in on-the-job training and related instruction.
Pointer, Cleaner, Caulker
USDOL
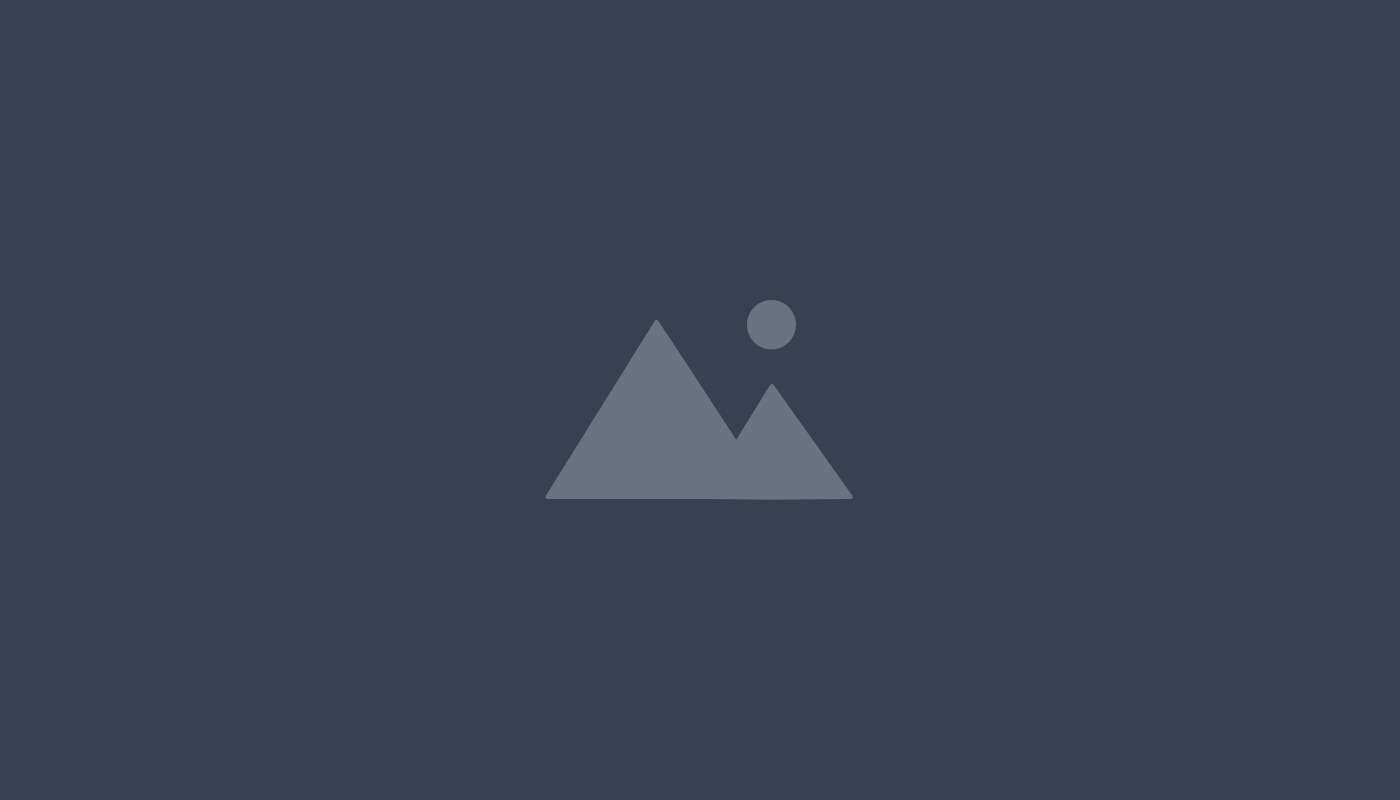
Work Process Content
On the Job Training
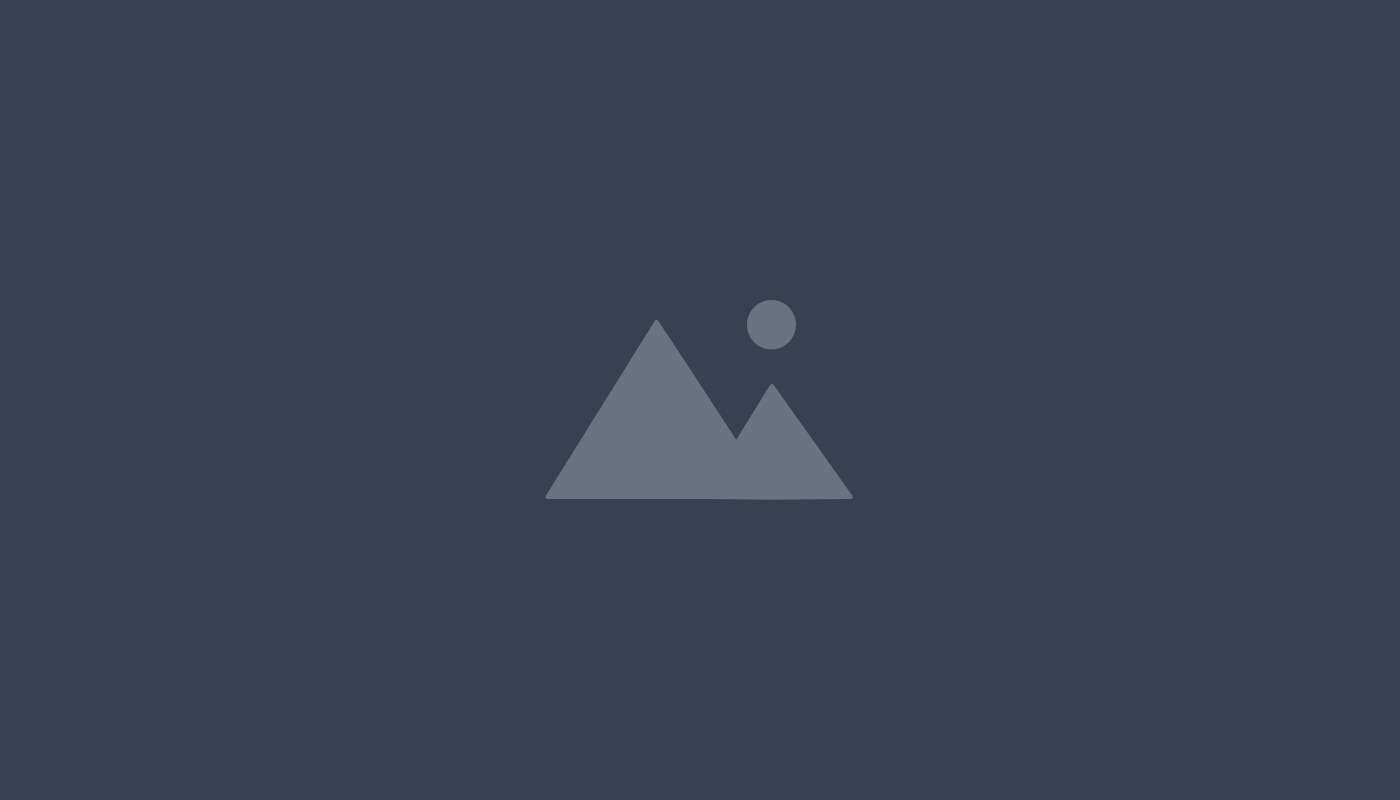
Use and Maintain Trade Related Tools and Equipment
0
150
Cleaning Exteriors of Buildings (Using 450 Methods/Materials per Job Specifications, Pressure Washing, Sandblasting, and Chemical Applications)
0
450
Pointing and Re-pointing of Masonry Joints
0
1.1K
Repairing Masonry Units (Natural and Manufactured Materials)
0
530
Application of Sealant (Using, Maintaining Related Tools and Equipment)
0
450
Repairing Concrete (Using Methods/Materials per Job Specifications)
0
680
Masonry Removal and Replacement (Using Natural and/or Manufactured Replacement Materials)
0
150
Weatherproofing and Waterproofing
0
150
Mold Making and Casting Replacement Masonry Elements
0
110
Patching Masonry Elements (Using Traditional and Modern Materials and Methods)
0
150
Welding, Certified and Required
0
200
Use and Maintenance of Hand Tools
98
Provided with the listed miscellaneous power tool, the worker must be able to demonstrate without error the proper use of each specific tool including, but not limited to:
- 2 or 3 pound mash hammer.
- Plugging chisel.
- Cold chisel.
- Concrete chisel.
- Brush.
- Straps.
