in on-the-job training and related instruction.
Combination Welder
Urban Institute
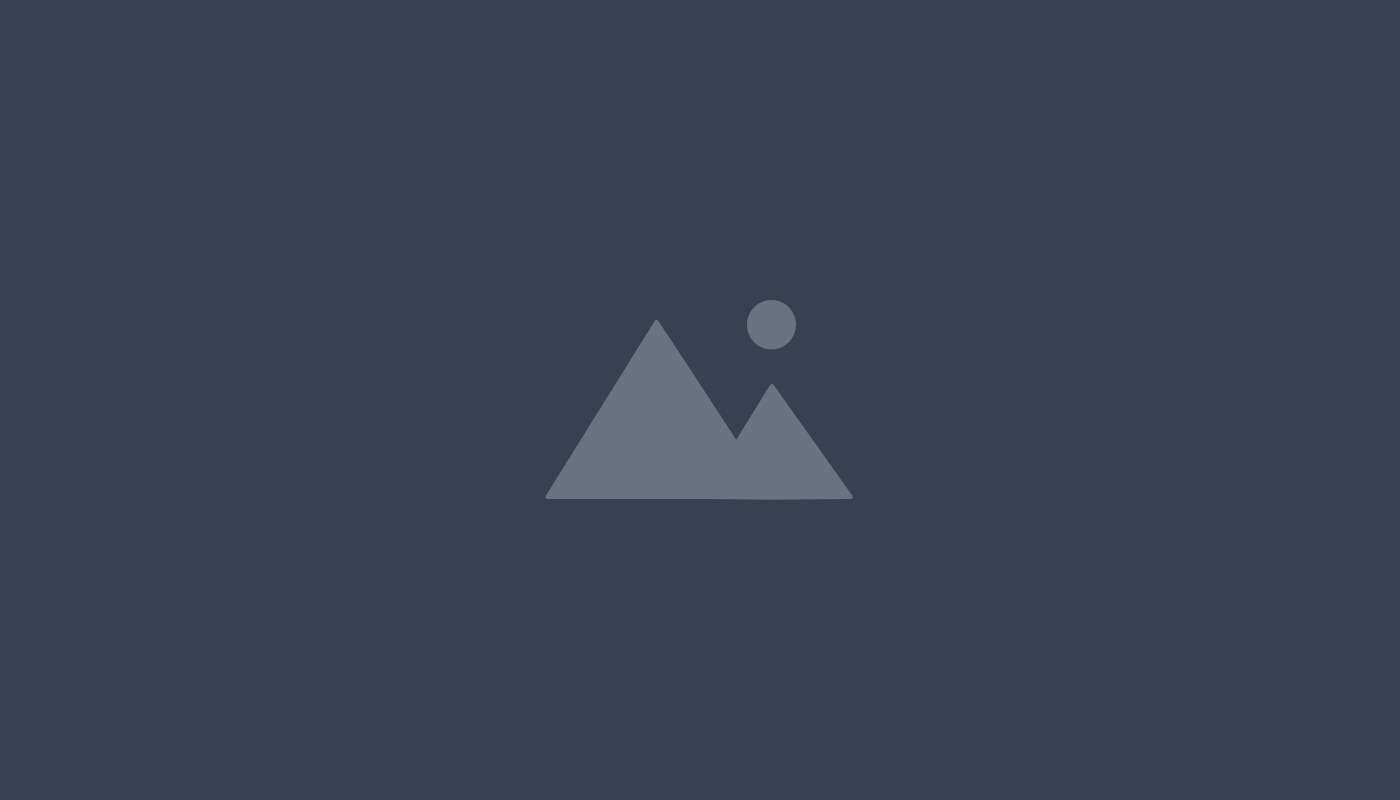
Work Process Content
On the Job Training
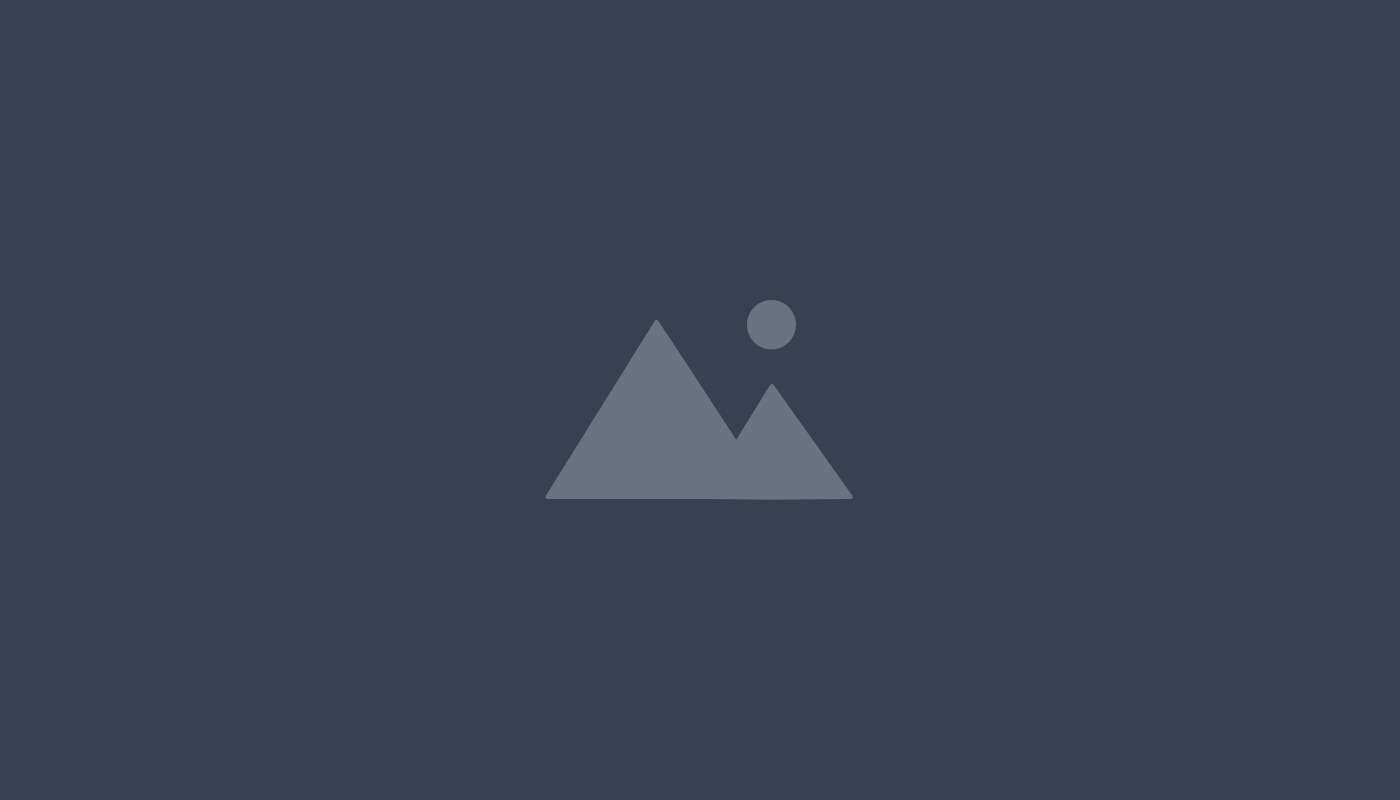
Demonstrates preparation to weld and executes welding procedures
16
- Analyzes engineering drawings, blueprints, specifications, sketches, work orders, and material safety data sheets to plan layout, assembly, and operations
- Prepares all material surfaces to be welded, ensuring there is no loose or thick scale, slag, rust, moisture, grease, or other foreign matter
- Determines required equipment and welding methods. applying proper knowledge of material grade, geometry, and welding techniques
- Accurately estimates load of weights and center of gravity
- Welds components in flat, vertical, horizontal, or overhead positions
- Grinds, cuts, buffs, or bends edges of workpieces to be joined per technical drawing
- Uses electric, gas, and other welding processes such as electron beam welding, and the skill to apply these processes in manufacturing, repairing, modifying, rebuilding, and constructing
- Assembles various types of metal and alloy parts, equipment, systems, and structures
- Conducts fabrication welding as necessary using a combination of welding processes, cutting, assembling and binding
- Monitors the welding process to prevent overheating, distortion. or shrinking during the process
- Welds metal parts and structures that may vary in size, shape, and thickness from very thin (e.g, .025 inches or less) to very thick (e.g„ armor plating), requiring multiple welding passes
- Welds dissimilar metals
- Assists other welders in installation, preparation, and fabrication while not actively welding
- Follows Weld Procedure Specification (WPS) as applicable
- Demonstrates understanding of PQR's (Procedure Qualification Record) and WPQR's (Welder Performance Qualification Record)
- Demonstrates ability to recognize welding symbols
Demonstrates proper use of tools and welding technique
9
- Selects and installs torches, torch tips, filler rods, and flux, according to welding chart specifications or types and thicknesses of metals
- Recognizes, sets up. and operates hand and power tools common to the welding trade. such as shielded metal arc and gas metal arc welding equipment
- Ignites torches or start power supplies and strike arcs by touching electrodes to metals being welded, completing electrical circuits
- Melts and applies solder along adjoining edges of workpieces to solder joints, using soldering irons, gas torches, or electric-ultrasonic equipment
- Secures pipes to structure with bracket. clamps, and hangers, using hand tools and power tools
- Uses straps, cables, and chains correctly
- Performs rigging, lifting, and moving of product using cranes, forklifts, metal carts, etc.
- Guides and directs flames or electrodes on or across workpieces to straighten, bend, melt. or build up metal
- Performs visual inspection of completed work (and reworks as needed)
