in on-the-job training and related instruction.
Quality Inspector
Anonymous
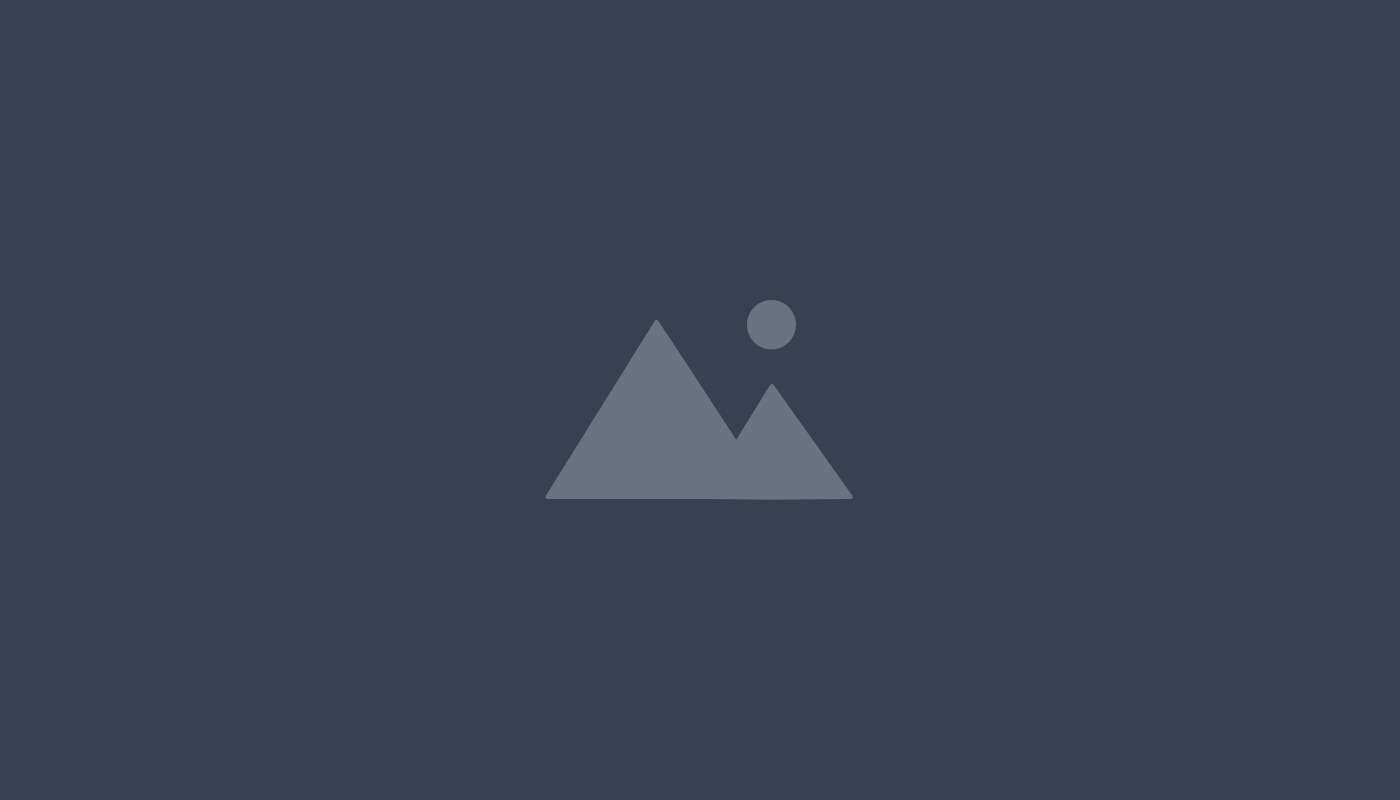
Work Process Content
On the Job Training
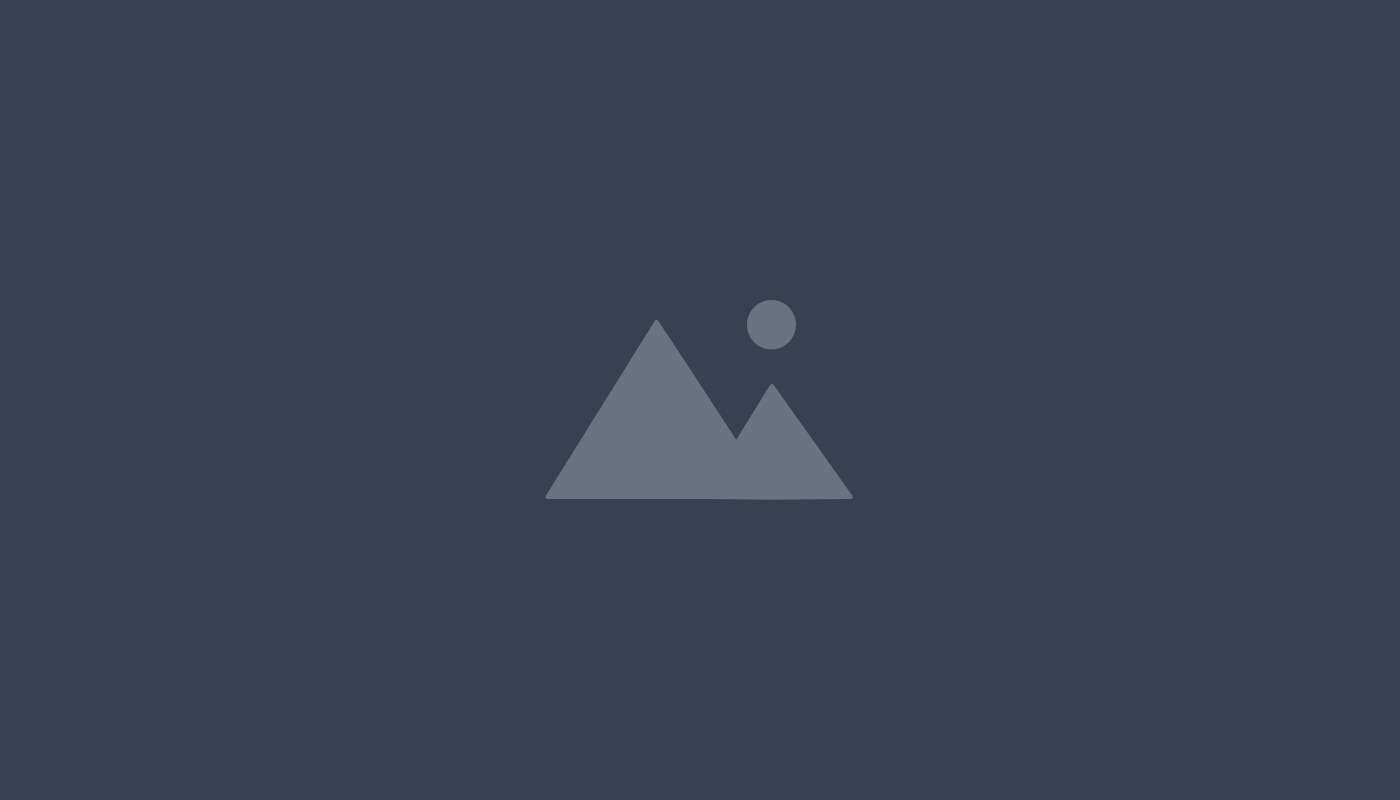
Shop Practices
0
80
a) Hazards of job b) Cost and maintenance of equipment c) Necessity for cleanliness and order d) OSHA guidance e) PPE personal protective equipment f) Power and hand tool safety g) Hazardous materials h) Computer systems and data processing
Procedures and Forms
0
140
a) Acceptance and rejection stamping b) Parts identification markings c) Recommendation for rework d) Salvage recommendation e) Scrap reports f) In-Tolerance or O.O.T. Out of Tolerance condition of machined parts reports g) Conformance reports. h) Non-Conformance reports. i) Computer use and understanding. j) Word processing, reports and CAD file management
Inspector Calculations Shop Math
0
400
a) Basic arithmetic operations b) Fractions, decimals and percentages c) Basic algebra d) Basic geometry e) Basic trigonometry f) Calculating features of part g) Calculating from datum’s h) Primary datum, secondary datum, tertiary datum i) Calculations with holes, slots, tabs, bosses and shafts j) Surface as datum k) Understanding true position l) Calculating offsets and dimensions
Blueprints and Drawings
0
450
a) Reading blueprints b) Blueprints notes and dimensions c) Basic drawings and layouts d) Isometric views e) Scale of views, sections and revisions f) CAD/CAM g) Part tolerancing h) Geometric Dimensioning & Tolerancing GD&T i) Symbols, ID datum features, control datum features j) ASME Y14.5-2009 standard
Understanding GD&T
0
400
a) Straightness b) Flatness c) Circularity d) Cylindricity e) Perpendicularity f) Parallelism g) Angularity h) Profile of a line i) Profile of a surface j) Position k) Circular runout l) Total runout m) Concentricity n) Symmetry o) Surfaces p) Planes q) Spheres r) Cylinders
Metrology Use Of Measuring Hand Gages
0
80
a) Micrometers (external, internal, depth) thread b) Height gauge, vernier calipers, dial indicators c) Surface plate, angle plate, V-block, size blocks, sinebar d) Machinist level e) Vernier caliper
Metrology
0
200
a) Accuracy and Precision b) Storage and handling c) Tool calibration d) Surface measurement e) Optical comparator f) CMM Coordinate Measuring Machine – benchtop DCC g) CMM Coordinate Measuring Machine – portable arm
Measurement Planning
0
620