- Lewis pins.
- Chain fall.
- Granite clamp.
- Pry bars.
- Well wheels.
- Wire/ synthetic rope.
- Debris bags/buckets/baskets .
- Follows supervisor's direction.
- Follows safety rules and requirements appropriate with this section.
- Follows other processes and procedures as required.
- Grinders
- Saws
- Chipping Hammers
- Drills
- Pneumatic.
- Vacuum.
- Electric hoists.
- Suction equipment.
- Follows supervisor's direction.
- Follows safety rules and requirements appropriate with this section.
- Follows other processes and procedures as required.
- Margin trowel.
- Gauging trowel.
- Brick trowel.
- Pointing trowel.
- Concrete trowel.
- Bucket trowel.
- Hawk board.
- Pointing tools.
- Slickers.
- Jointers.
- Levels.
- Rulers.
- Mason line and blocks.
- Masonry nails.
- Buckets.
- Follows supervisor's direction.
- Follows safety rules and requirements appropriate with this section.
- Follows other processes and procedures as required.
- Mixing drills/paddles.
- Power pointers.
- Power caulkers.
- Suction equipment.
- Power hoist.
- Follows supervisor's direction.
- Follows safety rules and requirements appropriate with this section.
- Follows other processes and procedures as required.
- Brushes.
- Scrapers.
- Sprayer.
- Wire Brush.
- Sponges.
- Rubbing stone.
- Follows supervisor's direction.
- Follows safety rules and requirements appropriate with this section.
- Follows other processes and procedures as required.
- Power washer/tips.
- Power pump sprayer.
- Abrasive blaster pot and nozzles.
- Orifice cleaner.
- Air compressor.
- Steam cleaner.
- Follows supervisor's direction.
- Follows safety rules and requirements appropriate with this section.
- Follows other processes and procedures as required.
- Trowels magnesium/steel.
- Miter rods/straight edge.
- Trowel leaf.
- Trowel square.
- Wood floats/sponge/floats/magnesium floats.
- Follows supervisor's direction.
- Follows safety rules and requirements appropriate with this section.
- Follows other processes and procedures as required.
- Cartridge gun.
- Sausage gun.
- Bulk gun.
- Slickers.
- Razor knife.
- Mixing tub/wheel barrows.
- Hoes.
- Water hose/nozzles.
- Pressure hose.
- Follows supervisor's direction.
- Follows safety rules and requirements appropriate with this section.
- Follows other processes and procedures as required.
- Caulking cutters.
- Electrical/ extension cords.
- Ground faults (GPIs).
- Generators.
- Follows supervisor's direction.
- Follows safety rules and requirements appropriate with this section.
- Follows other processes and procedures as required.
Cleaning Exteriors of Buildings
32
Provided the necessary and required materials, tools and equipment, the worker must be able to demonstrate without error the ability to clean the exterior of a building related to old work adhering to the following specific criteria:
- Identifies PPE equipment as needed.
- Checks scaffold for safety equipment/MSDS.
- Establishes a safety zone underneath the work area
- Establishes chemical controls, dykes and dams as necessary.
- Protects surrounding area.
- Mixes cleaning agent to water per the manufacturer's recommendations.
- Loads the scaffold with materials and equipment as required.
- Identifies the area to be cleaned.
- Pre tests cleaning solution on the area to be cleaned.
- Pre-wets the surface.
- Applies solution per specifications.
- Lets the solution stand for the prescribed amount of time, per specifications.
- Removes any remaining stains and residue.
- Rinses off cleaner.
- Neutralizes cleaning agent as necessary.
- Removes protection from surrounding areas.
- Properly disposes of leftover cleaning solution.
- Follows supervisor's direction.
- Follows safety rules and requirements appropriate with this section.
- Follows other processes and procedures as required.
- Identifies proper technique for cleaning old work.
- Demonstrates proper technique for the following: Soaker hoses;
- Demonstrates proper technique for the following: Spray bars;
- Demonstrates proper technique for the following: High pressure;
- Demonstrates proper technique for the following: Steam cleaning;
- Demonstrates proper technique for the following: Abrasive cleaning;
- Demonstrates proper technique for the following: Poultices;
- Demonstrates proper technique for the following: Latex cleaners: roll on, spray, brush;
- Demonstrates proper technique for the following: Soap and water;
- Follows supervisor's direction.
