using a minimum and maximum range of hours for each major job
function and the successful demonstration of identified competencies.
Additive 3D Printing Technician
Robert C. Byrd Institute and Apprenticeship Works National Advanced Manufacturing Partnership (NAMAP)
Work Process Content
On the Job Training
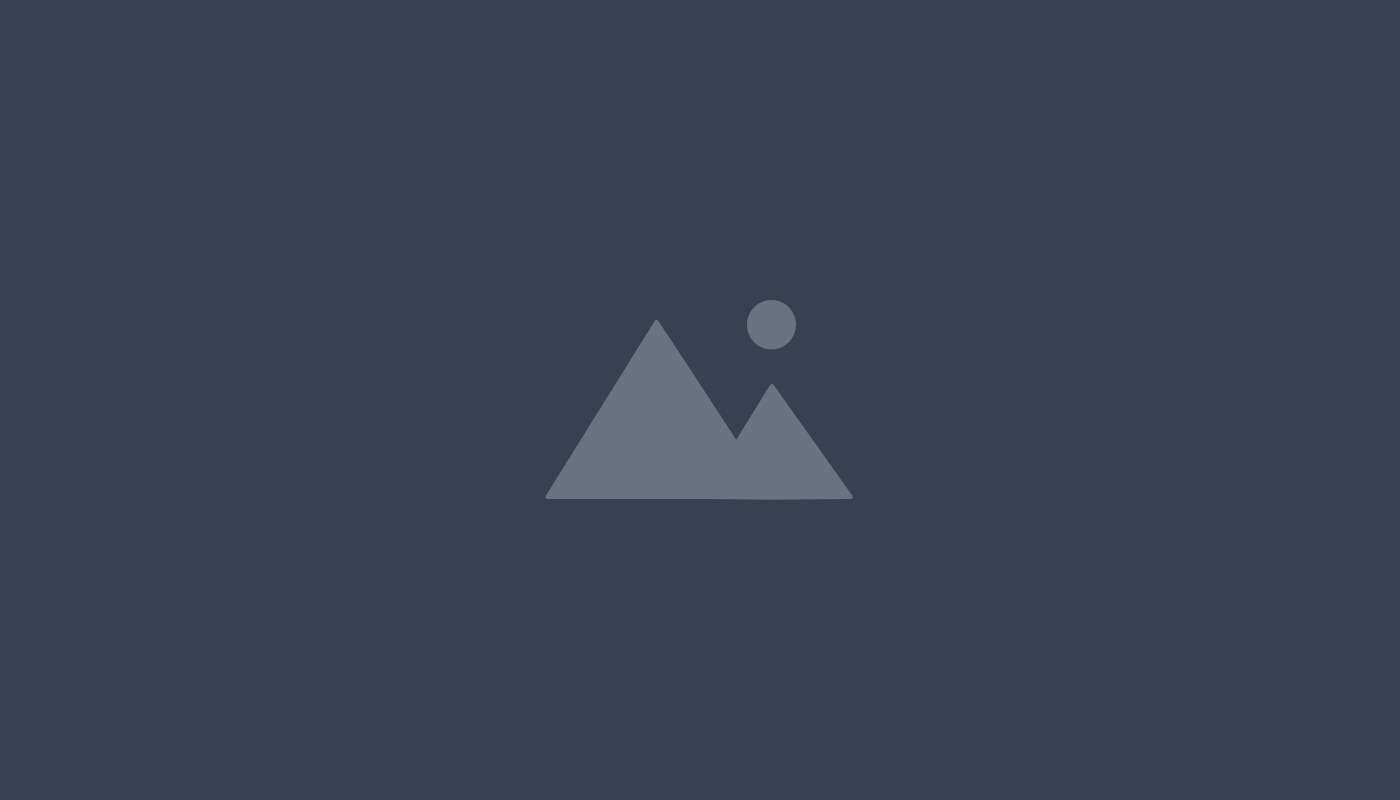
Industrial Safety
14
30
- Demonstrate the ability to adhere to personal grooming requirements in the facility.
