in on-the-job training and related instruction.
STATIONARY ENGINEER
STATIONARY ENGINEERS TRAINING TRUST
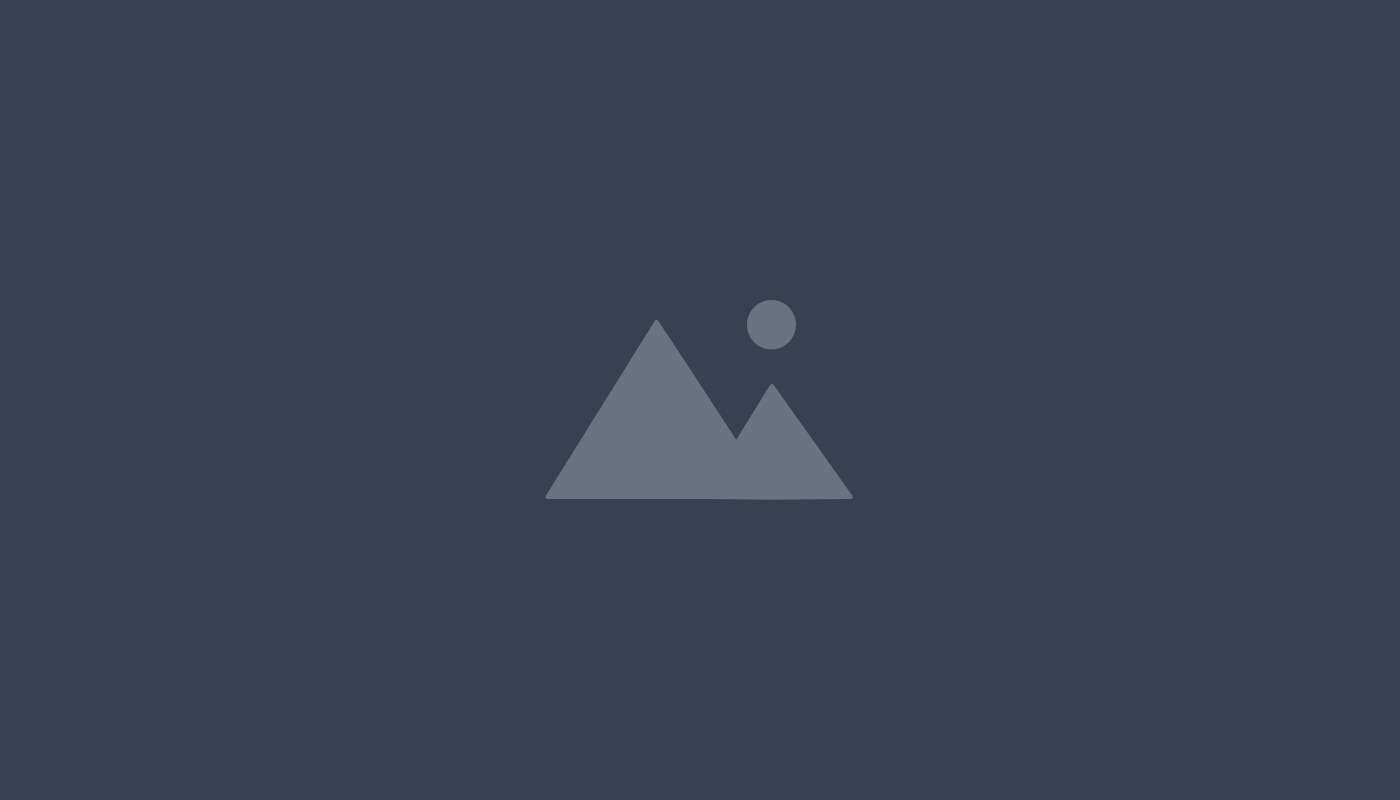
Work Process Content
On the Job Training
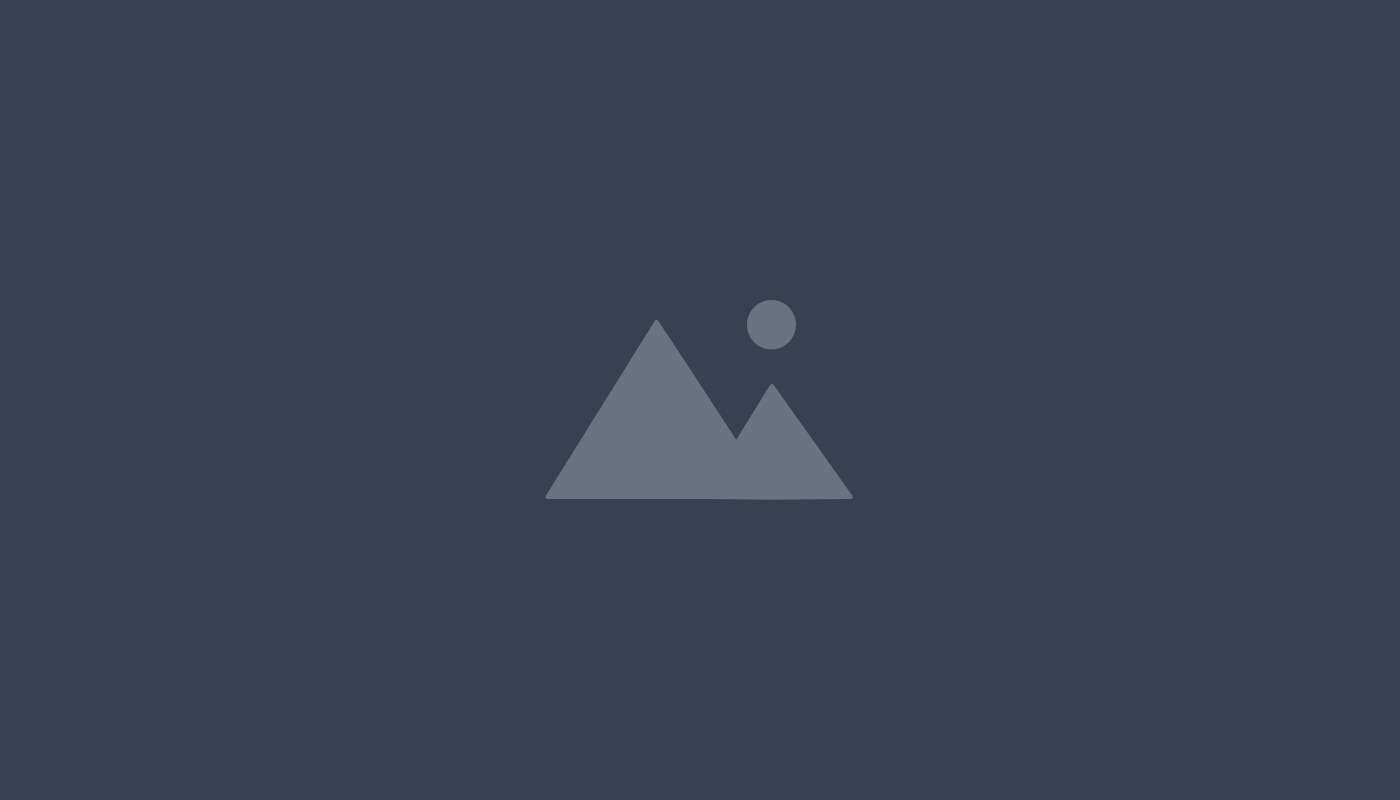
Plant Operations
0
600
a. Air Compressors b. Air Conditioners c. Air Dryers d. Boilers e. Chillers (1) Absorption (2) Reciprocating (3) Centrifugal f. Controls (1) Direct Digital (2) Electric (3) Electronic (4) Pneumatic g. Cooling Towers h. Fan Units i. Fire Alarm Systems j. Heat Exchangers (1) Air to Air (2) Air to Water (3) Water to Air (4) Water to Water k. Heat Pumps l. Humidifiers m. Lighting n. Motors and Motor Starters o. Production Equipment p. Pumps q. Refrigeration Equipment r. Resource Recovery and CO-Generation Equipment AC/DC Power Generation s. Steam Turbines and Engines t. Special Machinery
Monitoring Plant Operations
0
800
a. Air Compressor (1) Check oil pressure (2) Check oil level (3) Check pressure controls for proper operation (4) Drain moisture from receiver (5) Check cooling water temperature (6) Investigate any unusual operation or noise b. Air Conditioners (1) Check air and/or water flow (2) Check for proper temperature control (3) Check for proper operation of electrical controls (4) Investigate any unusual operation or noise c. Air Dryers (1) Check oil pressure (2) Check oil level (3) Check air differential pressures (4) Check pressure controls for proper operation (5) Drain moisture traps (6) Check air discharge temperatures (7) Investigate any unusual operation or noise d. Boilers (1) Check water level (2) Drain gauge glass (3) Check low water controls (4) Check high water controls (5) Blowdown water column (6) Check surface blowdown (7) Perform a bottom blowdown (8) Check flame failure controls (9 Perform a water analysis and treat accordingly (10) Check fuel oil temperature and pressure (11) Check atomizing air/steam pressure (12) Check fuel oil tank quantity and moisture (13) Check steam/water temperature/pressure (14) Check the feedwater temperature and pressure (15) Check quantity of make-up water (16) Check flue gas temperature and opacity (17) Clean and change burners (18) Check burner operation (19) Clean oil and water strainers (20) Investigate any unusual operation or noise e. Chillers (1) Check the compressor oil level, temperature and pressure (2) Check the suction and discharge temperature/pressure (3) Check the inlet vane ore slide vane position (4) Check the motor amperage and voltage (5) Check the steam pressure (6) Check the cooler refrigerant temperature and pressure (7) Check the brine concentrations (8) Check the cooler water inlet and outlet temperature and pressures (9) Check the condenser refrigerant temperature and pressure (10) Check the condenser water inlet and outlet temperature and pressures (11) Investigate any unusual operation or noise f. Controls (1) Direct Digital Monitor computer-controlled equipment, temperatures, pressures, volumes, etc. (2) Electric Monitor electric-controlled equipment, temperatures, pressures, volumes, etc. (3) Electronic Monitor electronic-controlled equipment, temperatures, pressures, volumes, etc. (4) Pneumatic Monitor pneumatic-controlled equipment, temperatures, pressures, volumes, etc. g. Cooling Towers (1) Check for proper fan, pump, and damper operation (2) Check sump water level (3) Perform a water analysis and treat accordingly (4) Investigate any unusual operation or noise h. Fan Units (1) Check for vibration (2) Visual check of belts and/or couplings (3) Check motor and fan bearing temperatures (4) Check inlet/outlet van/damper operation (5) Check pressure and/or temperature differentials across heating coils, cooling coils, humidifiers, filter banks, etc) (6) Investigate any unusual operation or noise i. Fire Alarm Systems (1) Disable/enable zones as needed (2) Perform emergency procedures as directed by the Fire Department. (3) Check trouble zones. (4) Investigate any unusual operation. j. Heat Exchangers (1) Air to Air Check pressure and/or temperature differentials of all air stream and filter banks. (2) Air to Water Check pressure and/or temperature differentials of all air and water streams and filter banks. (3) Water to Air Check pressure and/or temperature differentials of all air and water streams and filter banks. (4) Water to Water Check pressure and/or temperature differentials of all water streams and filter banks. k. Heat Pumps (1) Check air and/or water flow (2) Check for proper temperature control (3) Check for proper operation of electrical controls (4) Investigate any unusual operation or noise l. Humidifiers (1) Check pans for proper level and purging and/or drainage (2) Check for proper nozzle operation (3) Check for proper lamp operation (4) Investigate any unusual operation or noise m. Lighting (1) Check for burned out lamps and/or ballast (2) Check for proper lighting levels n. Motors and Motor Starters (1) Check for vibration (2) Visual check of belts and/or couplings (3) Check motor bearing temperatures (4) Check amperage and voltage readings (5) Investigate any unusual operation or noise o. Production Equipment (1) Check bearings, belts, sprockets, sheaves, chains, and conveyers for proper