- Follows safety rules and requirements appropriate with this section.
- Follows other processes and procedures as required.
Masonry Units
47
Provided the necessary and required materials, tools and equipment, the worker must be able to demonstrate without error the ability to repair masonry units adhering to the following specific criteria:
- Identifies area to be pointed.
- Checks scaffold for safety equipment/MSDS.
- Establishes a safety zone underneath the work area.
- Identifies and demonstrates use of appropriate PPE.
- Removes mortar per the techniques required. Hammer and chisel;
- Removes mortar per the techniques required. Pneumatic tools;
- Removes mortar per the techniques required. Grinding/diamond blades or carborundum;
- Removes mortar per the techniques required. Chipping hammer;
- Removes mortar per the techniques required. Saw;
- Cleans joints and prepares the area for pointing.
- Pre-Hydrates the area.
- Allows water to absorb.
- Identifies proper mixing ratio per specs.
- Thoroughly mix the materials dry.
- Pre-hydrates mortar mixture.
- Adds remaining water to achieve desired consistency.
- Begins to re-point the joints in lifts as required.
- Re-points an area and finishes the joints with proper profile.
- When mortar is thumb print hard, removes excess tags and brushes down.
- Re-hydrates the wall as necessary.
- Cleans the wall with mild solution if required.
- Cleans adjacent area.
- Disposes of material properly.
- Follows supervisor's direction.
- Follows safety rules and requirements appropriate with this section.
- Follows other processes and procedures as required.
- Identifies area or units to be repaired.
- Checks scaffold for safety equipment/MSDS.
- Establishes a safety zone underneath the work area.
- Identifies and demonstrates use of appropriate PPE.
- Removes deteriorated area.
- Prepares area for installation including anchoring systems.
- Washes down to remove dust.
- Installs pins and anchors with adhesives as required.
- Mixes material according to manufacturer's instructions.
- Applies bonding agent or slurry coat as required by specs.
- Installs new material.
- When mortar is thumb print hard, removes excess material to fit profile.
- Demonstrates proper technique of repairing by use of a Dutchmen or patching material.
- Uses appropriate finishing technique(s) to match existing substrate.
- Re-hydrates as necessary.
- Coats or seals as required.
- Cleans adjacent area.
- Disposes of material properly.
- Follows supervisor's direction.
- Follows safety rules and requirements appropriate with this section
- Follows other processes and procedures as required.
Sealant
26
Provided the necessary and required materials, tools and equipment, the worker must be able to demonstrate without error the ability to apply sealant adhering to the following specific criteria:
- Identifies area or units.
- Checks scaffold for safety equipment/MSDS.
- Establishes a safety zone underneath the work area.
- Identifies and demonstrates use of appropriate PPE.
- Identifies and contains any hazardous materials in the removal process.
- Removes old sealant method. Caulk cutters;
- Removes old sealant method. Utility knives;
- Removes old sealant method. Hammer and chisel;
- Removes old sealant method. Grinders;
- Removes residue using appropriate solvent per specs.
- Tapes joints if required.
- Identifies proper bond breaker/backer rod.
- Installs bondbreaker/backer rod to proper depth.
- Installs primer if recommended.
- Mixes material per the specs as required.
- Applies material to specifications using one of the following techniques: Cartridge gun;
- Applies material to specifications using one of the following techniques: Bulk gun;
- Applies material to specifications using one of the following techniques: Electric caulk gun;
- Applies material to specifications using one of the following techniques: Battery operated caulk gun;
- Applies material to specifications using one of the following techniques: Sausage bulk gun;
- Tools joint to uniform profile per specs.
- Cleans adjacent area.
- Disposes of material properly.
- Follows supervisor's direction.
- Follows safety rules and requirements appropriate with this section.
- Follows other processes and procedures as required.
Concrete
25
Provided the necessary and required materials, tools and equipment, the worker must be able to demonstrate without error the ability to repair concrete adhering to the following specific criteria:
- Identifies area or units to be repaired.
- Checks scaffold for safety equipment/MSDS.
- Establishes a safety zone underneath the work area.
- Identifies and demonstrates use of appropriate PPE.
- Removes loose and deteriorated substrates, min. one inch of clearance surrounding rebar.
- Prepares area as necessary.