- Demonstrate the ability to use personal protective equipment including eye, ear, hand, respiratory, body and foot protection, by ensuring that a correct fit and optimum protection is provided to the wearer for the specific task, in accordance with applicable safety legislation, government regulations, manufacturers' specifications and company standards/procedures.
- Demonstrate the ability to follow fire safety procedures including: determining the potential for fire posed by the work being performed; locating and assessing the severity of the fire; selecting and operating fire extinguishing equipment; suppressing minor fires; activating alarms; following fire evacuation plans; and, reporting incidents; in accordance with applicable Acts, Regulations, Legislation, and Codes, manufacturers’ specifications, and company standards or procedures.
- Demonstrate the ability to work around energy sources by observing limits and procedures for approaching energy sources to ensure personal safety and protection of equipment in accordance with standards.
- Demonstrate adherence to performing lock-out/tag-out procedures and energy isolation for assigned machinery in accordance with facility regulations.
- Demonstrate the ability to handle and store hazardous materials as assigned, while adhering to safe practices in accordance with Occupational Safety and Health Administration (OSHA) and Environmental Protection Agency (EPA) requirements and guidelines, including completing the required documentation.
- Demonstrate the ability to identify all pinch points on primary and supportive machine tools and the proper placements of guards.
- Demonstrate both emergency and standard shut down of all required equipment.
- Demonstrate the use and location of eye wash sinks within the workplace.
- Demonstrate the use and location of first aid kits in the workplace.
- Demonstrate the ability to practice good housekeeping in the workplace, by ensuring that the workplace is clean, organized, and free of obstructions, spills, or fire hazard and that materials and equipment are cleaned and sorted in designated areas after use.
- Demonstrate the safe use of hand and power tools.
- Demonstrate how to identify and recognize hazardous situations and apply proper procedures (includes following guidelines to prevent spread of blood borne pathogens and spill control).
- Demonstrate how to locate a material Safety Data Sheet (SDS) and describe how you interpret the information.
Workplace Skills
34
30
- Demonstrate the ability to listen and comprehend instructions.
- Demonstrate the ability to read and comprehend English.
- Interpret specific instructions from a supervisor.
- Demonstrate the ability to write clear letters, instructions and reports.
- Use e-mail and other electronic means for communication.
- Communicate non-documented processes to fellow employees or supervisors.
- Read and interpret non-English information, such as material specifications.
- Demonstrate the ability to use a group approach to identify problems and develop solutions based on group consensus.
- Adhere to company policies related to timeliness, punctuality, and confidentiality.
- Demonstrate time management skills.
- Work effectively in teams within a workforce or group.
- Manage conflict effectively and with sensitivity to the needs and perceptions of others.
- Plan and conduct effective meetings.
- Demonstrate life-long learning geared toward personal growth.
- Demonstrate strong presentation skills for small and large groups.
- Exercise appropriate usages of computer systems.
- Demonstrate adherence to computer security policies.
- Demonstrate proficiency in keyboard skills.
- Use email and text messaging effectively with the correct grammar and spelling.
- Create and use spreadsheets for data analysis, graphic, record keeping and other uses.
- Use the internet effectively for researching and acquiring technical information.
- Create quality written documents using word processing software.
- Create and use database applications.
- Integrate documents containing word processing, spreadsheets and graphics.
- Analyze test data, compare information and draw rational conclusions.
- Demonstrate mastery in basic arithmetic, including proportions, percentages, etc.
- Show that data, calculations and results are reasonable.
- Use mental arithmetic and calculators as computation tools.
- Prepare and interpret graphs using a variety of scales and presentation techniques.
- Perform conversions for units from one system to another.
- Use accurately both U.S. Customary units and the International System of Units (ISU).
- Demonstrate the use of accuracy and precision.
- Utilize concepts of perimeter, area and volume of basic shapes.
- Apply concepts of angles and triangles.
Problem Solving
10
30
- Recall key job-related information (processes, references, terminology, acronyms).
- Show proficient observation skills during demonstrations of processes or equipment operation.
- Perform troubleshooting of equipment and instrumentation.
- Perform basic setup, diagnosis and repair of industrial machinery and equipment.