Follows safety precautions in the workspace
6
- Develops and practices safe working habits and works in such a manner as to ensure personal safety and that of fellow workers
- Inspects equipment for defects and ensures proper working order
- Maintains work area and equipment in a safe, clean, and orderly condition
- Detects faulty operation of equipment or defective materials and notifies supervisors
- Properly determines rigging and hoisting capacity of cranes, lifts, and other tools based on weight of objects to be picked up
- Completes assigned tasks while wearing personal protective equipment (PPE) including but not limited to hard hat, safety glasses/goggles, ear plugs/muffs, masks/ respirators, safety vests, gloves, and leather work boots
Engages in professional and ethical communication
5
- Adheres to employer communication policies. Rules, regulations, and process instructions
- Accepts constructive feedback and criticism to improve performance
- Cooperates with and assists coworkers on projects when necessary
- Demonstrates effective one-on-one communication skills with supervisor and coworkers to discuss workplace challenges, personal limitations, and questions
- Completes assigned tasks on time
Possesses physical aptitude for welding
5
- Endures large amounts of standing, walking, bending, squatting, sitting, and lifting
- Utilizes arms and hands to signal, grab, hold. turn, push, and pull objects, materials, controls and tools
- Lifts, carries and moves heavy objects, possibly anywhere between 25 and 50 lbs, (with reasonable accommodations for workers with disabilities or injuries)
- Works at heights, climbs ladders and stairways, and works from platforms using the appropriate fall protection requirements
- Able to work in different weather conditions including heat conditions while wearing appropriate PPE
Applies math skills to conduct tasks with precision and accuracy
8
- Arranges, adds, subtracts, multiplies and divides whole numbers
- Solves practical problems using addition, subtraction, multiplication, and division of whole numbers
- Solves practical problems involving fractions
- Solves problems using operations with decimal fractions
- Solves more complex percentage problems in which two of the three parts are not directly given
- Solves practical applied problems involving tolerances and limits (customary and metric)
- Computes areas of more complex figures that consist of two or more common polygons
- Reads and interprets graph data
Related Instruction Content
Training Provider(s):
Fundamentals of Mathematics
30