- Uses appropriate method of prepping rebar: Abrasive blasting;
- Uses appropriate method of prepping rebar: Wire brushing;
- Uses appropriate method of prepping rebar: Grinder with wire brush;
- Install rebar coating according to specs.
- Applies bonding agent if required.
- Builds forms around substrate if required.
- Applies epoxy if required.
- Mixes repair material per specs.
- Installs material.
- Vibrate repair material if needed.
- Screeds excess mortar.
- If forms are used, remove and fill in voids if necessary.
- Uses proper finishing techniques to match adjacent area.
- Hydrates concrete being replaced.
- Cleans adjacent area.
- Disposes of material properly.
- Follows supervisor's direction.
- Follows safety rules and requirements appropriate with this section.
- Follows other processes and procedures as required.
Fireproof Caulking Systems
15
Provided the necessary and required materials, tools and equipment, the worker must be able to demonstrate without error the ability to apply fireproof caulking systems adhering to the following specific criteria:
- Identifies area where fireproofing is to be applied.
- Identifies proper system of fireproofing or intumescent caulk to use.
- Checks scaffold for safety equipment/MSDS.
- Establishes a safety zone underneath the work area.
- Identifies and demonstrates use of appropriate PPE.
- Cleans areas to be sealed of all grease, oil and loose material.
- Insures that any angular spaces between the through penetration and the opening must be within manufacturer's defined limits.
- When mineral wool is required, it is cut oversized and packed tightly into the space. between the opening and the surface.
- Packing is positioned to allow for correct depth of fill material to be installed.
- Applies using suitable standard or bulk loading gun, hand trowel or spray system to avoid gaps, voids and seams.
- Surface should be smoothed using a damp knife or spatula to leave a neat, sealed finish.
- Details of testing the constructions according to the UL fire resistance
- Follows supervisor's direction.
- Follows safety rules and requirements appropriate with this section.
- Follows other processes and procedures as required.
Fire Barrier Mortar
21
Provided the necessary and required materials, tools and equipment, the worker must be able to demonstrate without error the ability to install fire barrier mortar adhering to the following specific criteria:
- Identifies area where fireproofing is to be applied.
- Identifies proper system of fireproofing to use.
- Checks scaffold for safety equipment/MSDS.
- Establishes a safety zone underneath the work area.
- Identifies and demonstrates use of appropriate PPE.
- Demonstrates proper technique for cleaning items from any dirt, debris, grease or oil.
- Removes cable ties within 2 feet of either side of the cable penetration.
- Installs damming if required for floor openings.
- Masks the edge and end of penetrating items.
- Mixes mortar per manufacturer's recommendations.
- Moistens the opening with a spray bottle or hand brush.
- Immediately places mortar filling the most difficult areas to reach first
- Presses mortar against the side of the bonding surface.
- Smooth mortar off and flushes the wall or floor with water.
- Remove any masking from protected adjacent areas.
- Cleans adjacent area.
- Disposes of material properly.
- Details of testing the constructions according to the UL fire resistance
- Follows supervisor's direction.
- Follows safety rules and requirements appropriate with this section.
- Follows other processes and procedures as required.
Scaffolding and Rigging
99
Provided the necessary and required materials, tools and equipment, the worker must be able to demonstrate without error the ability to erect tubular scaffolding and rigging adhering to the following specific criteria:
- Identifies areas where work is to be performed.
- Inspects for overhead electrical lines.
- Identifies appropriate rigging tools and equipment. Adjustable wrenches;
- Identifies appropriate rigging tools and equipment. Torque wrench;
- Identifies appropriate rigging tools and equipment. 1/2 " ratchet set;
- Identifies appropriate rigging tools and equipment. Zip/cable ties;
- Identifies appropriate rigging tools and equipment. Screwdriver;
- Personal Fall Arrest System: Full body harness;
- Personal Fall Arrest System: Shock absorbing lanyards with locking snap hooks;
- Personal Fall Arrest System: Rope grabs for Synthetic rope for life line - 5/8"s;
- Personal Fall Arrest System: Mechanical attachment device;
- Personal Fall Arrest System: Chafing protection;
- Rigging Equipment A: Cornice hook with standoff;
- Rigging Equipment A: Parapet clamp;
- Rigging Equipment A: Boom/outrigger/look out beams;
- Rigging Equipment A: Stanchion truss;
- Rigging Equipment A: Scaffold frame as required;
- Rigging Equipment A: Mud sills;
- Rigging Equipment A: Base plates/leveling jacks;
- Rigging Equipment A: Header beams;
- Rigging Equipment A: Saddle/shoulder plates;
- Rigging Equipment A: Counterweights;
- Rigging Equipment A: Extension collars;
- Rigging Equipment A: Wire ropes suspension;
- Rigging Equipment A: Wire ropes - tie backs;
- Rigging Equipment A: Slings/pendants;
- Rigging Equipment B: Cable winder.
