate
competency in skills and knowledge through assessment tests,
but are not required to complete a specific number of hours.
competency in skills and knowledge through assessment tests,
but are not required to complete a specific number of hours.
Welding Inspector
USDOL
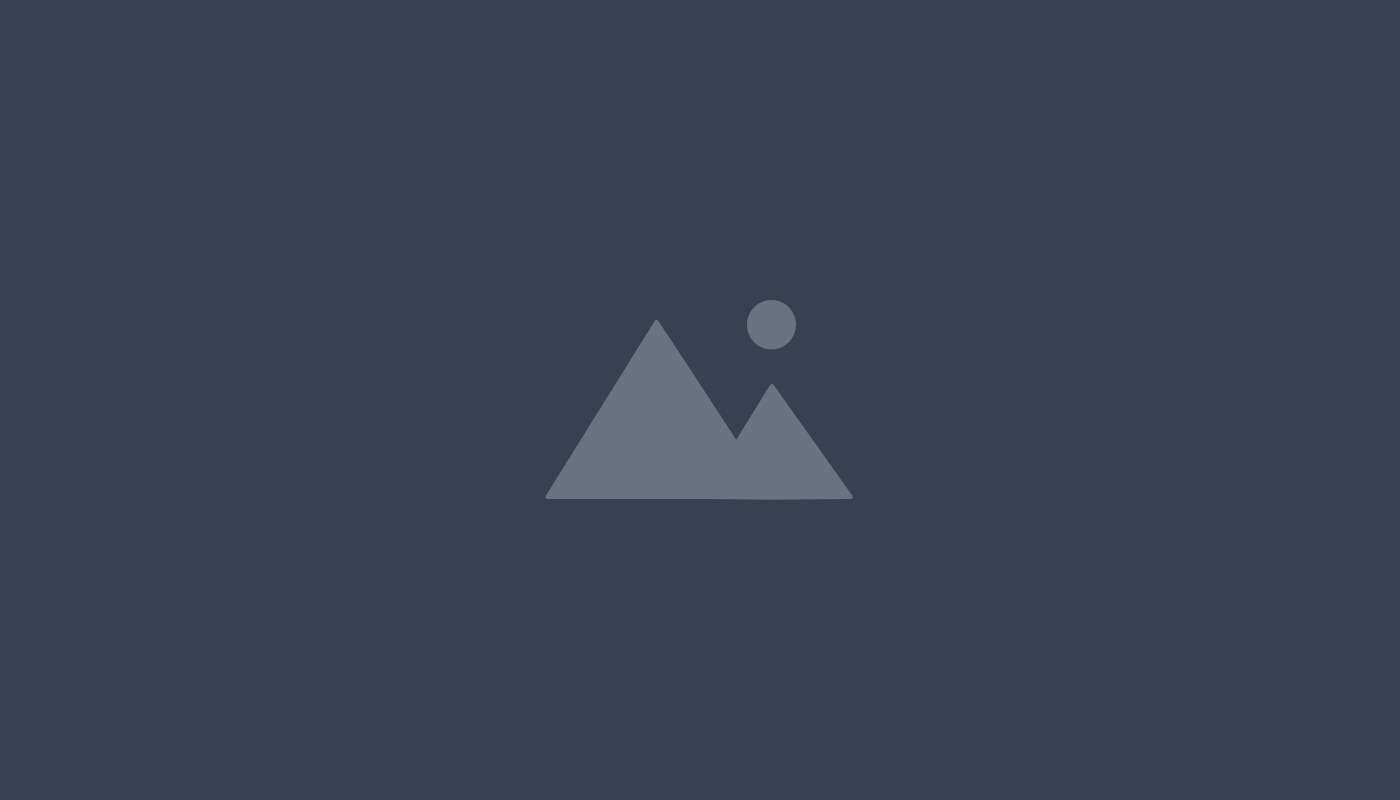
National (OA)
Documents
View Original Document
Individual state requirements may vary. Please contact your local apprenticeship office to ensure this version is suitable to your state’s requirements.