Sample learning objectives: Manipulate integers, natural numbers, and negative numbers Accurately, and without the use of a calculator or Other electronic device, add, subtract, multiply, and divide whole numbers, decimals, and fractions Convert decimals to fractions and fractions to decimals Define, measure, and calculate area. volume. diameter, length, and circumference Convert metric lengths and volumes to English lengths and volumes and vice versa Convert units within the metric and English systems Follow the appropriate order of operations Solve single and double variable linear equations Calculate ratios and percentages Measure angles using a protractor, define the different types of angles in a triangle. and demonstrate the ability to determine the angles in triangles, quadrilaterals, and polygons Calculate the sine. cosine, and tangent of a triangle and demonstrate the ability to use the Pythagorean Theorem to determine the measurements of a right triangle (legs and hypotenuse)
Maintaining Occupational Health and Safety in Welding
20
Sample learning objectives: Discuss the hazards associated with welding and cutting operations and select the appropriate protective gear, including the protective shade number recommended by OSHA, ANSI, and AWS for a variety of welding and cutting operations Explain the potential sources Of harm to the work environment or work materials during the welding process as well as strategies for eliminating or mitigating those risks Define physical hazards in the workplace that can lead to death or injury and discuss safety practices to reduce this risk Discuss the hazards Of fumes and gasses produced during welding and the safety strategies employed to mitigate these risks Define the elements of a fire-safe area and demonstrate the ability to survey and prepare the work area for cutting and welding operations Demonstrate the ability to select and use appropriate fire control and extinguishing devices Demonstrate the ability to provide emergency first aid in the event of worker lacerations, burns, electric shock, eye injury, and accidental exposure to hazardous substances or fumes Explain the significance of material safety data sheets and develop storage. clean-up, and/or emergency response plans for items commonly used in the welding environment Complete "Fire Watch" training and be capable of assuming the responsibilities of a Fire Watch for hot work operations
Introduction to Welding and Cutting
40
Sample learning objectives: Define and provide examples of the appropriate uses for welding, brazing, and soldering Differentiate between mechanical, chemical, and metallurgical joining, describing the advantages, disadvantages, and indicated uses of each Differentiate between stick welding (also known as Shielded Metal Arc Welding, or SMAW), Manual Metal Arc Welding (MMAW), and flux-shielded arc welding; Gas Metal Arc Welding (GMAW) or Metal Inert Gas (MIG) welding; Active and Inert Gas welding is compiled in GMAW; Flux Cored Arc Welding (FCAW); and Gas Tungsten Arc (GTAW) Welding; describe the appropriate uses, advantages, and disadvantages of each Define and identify different types of electrodes used in welding as well as various types of metals used in construction, manufacturing, and metal work Describe the metallurgy of common alloys and correctly identify types of metals included