- Rigging Equipment B: Rope fall lines/block and tackle/%" manila rope or stronger.
- Rigging Equipment B: Heavy duty electric cord with tvvist lock connection.
- Rigging Equipment B: Turn buckle.
- Rigging Equipment B: Thimbles.
- Rigging Equipment B: Shackles or clevis.
- Rigging Equipment B: Crosby clamps or fist grips.
- Rigging Equipment B: Work Platform.
- Platform or stage: Stirrups/ cradle iron;
- Platform or stage: Lifting mechanisms;
- Platform or stage: Rails and posts;
- Platform or stage: Kick boards and screens;
- Single point suspended cage. Boatswain's chair:
- Single point suspended cage. Rope fall;
- Single point suspended cage. Repelling device;
- Single point suspended cage. Electric boatswain's chair;
- Establishes a safety zone underneath the work area.
- Identifies suspension system to be used.
- Identifies and confirms adequate tie backs and anchoring points.
- Identifies tie back points.
- Safely transports appropriate equipment to staging point.
- Installs edge and fall protection as required.
- Sets up suspension system.
- Lowers suspension lines.
- Connects to suspension system with a minimum of 3 cable clamps properly spaced using thimble and shackle/clevis and torques to manufacturer's specifications.
- If welding use an insulated thimble.
- Tie back suspension system to structurally sound anchor point per requirements.
- Lower independent safety lines and anchor to independent structure per requirements.
- Lower electric cord.
- Protect all lines from chafing.
- Assemble platform staging per manufacturer's requirement.
- Install guard rail, end rails, kick boards and netting as required.
- Attach proper electric cord restraints.
- Attach suspension cables to proper lifting mechanism.
- Performs and documents load test on scaffold system according to safety requirements.
- Re-check all connections and secure as necessary.
- Follows supervisor's direction.
- Follows safety rules and requirements appropriate with this section.
- Follows other processes and procedures as required.
- Identifies areas where work is to be performed.
- Identifies appropriate rigging tools and equipment .
- Establishes a safety zone underneath the work area.
- Lays out scaffold for efficient use and proper distance from structure.
- Performs ground test to ensure stability for required standards.
- Inspects for overhead electrical lines.
- Checks for underground voids and support as required.
- Gathers necessary scaffold components: Frames;
- Gathers necessary scaffold components: Braces;
- Gathers necessary scaffold components: Mud sills;
- Gathers necessary scaffold components: Screw jacks and base plates;
- Gathers necessary scaffold components: Guard rails and posts;
- Gathers necessary scaffold components: Kick boards;
- Gathers necessary scaffold components: Side arm bracket/Outriggers;
- Gathers necessary scaffold components: Scaffold boards or planks;
- Gathers necessary scaffold components: Coupling pins and locking devices;
- Gathers necessary scaffold components: Tie-in materials and stiff arms/diagonal supports as required;
- Gathers necessary scaffold components: Putlog and hangers;
- Gathers necessary scaffold components: #9 tie wire;
- Install mud sills.
- Install screw jacks/base plates.
- Center screw jacks/base plates on mud sills and attach.
- Assemble frames and attach braces.
- Check for level and plumb and correct as necessary.
- Square the scaffold.
- Repeat steps for each frame as required.
- Attach tie in points as the work progresses per requirements.
- Fully plank each work area.
- Install access.
- Install fall protection and falling object protection.
- Uses PPE and fall protection devices as required.
- Follows supervisor's direction.
- Follows safety rules and requirements appropriate with this section.
- Follows other processes and procedures as required.
Masonry
22
Provided the necessary and required materials, tools and equipment, the worker must be able to demonstrate without error the ability to remove and replace masonry adhering to the following specific criteria:
- Identifies areas where work is to be performed.
- Checks for safety equipment.