Work Process Content
On the Job Training
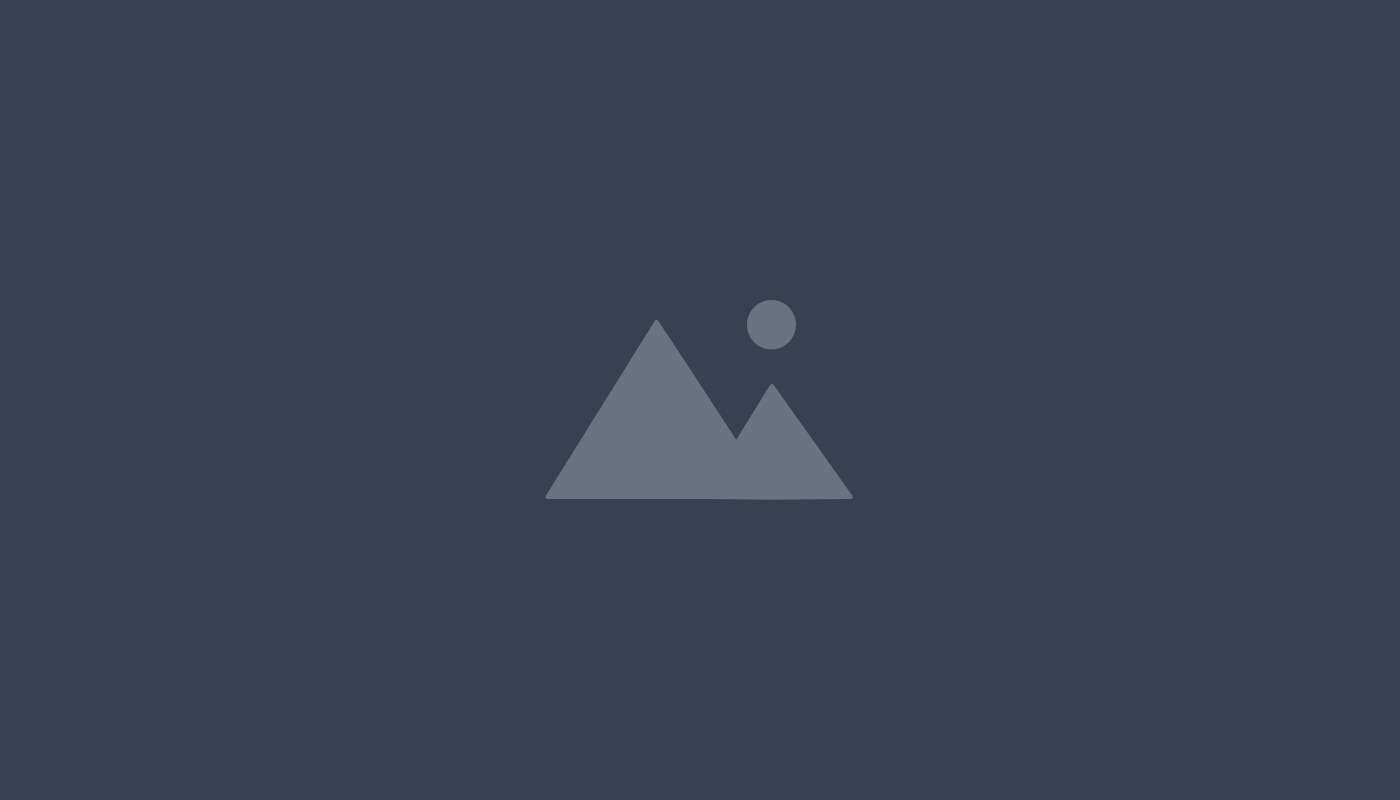
Anonymous
78
Skills
Welding Fundamentals
10
Welding Fundamentals
10
- Knowledgeable in Safe Work Practices & Welding Safety-per ANSI/AWS Z49.1
- Minimum comprehension and understanding with welding and joining processes for manufacturing and repair.
- Weld Joint Preparation before welding per a WPS
- Minimum Proficiency with welding technique, power sources, filler metals their proper selection and use.
- Basic Understanding of GMAW Equipment Setup & Operation
- Basic Understanding of FCAW Equipment Setup & Operation
- Basic Understanding of SMAW Equipment Setup & Operation
- Basic Understanding of GTAW Equipment Setup & Operation
- Minimum comprehension and understanding with standard Weld Joints and Welding Positions in accordance with AWS A3.0
- Basic Understanding of thermal cutting and gouging operations
Material Joining and Welding Metallurgy
6
Material Joining and Welding Metallurgy
6
- Basic Understanding of welding metallurgy, base metal and filler metal chemistry, and alloys used in industry.
- Basic, Minimum comprehension and understanding of the weldability of ferrous and nonferrous base metals.
- Basic, Minimum comprehension and understanding of the mechanical properties of base metals and deposited weld metal.
- Basic Understanding of the HAZ and its metallurgical significance in welded joints, and effect of preheat for carbon and low alloy steels.
- Basic Understanding of time/temperature measurement, preheat, holding times, and cooling rates in PWHT when applicable.
- Basic Understanding of metallographic techniques used for analyzing weld microstructures.