- Use vendor catalogs to acquire troubleshooting information and to identify materials and components for work tasks.
- Demonstrate flexibility, willingness to learn and ability to solve problems.
- Demonstrate the tracing of defects to the originating section of their root cause.
- Demonstrate the use of cause mapping when performing Root Cause Analysis.
- Demonstrate the ability to apply the 5 Why methodology to isolate problems for an equipment problem.
- Demonstrate the ability to apply effective observation and interview strategies to validate the problem and determine the most effective troubleshooting strategy.
Quality Assurance and Part Analysis
8
200
- Measure dimensions accurately using scales, micrometers and related tools.
- Measure hardness, impact strength and related properties of materials accurately.
- Demonstrate knowledge of order of magnitude of measurement and scales.
- Measure temperature, pressure, force, torque and related quantities accurately.
- Measure mass accurately using appropriate devices.
- Apply precision metrology devices and inspection tools.
- Read and interpret technical drawings.
- Interpret and apply tolerances on component dimensions and specifications.
Material Selection, Sourcing, Requisitioning
5
100
- Choose and apply a type of material to render parts.
- Compare the differing properties and characteristics of common materials used for additive manufacturing models.
- Perform formal historical sourcing analysis for upcoming events, tapping into internal/external data to identify trends, opportunities and threats.
- Execute structured formal bid processes, (Request for Information [RFI], Request for Quotation [RFQ], Request for Proposal [RFP]), consistently with appropriate suppliers, which include favorable terms and conditions to the enterprise.
- Evaluate supplier capabilities against a standard set of well-documented criteria and provides a comprehensive comparison on the relative capabilities of suppliers against the criteria.
Part Design (CAD)
28
2.2K
- Create and modify technical drawings using computer-aided design (CAD), including three-dimensional (3D) modeling.
- Demonstrate the proper use of computer-aided design (CAD) software.
- Apply the computer-aided (CAD) design three-dimensional (3D) coordinate system for three-dimensional objects.
- Demonstrate and apply basic software utilities for arranging, detailing and plotting views of an object.
- Align, rotate and mirror three-dimensional (3D) objects.
- Create and render a three-dimensional (3D) model.
- Perform analysis on the computer model and refine the design, as needed.
- Enter and save data for an object drawing.
- Create an assembly drawing with proper dimensioning and appropriate views.
- Apply basic solid modeling commands.
- Create multiple parts using components of a design tree.
- Choose and apply a type of material to use to render parts.
- Demonstrate basic design principles of visual and spatial form as applied to products.
- Capture physical three-dimensional (3D) objects, and reverse engineer accurate computer-aided design (CAD) models from three-dimensional (3D) scans.
- Describe the fundamentals of material selection for product and system design.
- Measure and calculate properties of parts.
- Apply orthographic projection principles to drawing’s layouts.
- Perform analyses on the sketch procedures and refine the sketch design.
- Perform advanced mating using multiple parts or sub-assemblies.
- Create and insert render parts into the sheet environment of a solid modeling drawing.
- Create basic building construction, architectural and object designs in three dimensions.
- Demonstrate a thorough knowledge of three-dimensional (3D) file formats as applicable.
- Demonstrate the ability to manipulate and modify a three- dimensional (3D) file.
- Explain and illustrate the advantages of using the different three-dimensional (3D) file formats.
- Describe the characteristics of the different three-dimensional (3D) file formats.
- Differentiate part orientation using x, y, z, coordinates in the build platform.
- Define and illustrate orthogonal orientation notation of a part.
- Demonstrate the right hand rule for positive rotations with reference to the build volume origin.
Cost Modeling: Pricing Parts Correctly
5
100
- Prepare detailed cost estimates of capital and annual operating costs, maintenance and repair, and replacement costs for a project or component of a project, such as equipment, materials, assembly, inspection, modification, quality assurance, etc.
- Calculate the return on investment, present worth and/or annual cost and benefit of a project having initial capital and annual operation, maintenance, repair, salvage value and replacement costs using appropriate interest, discount, and projected inflation rates.
- Identify and quantify the economic risks associated with a project or product, including how warranty costs are considered for a product.