- Identifies appropriate tools and equipment for the job assigned.
- Establishes a safety zone underneath the work area.
- Identifies and demonstrates use of appropriate PPE.
- Set up debris removal system.
- Saw cut affected area.
- Remove deteriorated masonry units and support work area as necessary.
- Clean the area of all dust and loose materials.
- Flash and install damp proofing per specifications.
- Mix mortar per specs.
- Place replacement material in work area.
- Hydrate replacement area as needed.
- Allow water to absorb.
- Install units to match adjacent area and anchor per specs.
- Finish the joints to match existing work
- Re-hydrated replacement area for curing.
- Cleans adjacent area.
- Disposes of material properly.
- Follows supervisor's direction.
- Follows safety rules and requirements appropriate with this section.
- Follows other processes and procedures as required.
Waterproofing and Weatherproofing
104
Provided the necessary and required materials, tools and equipment, the worker must be able to demonstrate without error the ability to waterproof and weatherproof above grade using horizontal applications adhering to the following specific criteria:
- Identifies areas where work is to be performed.
- Checks for safety equipment.
- Identifies appropriate tools and equipment for the job assigned.
- Establishes a safety zone for the protection of the trench.
- Ensures that the shoring meets the necessary requirements.
- Identifies and demonstrates use of appropriate PPE.
- Clean and prep the area to be waterproofed.
- Make sure area is dry to receive application of material.
- Applies primers, if required, according to manufacturer's specifications.
- Applies adhesive according to manufacturer's specifications.
- Installs membrane ensuring that no air is trapped behind it.
- Installs termination bar at the proper location according to recommendations.
- Installs protection board if required.
- Installs drainage system per specs.
- Cleans adjacent area.
- Disposes of material properly.
- Follows supervisor's direction.
- Follows safety rules and requirements appropriate with this section.
- Follows other processes and procedures as required.
- Identifies areas where work is to be performed.
- Checks for safety equipment.
- Identifies appropriate tools and equipment for the job assigned.
- Establishes a safety zone for the protection of the trench.
- Confirms that the shoring meets the necessary requirements.
- Identifies and demonstrates use of appropriate PPE.
- Cleans and preps the area to be waterproofed.
- Makes sure area is dry to receive application of material.
- Sets up equipment appropriate to application process.
- Applies material according to manufacturer's specs.
- Installs protection board if required.
- Installs drainage system per specs.
- Cleans adjacent area.
- Disposes of material properly.
- Follows supervisor's direction.
- Follows safety rules and requirements appropriate with this section.
- Follows other processes and procedures as required.
- Identifies areas where work is to be performed.
- Checks for safety equipment.
- Identifies appropriate tools and equipment for the job assigned.
- Establishes a safety zone for the protection of the trench.
- Confirms that the shoring meets the necessary requirements.
- Identifies and demonstrates use of appropriate PPE.
- Cleans and preps the area to be waterproofed.
- Mixes cementitious product according to manufacturer's specs.
- Hydrate area to be waterproofed.
- Trowel on material per job specifications.
- Cleans adjacent area.
- Disposes of material properly.
- Follows supervisor's direction.
- Follows safety rules and requirements appropriate with this section.
- Follows other processes and procedures as required.
- Identifies areas where work is to be performed.
- Checks for safety equipment.
- Identifies appropriate tools and equipment for the job assigned.
- Establishes a safety zone.
- Identifies and demonstrates use of appropriate PPE.
- Clean and prep the area to be waterproofed.
- Protects adjoining areas from overspray.
- Roll, spray or brush on according to manufacturer's specs.
- Cleans adjacent area.
- Disposes of material properly.
- Follows supervisor's direction.
- Follows safety rules and requirements appropriate with this section.
- Follows other processes and procedures as required.
- Identifies areas where work is to be performed.
- Checks for safety equipment.
- Identifies appropriate tools and equipment for the job assigned.
- Establishes a safety zone.
- Identifies and demonstrates use of appropriate PPE.
- Cleans and preps the area to be waterproofed.
- Mixes cementitious product according to manufacturer's specs.
- Hydrates area to be waterproofed.
- Trowels, sprays, brushes or rolls on material per job specifications.
- Cleans adjacent area.
- Disposes of material properly.
- Follows supervisor's direction.
- Follows safety rules and requirements appropriate with this section.