Welding Codes & Standards
11
Welding Codes & Standards
11
- Minimum comprehension and understanding with the organizations responsible for developing and publishing welding codes, specifications, and standards (e.g., AWS, ASME, ISO).
- Basic understanding of ASNT SNT-TC-1A and its application in regard to welding and QC systems.
- Basic understanding of the role of federal and local government rules, regulations, and industry-specific standards where applicable.
- Understand the welding inspector’s responsibilities versus contractor, engineer, manufacture within the code or standard.
- Basic understanding of the roles and responsibilities of personnel involved in quality control and quality assurance.
- Understand and apply reference documents; including other industry standards and codes that are integral to welding inspections
- Basic understanding of material specification documents.
- Basic understanding of the requirements for welding repairs and modifications to welded components per the specified, referenced construction code or standard.
- Basic understanding of the requirements for base material identification, chemical composition, and mechanical properties per the specified, referenced construction code or standard.
- Basic understanding of the visual testing (VT) acceptance criteria for of discontinuities / defects per the specified, referenced construction code or standard.
- Basic understanding of the requirements of the codes, standards, and specifications related to qualifying and certifying welding inspection personnel.
Visual Inspection Techniques
8
Visual Inspection Techniques
8
- Minimum comprehension and understanding with identifying common types of discontinuities in butt, T-, corner, lap, and parallel (edge) joints in accordance with AWS B1.10 and AWS 3.0.
- Minimum comprehension and understanding of weld and basemetal discontinuities of common welding processes
- Minimum comprehension, understanding, and proper use of the various examination tools and gauges commonly employed in visual welding examination.
- Basic Understanding of quality control programs and the importance of visual examinations performed during all phases of fabrication, repair, and manufacturing.
- *Basic understanding and identification and assessment techniques for material discontinuities, including surface conditions
- *Basic Understanding of joint fit-up, alignment, and surface quality using appropriate instruments and tools.
- *Basic Understanding of adherence to Welding Procedure Specifications, monitoring and inspecting welding operations
- Note: *competencies above should be evaluated and modified to reference specific industry requirements per specific industry standards and engineering criteria related to the employer/sponsor.
Nondestructive and Mechanical Testing Methods
5
Nondestructive and Mechanical Testing Methods
5
- Understand the advantages and limitations of nondestructive examination methods for detecting discontinuities.
- Basic understanding of the most common nondestructive examination methods, Visual Testing (VT), Liquid Penetrant testing (PT), Magnetic Particle Testing (MT), Radiographic Testing (RT), and Ultrasonic Testing (UT).
- Minimum comprehension and understanding with NDE reports and documentation related to examination results and findings
- Minimum comprehension and understanding with requirements for guided bend test specimen preparation, test parameters, testing procedures, bend radius requirements, and applicable acceptance criteria per the specified, referenced construction code or standard.
- Basic understanding of employer/sponsor specified standards for nondestructive, mechanical, destructive, and related testing methods required within specific industry as described in contract documents.
Welding Documentation and Reporting
10
Welding Documentation and Reporting
10
- Understand and interpret contract documents defining the scope of work, fabrication, assembly, and welding requirements per the specified QC system procedure.
- Understand and apply both the International System of Units (SI) and U.S. Customary Units
- Comprehension of crafting written reports and inspection details essential to convey a clear, concise, and comprehensive message to the end user
- Minimum comprehension and understanding of methods for identifying nonconforming materials, parts, or components that have been examined per the specified QC system procedure.
- Minimum comprehension and understanding of standard symbols within AWS A2.4, Standard Symbols for Welding, Brazing, and Nondestructive Examination
- Minimum comprehension and understanding of welding terminology defined in AWS A3.0M/A3.0, Standard Welding Terms and Definitions, Including Terms for Adhesive Bonding, Brazing, Soldering, Thermal Cutting, and Thermal Spraying
- Minimum comprehension and understanding with producing and recording images of visual inspection findings related to reporting and documentation per the specified QC system procedure.
- Minimum comprehension and understanding in materials inspection documentation, materials certification, and mill test reports per the specified QC system procedure.
- Minimum comprehension and understanding in verifying current NDE personnel qualifications, equipment calibrations, and procedures per the specified QC system procedure.
- Minimum comprehension and understanding with weld repair inspections and related documentation or reporting per the specified QC system procedure.