a) Determine error budget b) Optimize equipment stations (including fixturing) c) Determine data collection/sampling d) Plan reference system e) Determine order of measurement f) Estimate data collection time g) Determine naming conventions h) Identify safety requirements i) Plan coordinate systems j) Plan traceability and documentation k) Create a documentation plan l) Develop a mitigation plan for environmental factors m) Plan subject temperature compensation strategy n) Maintain equipment o) CMM measure manager and edits p) CMM measurement of points and point-clouds q) CMM probe compensation r) CMM measurement of planes, lines, circles, slots, cylinders. s) CMM editing features
Performing Measurement Operations
0
620
a) Verify calibration status b) Setup equipment (including fixturing) c) Install reference features d) Perform in-situ equipment check e) Determine and mitigate environmental influence on instrument f) Measure reference features to create a coordinate system g) Measure features of interest h) Re-check reference features i) Manage temperature influence on part (scale) j) Perform device move if required k) Perform quality assurance of data set l) Manage measurement data m) Manage temperature influence on part (scale) n) Perform device move if required o) Perform quality assurance of data set p) Manage measurement data q) Establish traceability r) CMM alignments and transformations s) CMM feature-based alignments t) CMM AutoAlign u) CMM work coordinates v) CMM reporting w) CMM MBD manager and GD&T x) CMM inspect y) CMM analysis manager
Analyzing Data and Ethics
0
300
a) Compare measurement data to design specifications b) Evaluate GD&T c) Combine and evaluate alignment of multiple data sets d) Register data sets to known reference system e) Optimize data f) Construct geometry g) Calculate uncertainty and its impact on measurement task h) Describe statistical process control (SPC)
Preliminary & Final Inspection (Visual)
0
40
a) Material flaws b) Nicks, scratches, burns, toolmarks finish c) Identification markings d) Quality review procedures
Optical Inspection
0
100
a) Set-up, use and care of optical comparators
In Process Inspection
0
120
a) Job Scheduling b) Application of Shop Math c) Application of blueprint reading d) Inspection and measurement process e) Reporting conformity to manufacturers' instructions and specifications f) Documentation processing and archival
Final Inspection Reports
0
55
a) Conformity to specifications, prints, drawings and CAD files. b) Reporting as-found dimensions (length, ID, OD, etc.)
Related Instruction Content
Training Provider(s):
Applied Mathematics
16
Units of Measurement, Blueprints, Math Fundamentals, Algebra, Geometry, Trigonometry, and Statistics
Inspection
27
Basics of Tolerance, Blueprint Reading and GD & T, Measuring System Analysis, Caliberation Fundamentals, Hole and Thread Standards and Inspection, Surface Texture and Inspection, Inspecting with Optical Comparators and CMMS, Calibration and Documentation, and In-line Applications