in sample materials Define flux, slag, spatter, weld bead, and other key welding terms Identify different types of welds, such as groove welds, fillet welds, plug welds, and slot welds Differentiate between butt joints, cross joints, T-joints, corner joints, strapped joints, lap joints, and edge joints Discuss the importance of cleaning materials before cutting and welding, and demonstrate the ability to perform the appropriate cleaning processes Explain the characteristics of a properly performed welding operation and identify examples of quality welding versus defective welding (i.e„ pits, undercut, overlap, insufficient reinforcement, surface crack, arc strike, bead meandering [consistency], blow holes [porosity], impurities, slag inclusion, incomplete penetration, incomplete fusion, internal cracking, etc.) Correctly read engineering diagrams and construction or manufacturing blueprints to identify instances when welding is required and what type of welding is required Describe the purpose of a welding code, identify sources of information about relevant welding codes, and explain how to comply with various welding codes relevant to the work performed Describe the various techniques, tools, and processes used to inspect weld quality
Shielded Metal Arc Welding
40
Sample learning objectives: Demonstrate the appropriate use of arc welding shields and other safety equipment Inspect welding equipment and accessories and set-up equipment and materials needed to perform welding Explain the principles of metal arc welding, including the use of consumable electrodes, AC or DC power, and flux materials to combine metals Describe the process by which the flux coating of the welding electrode forms shielding gas and slag to protect the weld area Select the appropriate power source based on the materials to be combined and the type of weld desired, and adjust the power source to desired polarity and amperage setting Select the appropriate electrode based on the materials being joined and demonstrate the ability to change electrodes during the welding process Describe the main types of welding joints, the applications for each, and the criteria used to evaluate the quality and durability of such joints Demonstrate the ability to perform welding of fillet and groove welds on carbon steel Identify the types of metals that can be joined by shielded metal arc welding Demonstrate the ability to select the appropriate voltage, and strike an arc sufficient to combine various types of metals Demonstrate the ability to produce clean, effective welds across a range of joints and under various environmental conditions Critique a variety of welds to determine their quality and sufficiency; troubleshoot technique to improve weld quality, strength, appearance, and durability
Gas Tungsten Arc Welding
40