Welder Performance Qualification
9
Welder Performance Qualification
9
- Understand Welder Performance Qualification Record variables
- Understand the role of contractors and their responsibility to comply with the qualification requirements of codes relative to WPSs, welders, welding operators and tack welders
- Understand the importance of verifying that all welders are qualified before they begin welding on the project
- Understand the requirements for welder qualification, including the welding positions, materials, and thicknesses for which a welder is qualified
- Understand the requirements for the types of tests, test methods, and acceptance criteria outlined within specific codes for welder qualification
- Understand the requirements and criteria for the retests during welder qualification
- Minimum comprehension and understanding in the terms and concepts of qualification to a standard, certification by an organization, maintenance of qualifications and certifications, and AWS Accredited Testing Facilities
- Understand the Performance Qualification Variables, the qualification limits for welders and welding operators, and changes exceeding limits requiring requalification
- Minimum comprehension and understanding in the qualification requirements and limitation variables for tack welders.
Welding Procedure Specifications
6
Welding Procedure Specifications
6
- Understand the procedure qualification record (PQRs) relationship and variables used to qualify a welding procedure specification (WPS)
- Understand the criteria for prequalification of welding procedure specifications (WPSs)
- Minimum comprehension and understanding in the criteria for the Qualification of WPSs required by code to provide assurance that the production welding to be performed will provide the strength, ductility, and toughness required by the design
- Minimum comprehension and understanding with essential and nonessential variables related to WPS qualification and qualified ranges and criteria for changes in parameters, beyond those specified on the written welding procedure specification
- Understand the purpose of the combination of qualified or prequalified joint welding procedures and the limitations of essential variables applicable
- Ability to review a WPS to determine if it qualifies for the production welding being performed with regard to welding process, base metal(s), filler metal(s), etc.
Safety and Health
3
Safety and Health
3
- Minimum comprehension and certification attainment to applicable local, state, and federal regulatory agencies required within work environment
- Understand organization specific safety program requirements and policies prior to inspection within a company facility
- Minimum understanding of hot work and enclosed entry requirements.
Communication and Documentation
5
Communication and Documentation
5
- Understand proper documentation, including the maintenance of records related to welding procedures, welder qualifications, and inspection reports.
- Minimum comprehension and understanding with project schedules and deadlines for completion of various phases of work.
- Minimum comprehension and understanding in regularly evaluating and communicating the quality of the welds produced by each welder, welding operator, and tack welder
- Minimum comprehension and understanding in best practices for recordkeeping, confidentiality, and document retention practices for sensitive or secure information