- Compare design alternatives with varying cost profiles on a present worth or annual cost basis.
- Interact with managers and other professionals in providing project economic information and opinions of project costs in financial analysis and financing process.
Process Selection
5
100
- Identify standards of ASTM International (formerly the American Society for Testing and Materials) in relation to additive manufacturing.
- Define the basic terms used in additive manufacturing in oral and written communications.
- Explain and illustrate the various additive manufacturing processes.
- Compare and contrast the various additive manufacturing processes.
- Compare and contrast additive manufacturing processes to other manufacturing processes.
Machine Operation
8
200
- Demonstrate a knowledge of the safety precautions required to operate each additive manufacturing device.
- Demonstrate the proper method for wearing of safety goggles, face shields particle masks, ear protection devices and appropriate clothing used in additive manufacturing.
- Demonstrate the required response needed in the event of an accident in the workplace.
- Demonstrate the location and use of safety manuals located in the workplace.
- Demonstrate the location and operation of all power sources for additive manufacturing equipment in the workplace.
- Set-up a 3D printer (Three Dimensional Printer) and supporting equipment for a build, including uploading the file, placing support structures, selecting part orientation, and loading the build materials and platform.
- Start and stop an operation in accordance with standard operating procedures.
- Fabricate a part or an assembly using additive manufacturing equipment.
Machine Maintenance: Troubleshooting, Install, etc.
14
100
- Verify equipment is ready for operation in accordance with a safety checklist.
- Identify machine malfunctions through observations of control panels or other notifications.
- Use five senses to observe machine operations and vibration to determine if operations is correct.
- Recognize symptoms of equipment malfunction.
- Check for leaks, dirt and loose connections during equipment operations.
- Read and interpret pressure gauges, flow meters, fluid levels, temperature gauges, voltages and current.
- Use Human Machine Interface (HMI) equipment to monitor machine performance.
- Replace or install additive manufacturing equipment components to maintain proper working order.
- Select applicable diagnostic or configuration software so that controls, instruments, equipment, and systems can be calibrated, configured, and tested, in accordance with manufacturers’ specifications, and company standards/procedures.
- Identify required configuration licensing so that controls, instruments, equipment, and systems can be calibrated, configured, and tested, in accordance with manufacturers’ specifications, and company standards/procedures.
- Use software such as spreadsheets, databases, and word processors so that controls, instruments, equipment, and systems can be calibrated, configured, and tested, in accordance with manufacturers’ specifications, and company standards/procedures.
- Use interfaces such as handhelds, laptops, and modems so that controls, instruments, equipment, and systems can be calibrated, configured, and tested, in accordance with manufacturers’ specifications, and company standards/procedures.
- Update software and firmware so that controls, instruments, equipment, and systems can be calibrated, configured, and tested, in accordance with manufacturers’ specifications, and company standards/procedures.
- Back-up data and equipment configurations so that controls, instruments, equipment, and systems can be calibrated, configured, and tested, in accordance with manufacturers’ specifications, and company standards/procedures.
Post Processing, Finishing and Breakout
18
590
- Demonstrate a thorough knowledge of the proper use of basic hand tools (hammers, pliers, screw drivers, hand saws, wrenches, sanding blocks).
- Demonstrate a thorough knowledge of the proper use of standard machine tools (electric: drills, saws, grinders, sanders).
- Interpret the proper tool selection for a given task.
- Demonstrate a knowledge of investment casting and how additive manufacturing is used as a secondary process for investment casting.
- Demonstrate a knowledge of sand casting and how additive manufacturing is used as a secondary process for sand casting, including making the cope and drag using additive manufacturing.
- Demonstrate a knowledge of die casting and how additive manufacturing is used as a secondary process for die casting.
- Demonstrate a knowledge of silicone molding and how additive manufacturing is used as a secondary process for silicone molding, including making the master pattern using additive manufacturing and how to create silicone molds using the master pattern.
- Demonstrate a knowledge of composite molding and how additive manufacturing is used as a secondary process for composite molding.
- Demonstrate a knowledge of metal spraying and how additive manufacturing is used as a secondary process for metal spraying.