Sample learning objectives: Describe the types of metals and processes for which GTAW provides the best welding option Select the appropriate power source, tungsten electrode, sacrificial or filler rod (consumable),and shielding gas Select the appropriate filler material, if needed, based on the job specifications Inspect equipment for safety, assemble it properly, and start an arc Demonstrate proper use of safety equipment and proper preparation of the workspace Prepare materials for welding Perform flat, horizontal, and vertical fillet welds and flat groove welds in carbon steel, stainless steel, and aluminum Identify tungsten inclusion defects in sample welds and describe how to eliminate them from welds
Gas Metal Arc Welding
40
Sample learning objectives: Demonstrate proper use of safety equipment and proper set-up of workspace Explain the use of different types of feed (filler) wire and shielding gasses (inert and noninert gasses such as carbon dioxide) in GMAW and the advantages and disadvantages of each Assemble power source, wire feed unit, gun assembly, ground unit and gas source; set up and adjust machine to correct polarity, wire speed, and voltage based on type and position of joint desired Demonstrate safe use and storage of gas bottles, cylinder valves, and protective valve covers Make fillet welds in all positions on carbon steel material Make groove welds in all positions on carbon steel material Perform vertical and overhead welds Explain the importance of maintaining a consistent CTWB (Contact to Work Distance), weld speed, and voltage to produce an optimal weld Explain the importance of maintaining a consistent arc gap, weld speed, angles, and voltage to produce an optimal weld Compare and contrast between the use and techniques of short circuit transfer, globular transfer, and spray transfer Set up equipment, select wire size, select contact tip, and install new roll of wire Describe how variations in voltage and wire speed can change the type of joint produced Demonstrate weld puddle pushing, pulling and side-to-side motions to create appropriate weld type and dimensions Demonstrate the ability to use welding charts to determine the minimum voltage and wire speed needed for metal depth of materials being joined Demonstrate proper techniques for preparing metal for joining
Thermal Cutting Processes
10
Sample learning objectives: Differentiate between flame, plasma, oxyfuel, and laser cutting processes Demonstrate the ability to use oxyfuel cutting to cut through materials Explain how changes in gas purity will impact cutting speed and gas consumption List the five most common fuel gasses used for high-energy cutting and discuss the advantages and disadvantages of each Demonstrate the ability to use grinders to complete cutting and prepare edges and grooves for welding Demonstrate the process of gouging, joint edge preparation, and removal of defective weld metal Set up a plasma arc cutting circuit, and select the appropriate cutting gas based on the type of metal being cut Demonstrate appropriate use of measuring devices to cut metal to appropriate specifications and dimensions