- Minimum comprehension and understanding in traceability of documentation related to welding, fabrication, assembly, consumables, materials, etc.
AWS Certification Preparation
5
AWS Certification Preparation
5
- Understand responsibilities, ethics, and duties of an AWS Certified Welding Inspector and the CWI program per AWS QC1 and B5.1
- Understand levels of certification within the CWI and accompanying endorsements offered by AWS
- Understand the Certified Welding Inspector (CWI) credential application process, including vision test requirements, the combination of qualifying education and work experience, and supporting documentation
- Understand the examination process, requirements, scoring metrics, and retesting criteria
- Understand renewal and certification maintenance requirements.
Related Instruction Content
Training Provider(s):
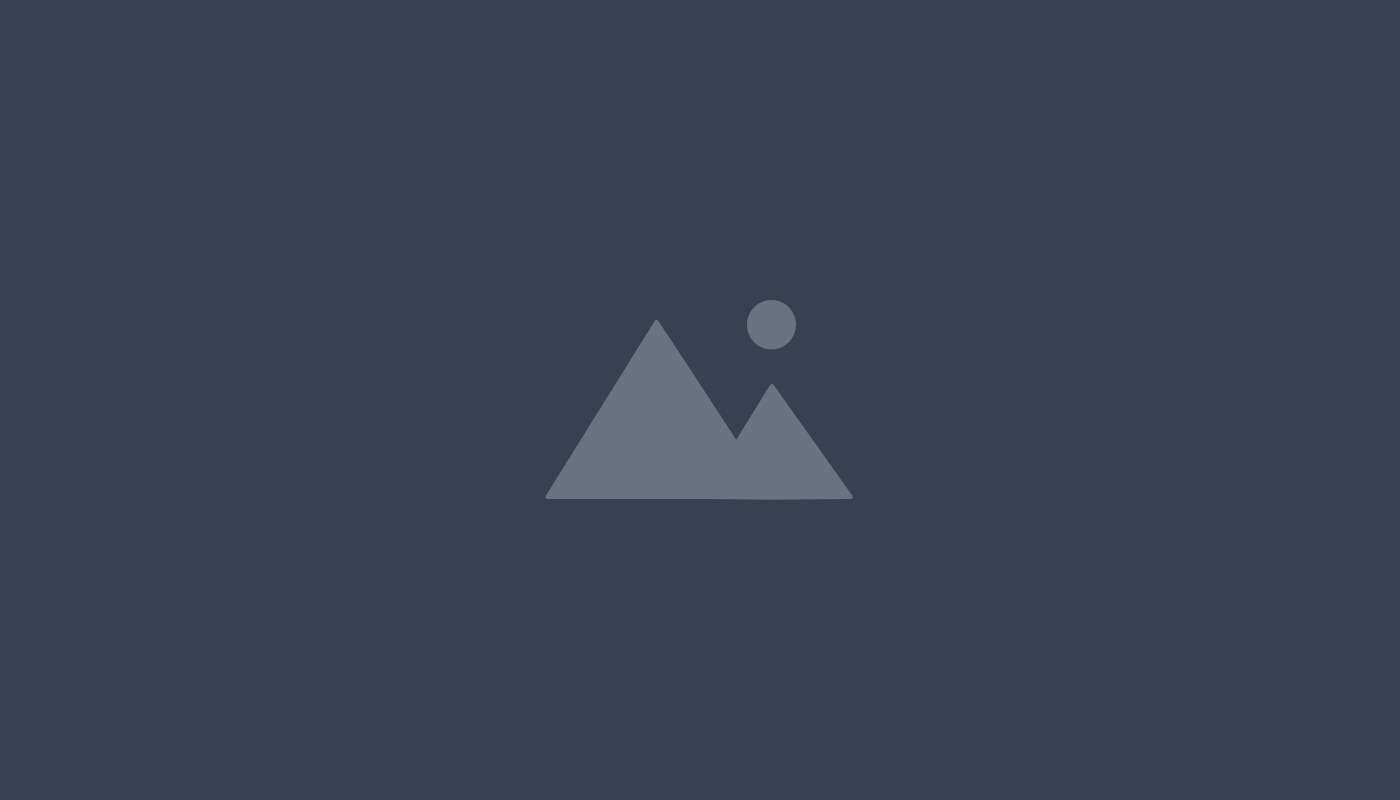
American Welding Society
440
RI hours
Industrial/Construction Safety and Safe Work Practices (OSHA/MSHA, etc.)
40
Industrial/Construction Safety and Safe Work Practices (OSHA/MSHA, etc.)
40
Introduction to Thermal Cutting and Gouging
10
Introduction to Thermal Cutting and Gouging
10
Welding for Inspection and Quality Personnel
44
Welding for Inspection and Quality Personnel
44
Weld Joint Design and Preparation
20
Weld Joint Design and Preparation
20
Fabrication Math I
18
Fabrication Math I
18
Fabrication Math II
15
Fabrication Math II
15
Safety in Welding
10
Safety in Welding
10
Metallurgy I
10
Metallurgy I
10
Metallurgy II
10
Metallurgy II
10
Welding Symbols & Drawings
12
Welding Symbols & Drawings
12
Welding Fundamentals I
14
Welding Fundamentals I
14
Welding Fundamentals II
7
Welding Fundamentals II
7
Welding Discontinuities and Defects
20
Welding Discontinuities and Defects
20
WPS/PQR Development and Fundamentals
12
WPS/PQR Development and Fundamentals
12
Precision Measurement, Tools, and Machines
8
Precision Measurement, Tools, and Machines
8
Introduction to Welding Codes and Standards
20
Introduction to Welding Codes and Standards
20
Welder Performance Qualification and Testing
20
Welder Performance Qualification and Testing
20
Destructive Testing for Welding Applications
16
Destructive Testing for Welding Applications
16
Welding Procedures and Specifications
16
Welding Procedures and Specifications
16
Material Identification and Testing
8
Material Identification and Testing
8
Quality Control in Welding
16
Quality Control in Welding
16
Introduction to non-destructive examination and testing
8
Introduction to non-destructive examination and testing
8
Visual Testing (Standard Specific AWS/API/ASME etc.)
24
Visual Testing (Standard Specific AWS/API/ASME etc.)
24
Inspection Reporting and Documentation
12
Inspection Reporting and Documentation
12
Applications of Penetrant Testing
8
Applications of Penetrant Testing
8
Applications of Magnetic Particle Testing
8
Applications of Magnetic Particle Testing
8
Introduction to Radiographic Testing
8
Introduction to Radiographic Testing
8
Principles of Ultrasonic Testing
8
Principles of Ultrasonic Testing
8
Introduction to Engineering and Design Concepts
8
Introduction to Engineering and Design Concepts
8
Technical Report Writing
8
Technical Report Writing
8
Industry certification & endorsements (AWS)
1
Industry certification & endorsements (AWS)
1