- Demonstrate a knowledge of metal stamping/forming and how additive manufacturing is used as a secondary process for metal stamping/forming.
- Demonstrate a knowledge of hydroforming and how additive manufacturing is used as a secondary process for hydroforming, including making molds using additive manufacturing.
- Demonstrate a knowledge of thermoforming and how additive manufacturing is used as a secondary process for thermoforming.
- Demonstrate a knowledge of EDM (electrical discharge machining) and how additive manufacturing is used as a secondary process for electrical discharge machining (EDM).
- Demonstrate a knowledge of important additive manufacturing post-processing procedure, such as abrasive finishing, heat treatment, support structure removal, and painting, and how to perform them.
- Demonstrate a knowledge of the coatings used in additive manufacturing post-processing and how to apply them.
- Demonstrate a knowledge of additive manufacturing assembly procedures, such as adhesive bonding and welding.
- Demonstrate a knowledge of the various metal cutting procedures, such as turning and milling.
- Demonstrate a knowledge of manual machining, including using an engine lathe.
Electrical Systems
12
100
- Adhere to National Electric Code (NEC) safety procedures for tightening, disconnecting or connecting electrical conductors and components.
- Adhere to hazard avoidance in contact with live electrical systems.
- Adhere to guidelines on the safe approach distances while working on electrical systems.
- Use a multi-meter to measure voltage and current to an electrical circuit.
- Use a multi-meter to measure resistance in an electrical circuit.
- Use a multi-meter to perform a continuity check in an electrical circuit
- Calculate power in an electrical circuit given current and voltage.
- Size fuses and circuit breakers in accordance with NEC requirements for a given power draw in an electrical circuit with consideration to ampacity of wiring in that circuit.
- Install fuses and circuit breakers into circuits.
- Inspect circuit breakers to determine if they have been tripped.
- Reset a circuit breaker.
- Recognize all protective tags and lockout devices that are used to isolate equipment and components from hazardous energy sources.
Computer-Numerical Control (CNC) Systems
10
200
- Identify and select the Computer-Numerically Controlled (CNC) machines using information from the job specifications to ensure that the machining process selected is the correct one to make the parts or components.
- Input and process program data to the machine memory using information from machine-tool manual and programming data so that the data is input correctly to machine the part in accordance with the job process sheet.
- Determine the tool path and calculate the proper coordinates to establish cutter start-point, cutter finish-point, and geometry of path in accordance with the set-up sheet and job specifications.
- Identify, select, and set up Computer-Numerically Controlled (CNC) cutting tools and tooling (tool holders, end and face mills, carbide insert tools, center-drill, drill, taps, reamers, counter bores, and boring head) to pre-determined reference points outlined from the prepared sequence sheets and tool lists, to ensure that the tools and tooling selected are the correct ones to machine the workpiece efficiently and safely.
- Identify, select, and set machine parameters (spindle feeds, table feeds, and power settings) using speed and feed charts and according to the type, size, grade, and hardness of the material to be cut so that the workpiece is machined efficiently and safely without damage to the tooling, machine, or workpiece and ensure personal safety in accordance with job specifications.
- Position and align workpiece in Computer-Numerically Controlled (CNC) machine to specified datums and required alignments, using chucks, face plates, collets, vises, clamps, stops, and fixtures to locate and position the workpiece, avoid collisions, and, ensure maximum stability during machining in accordance with job specifications.
- Input and verify the part program at Numerically Controlled/Computer Numerically Controlled (NC/CNC) machine controls by: performing a dry run; taking a test cut; interrupting machining; measuring and checking dimensions; adjusting machine feeds, speeds, and offsets; editing the program; taking a final cut; and, performing an inspection prior to the production run; to ensure that the dimensions, shape, and tolerances of the machined part conforms to job specifications.
- Store and record a verified program on storage media for future use so that programs can be retrieved and available for repeat machining jobs in accordance with job specifications.
- Monitor the Numerically Controlled/Computer Numerically Controlled (NC/CNC) machining process by interrupting machining, measuring or checking dimensions, and adjusting machine feeds, speeds, and offsets, so that the dimensions, shape, and tolerances of the machined work piece are maintained during machining in conformance job specifications.