- Follows other processes and procedures as required.
- Identifies areas where work is to be performed.
- Checks for safety equipment.
- Identifies appropriate tools and equipment for the job assigned.
- Establishes a safety zone
- Identifies and demonstrates use of appropriate PPE.
- Cleans and preps the area to be waterproofed.
- Mixes product according to manufacturer's specs.
- Sprays, brushes or rolls on material per job specifications.
- Cleans adjacent area.
- Disposes of material properly.
- Follows supervisor's direction.
- Follows safety rules and requirements appropriate with this section.
- Follows other processes and procedures as required.
- Identifies areas where work is to be performed.
- Checks for safety equipment.
- Identifies appropriate tools and equipment for the job assigned.
- Establishes a safety zone.
- Identifies and demonstrates use of appropriate PPE.
- Cleans and preps the area to be waterproofed.
- Mixes product according to manufacturer's specs if necessary.
- Apply material per job specifications.
- Cleans adjacent area.
- Disposes of material properly.
- Follows supervisor's direction.
- Follows safety rules and requirements appropriate with this section.
- Follows other processes and procedures as required.
Mold Making
17
Provided the necessary and required materials, tools and equipment, the worker must be able to demonstrate without error the ability to make molds on-site adhering to the following specific criteria:
- Identifies areas where work is to be performed.
- Checks for safety equipment.
- Identifies appropriate tools and equipment for the job assigned.
- Establishes a safety zone.
- Identifies and demonstrates use of appropriate PPE.
- Cleans and preps the area and masks adjacent area.
- Seals casting piece.
- Applies releasing agent to casting piece.
- Mixes product according to manufacturer's specs.
- Sprays or brushes on material per job specifications.
- Applies multiple coats as required.
- Builds reinforcement for the mold as needed.
- Allows cure time per manufacturer's specs.
- Pulls mold.
- Follows supervisor's direction.
- Follows safety rules and requirements appropriate with this section.
- Follows other processes and procedures as required.
Mold Casting
29
Provided the necessary and required materials, tools and equipment, the worker must be able to demonstrate without error the ability to cast molds in a shop adhering to the following specific criteria:
- Builds casting box.
- Mixes casting material per manufacturer's specs.
- Sprays release on casting box.
- Pours material into the mold and allows to cure per manufacturer's specs.
- Finishes casting to match existing surface.
- Installs with proper anchorage according to specs.
- Follows supervisor's direction.
- Follows safety rules and requirements appropriate with this section.
- Follows other processes and procedures as required.
- Checks for safety equipment.
- Identifies appropriate tools and equipment for the job assigned.
- Establishes a safety zone.
- Identifies and demonstrates use of appropriate PPE.
- Builds mold containment box.
- Seals edges.
- Seals casting piece.
- Applies releasing agent to mold and box.
- Mixes mold product according to manufacturer's specs.
- Pours material per job specifications.
- Allows mold to cure per manufacturer's specs.
- Removes original stone from box.
- Mixes casting material per manufacturer's specs.
- Sprays releasing agent on piece to be cast.
- Pours material into the mold and allows to cure per manufacturer's specs.
- Finishes casting to match existing surface.
- Installs with proper anchorage according to specs.
- Follows supervisor's direction.
- Follows safety rules and requirements appropriate with this section.
- Follows other processes and procedures as required.
Masonry Elements
19
Provided the necessary and required materials, tools and equipment, the worker must be able to demonstrate without error the ability to patch masonry elements adhering to the following specific criteria:
- Identifies area or units to be repaired.
- Checks scaffold for safety equipment/MSDS.
- Establishes a safety zone underneath the work area.
- Identifies and demonstrates use of appropriate PPE.
- Removes loose and deteriorated substrates.
- Prepares edges of area to be patched.
- Washes down for appropriate patching.
- Installs anchors if required according to job site specs.
- Mixes material according to manufacturer's specs.
- Applies slurry or bonding agent if recommended.
- Applies material.
- Finishes profile to match adjacent area.
- Allows material to cure the appropriate time.
- Cleans adjacent area.
- Disposes of material properly.
- Applies any coatings or sealants per the job site specs.
- Follows supervisor's direction.
- Follows safety rules and requirements appropriate with this section.
- Follows other processes and procedures as required.
Related Instruction Content
Training Provider(s):