Metal Cutting
28
Metal Cutting Safety, Processes, Machine Tools, Materials and Fluids Overview, Cutting Theory, and Grade and Insert Selection, Safety for Metal Cutting and Cutting Fluid, Cutting, Deburring Processes, and Optimizing Tool Life
Abrasives
9
Safety, Theory, Grinding Processes, Finishing Processes and Grinding Metal and Material Overview
CNC Machining
7
Basics of CNC Lathe and Mill Machines and their Control Panel Functions
Manual Machining
15
Manual Mill and Engine Lathe Basics, Benchwork and Layout Operations, and Engine Lathe Threading and Taper Turning
Materials
15
Introduction to Physical and Mechanical Properties, Metals and Alloys, Heat Treatment, Hardness Testing, and Polymer Composite Processes
Quality
13
SPC Overview, Customer Service, ISO 9000/9001, Process and Production System Design and Development, Supply Chain Management, and Internal Audits
Lean
24
Total Quality Management Overview, Six Sigma, Lean Manufacturing Overview, Continuous Process Improvement, Product and Process Design, and Value Stream Mapping
Composites
4
Composite Inspection and Defect Prevention, Safety and Overview of Composite Processing
Rigging
1
Rigging Inspection and Safety
Additive Manufacturing
7
Additive Manufacturing Safety, Basics, Supply Chain, Methods and Materials
Electrical Systems
1
Safety for Electrical Work
Fasteners
1
Safety for Assembly
Hydraulics & Pneumaics
3
Safety for Hydraulics and Pneumatics and Control Valves
Mechanical Systems
1
Safety for Mechanical Work
Press Brake
1
Press Brake Safety
Safety
13
Intro to OSHA, Respiratory, Fire, Arc Flash and Tool Safety, Infection Safety and Prevention, Truck and Device Safety, and Enviromental Safety Hazards
Soldering
1
Safety for Soldering
Stamping
1
Stamping Safety
Welding
7
Welding Processes, Safety Essentials, Oxyfuel Welding and Electrical Safety, and Fabrication Process
Adhesives
1
Basics of the Bonding Process
Coatings
1
Processes for Applying Coatings
Shop Essentials
3
Manufacturing Process Applications: Part I and II
Composites
1
Repair Methods for Composites
Motor Controls
7
Deceleration and Acceleration Methods, Motor Symbols and Diagrams, Control Devices, and Logic and Line Diagrams
PLC's
3
Basic PLC Programming, Diagrams and Programs
Robotics
21
Intro to Robotics, Robot Components, Applications, Maintenance, Safety and Troubleshooting
Shop Essentials
1
Concepts of Calculus
Workforce Essentials
1
Manufacturing
Supervisor Essentials
3
Essentials of Communication and Personal Effectiveness
Smart Manufacturing
1
Cybersecurity for Manufacturing Basics
Motor Controls
1
Control Devices