tension, lubrication and operation (2) Monitor temperatures, pressures, and flow rates (3) Check for proper operation of electrical controls (4) Investigate any unusual operation or noise p. Pumps (1) Check for vibration (2) Visual check of belts and/or couplings (3) Check motor and pump bearing temperatures (4) Check inlet/outlet valve operation and position (5) Check pressure and/or temperature differentials across pump (6) Investigate any unusual operation or noise q. Refrigeration Equipment (1) Check air and/or water flow (2) Check for proper temperature control (3) Check for proper operation of electrical controls (4) Investigate any unusual operation or noise r. Resource recovery and co-generation equipment AC/DC Power Generation (1) Check for proper temperatures and pressures (2) Check amperage and voltage readings (3) Check for proper fuel levels and filtering (4) Check for proper cooling and air flows (5) Check for proper synchronization and phases (6) Check for proper operation of electrical controls (7) Investigate any unusual operation or noise s. Steam Turbines and Engines (1) Check for proper steam pressures and temperatures (2) Check for proper pressures and temperatures for lubrication (3) Check for proper speed and control (4) Investigate any unusual operation or noise t. Special Machinery (1) Check for proper temperatures and pressures (2) Check for proper lubrication (3) Check amperage and voltage readings (4) Check for proper operation of electrical controls (5) Check bearing, belts, sprockets, sheaves, chains, and conveyors for proper tension, lubrication and operation (6) Investigate any unusual operation or noise
Diagnostic Analysis
0
2K
a. Water Analysis (1) Hot water boilers (2) Steam boilers (3) Closed-loop heating systems (4) Closed-loop cooling systems (5) Condenser water (6) Chilled water b. Boiler/furnace stack gases analysis (1) Temperature (2) CO, CO2, O2, NOX c. Ambient Air Conditions (1) Temperature (2) Carbon Dioxide (3) Oxygen (4) Humidity (5) Contaminates d. Process wastewater (1) PH (2) Contaminates e. Testing the "Sequence of Operation" for the following equipment: (1) Air Compressors (2) Air Conditioners (3) Air Dryers (4) Boilers (5) Chillers (a) Absorption (b) Reciprocating (c) Centrifugal (6) Controls (a) Direct digital controls (b) Electric controls (c) Electronic controls (d) Pneumatic controls (7) Cooling towers (8) Fan units (9) Fire alarm systems (10) Heat exchangers (a) Air to air (b) Air to water (c) Water to air (d) Water to water (11) Heat pumps (12) Humidifiers (13) Motor starters (14) Production equipment (15) Pumps (16) Refrigeration equipment (17) Resource recovery and CO-generation equipment (18) Steam Turbines and Engines (19) Variable Speed Drive controls (20) Special machines within the craft jurisdiction by contract f. Electrical (1) Testing for continuity, grounds, short circuits, etc., on the electrical circuits of: (a) Air Compressors (b) Air Conditioners (c) Air Dryers (d) Boilers (e) Chillers (f) Controls 1) Transformers 2) Solenoid operations 3) Timers and timing devices 4) Control devices 5) Connecting three-phase and singlephase motors 6) Reversing motor direction 7) Reduced voltage starting 8) Overload protection/overload heater selection. 9) Inherent motor protection 10) Braking circuits 11) Photo-electric/proximity sensors 12) Programmable controllers 13) Direct digital Controllers 14) Contactors, starters and relays 15) Motor control centers 16) Variable Speed Drives (g) Cooling towers (h) Fan units (i) Fire alarm systems (j) Heat Exchangers 1) Air to air 2) Air to water 3) Water to air 4) Water to water (k) Heat pump (l) Humidifiers (m) Lighting (n) Motors and motor starters (o) Production equipment (p) Pumps (q) Resource recovery and co-generation equipment (r) Steam Turbines and Engines (s) Special machines within the craft jurisdiction by contract (2) Circuit analysis (a) Ohms law (b) Rules of line diagrams (c) Wire codes and amperage calculations (d) Numerical cross referencing (e) Wiring diagrams (f) Torque and horsepower (g) AC/DC motor speed control (h) Solid state starting/speed control (i) Photo-electric control (j) Inspection and analysis of mechanical equipment 1) Inspect bearings, belts, sprockets, sheaves, chains, etc. 2) Vibration analysis g. Commissioning (1) Retro or Re-Commissioning practices (2) Energy use analysis (3) Functional Performance Testing
Preventive Maintenance
0
1.2K
Perform the daily, weekly, monthly, quarterly, semiannual, and annual mechanical and electrical maintenance as needed on the following equipment: a. Air Compressors b. Air Conditioners c. Air Dryers d. Bearings adjustment e. Boilers f. Chillers g. Controls (1) Direct digital controls (2) Electric controls (3) Electronic controls (4) Pneumatic controls h. Cooling towers i. Electrical Distribution j. Fan units k. Fire alarm systems l. Heat exchangers (1) Air to air (2) Air to water (3) Water to air (4) Water to water m. Heat pump n. Humidifiers o. Lighting p. Motor control centers q. Motors and motor starters r. Production equipment s. Pumps t. Refrigeration equipment u. Resource recovery and co-generation equipment v. Steam Turbines and Engines w. Transformers x. Any other mechanical/electrical device found in the field