- Perform final inspection using precision measuring instruments and checking devices including inside and outside micrometers, vernier height gauges or indicators, gauge blocks, and pin gauges to ensure that the tolerances and dimensions of the sawed work piece to conform to the engineering drawings and job specifications.
Related Instruction Content
Training Provider(s):
Industrial Safety
10
Occupational Safety Health Administration (OSHA) Training Personal protection equipment [PPE], hazard communication, accident/near miss reporting, hazardous materials, emergency plan, fire prevention, blood borne pathogens, lock-out tag- out, ergonomics, walking and working surfaces, machine guarding, Additive Manufacturing Hazards: Mechanical; Electrical; Thermal; Airborne Particles)
Advanced Mathematics
6
Applied Mathematics Review (Units of measurement, algebra, geometry, trigonometry, statistics)
History of 3D Printing
4
History (Uses of additive manufacturing parts, industries using additive manufacturing, etc.)
3D Printing Theory
16
Introduction to Additive Manufacturing (Terminology, sources of input, additive manufacturing materials, additive manufacturing processes, current technology and equipment supporting additive manufacturing, secondary processes)
International Organization for Standardization (ISO)/American National Standards Institute (ANSI) Standards
4
Additive Manufacturing Quality Systems (Key quality factors, digital file configuration and control, vendor and raw material management, device inspection/control, machine calibration, preventative maintenance, sample testing, production/process flow documentation, final part inspection)
Practical Metrology
24
Dimensional Measurement (Blueprint reading and interpretation, part tolerance, measurement equipment and gauges, scales, hardness testing, optical comparators, vision systems, coordinate measuring machines)
Additive Manufacturing Materials
12
Additive Manufacturing Materials (Materials: polymers; metals; ceramics; hybrid, microstructure, properties, qualification, vendor considerations, material life cycle.
Applied 3D Printing
80
3D Printing Equipment Operation (Equipment overview and setup, AM file input, auxiliary equipment set-up and operations, troubleshooting, part verification)
Additive Manufacturing Materials
12
Additive Manufacturing Materials (Materials: polymers; metals; ceramics; hybrid, microstructure, properties, qualification, vendor considerations, material life cycle)
Additive Manufacturing Secondary and Post Processing
24
Secondary Processing (Investment casting, sand casting, die casting, silicone molding, lay-up tooling, metal spraying, metal forming, stamping, metal spraying, jigs and fixtures, thermoforming, paper pulp tooling, electrical discharge machining [EDM] tools) Post Processing (Materials, methods, automating processes, processes for parts and components, processes for final products/use)
Workplace Communications
4
Communications (Active listening, reading and comprehension, writing clearly, communicating through multiple means of communication)
Geometric Dimensioning and Tolerancing (GD&T)
12
Applied Geometric Dimensioning and Tolerancing (GD&T) for Design for Additive Manufacturing (DFAM) (terminology and key elements, goals and objectives, roadmaps, integrating GD&T for rapid prototyping)
Intermediate Computer-Aided Design (CAD)
40
Applied computer-aided design (CAD) Design (Software navigation, drawing creation and modification, arranging/detailing and plotting views of an object, capture three-dimensional cans of objects and reverse engineering in software environment, save and render parts)
Additive Part Design
80
Design for Additive Manufacturing (DFAM) (Design strengths, design weaknesses, design considerations, computational modeling, design for direct digital manufacturing, legacy parts optimization, customer requirement specifications, design verification, risk management)
Basic Electrical Systems
16
Core Electrical Systems (Safety, interpreting schematics, electrical theory, power supply, circuits, basic wiring)
Basic Computer Numerical Control Systems
24
Core Computer Numerical Control (CNC) Systems (Safety, cartesian coordinate system, controls, part programs)
Problem Solving
16
Problem Solving (Root cause analysis, the 5 why’s, creative thinking, preventative and predicative maintenance)
Design Economics and Costs
16
Manufacturing Economics (Time value of money, accounting basics, capital budgeting, risk identification, cost-benefit analysis, profit/loss)