Mechanical Repairs
0
700
Perform the needed mechanical repairs on the following equipment a. Air Compressors b. Air Conditioners c. Air Dryers d. Boilers e. Chillers f. Controls g. Direct digital controls (1) Electric controls (2) Electronic controls (3) Pneumatic controls h. Cooling towers i. Fan units j. Fire alarm systems k. Heat exchangers (1) Air to air (2) Air to water (3) Water to air (4) Water to water l. Heat pumps m. Humidifiers n. Lighting o. Motors and motor starters p. Production equipment q. Pumps r. Refrigeration equipment s. Resource recovery and co-generation equipment t. Steam turbines and engines u. Any other mechanical device found in the field
Plant safety
0
500
a. Lockout and tagout of energy sources b. Industrial/CPR first aid c.Hazardous material d. Chemical identification safety e. Emergency procedures f. OSHA/WISHA/EPA Standards and Regulations g. General electrical/mechanical safety h. Industrial Accidents/Reporting i. Plant general up-keep
Fabrication
0
800
a. Welding and use of oxy-acetylene equipment b. Metal cutting power machine c. Shop and bench work d. Job planning e. Line voltage/low voltage circuitry h. Circuit Analysis (1) Ohms law (2) Rules of line diagrams (3) Wire codes and amperage calculations (4) Numerical cross referencing (5) Wring Diagrams (6) Torque and horsepower (7) AC/DC motor speed control (8) Solid state starting/speed control (9) Photo-electric control (10) Panel box connections (11) Conduit bending (12) Control devices (13) Connecting three-phase and single-phase motors (14) Reversing motor direction (15) Reduced voltage starting (16) Overload protection/overload heater selection (17) Inherent motor protection (18) Braking circuits (19) Photo-electric/proximity sensors (20) Programmable controllers (21) Direct digital controllers
Electrical Repairs
0
1.4K
Perform the needed electrical repairs on the following equipment: a. AC/DC power generation equipment b. Transformers and solenoids c. Contactors, relays and starters d. Line voltage and control voltage wiring e. Motor overload protection f. Timers and timing devices g. Motor control centers h. Control devices and sensors i. Programmable controllers j. Direct digital controllers k. Any other line voltage and/or low voltage device encountered in the field l. Variable Speed Drives In addition, the apprentice will be taught the use, care and safe handling of all tools, materials and apparatus commonly used in connection with the Stationary Operating Engineers trade.
Related Instruction Content
Training Provider(s):