Hybrid programs blend both competency- and time-based strategies,
using a minimum and maximum range of hours for each major job
function and the successful demonstration of identified competencies.
using a minimum and maximum range of hours for each major job
function and the successful demonstration of identified competencies.
Service Technician
Anonymous
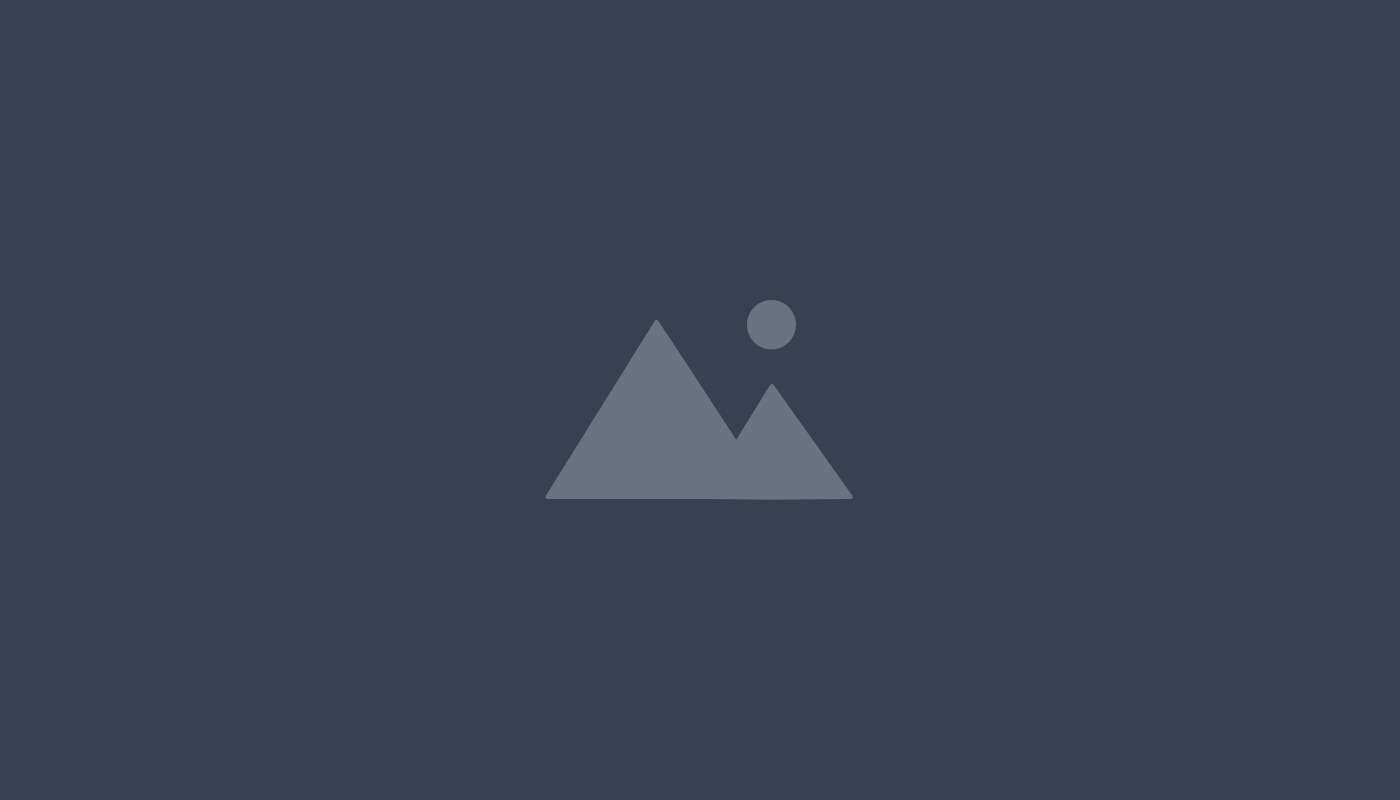
North Carolina (SAA)
Documents
View Redacted Document
Personal and employer info redacted
Individual state requirements may vary. Please contact your local apprenticeship office to ensure this version is suitable to your state’s requirements.
Work Process Content
On the Job Training
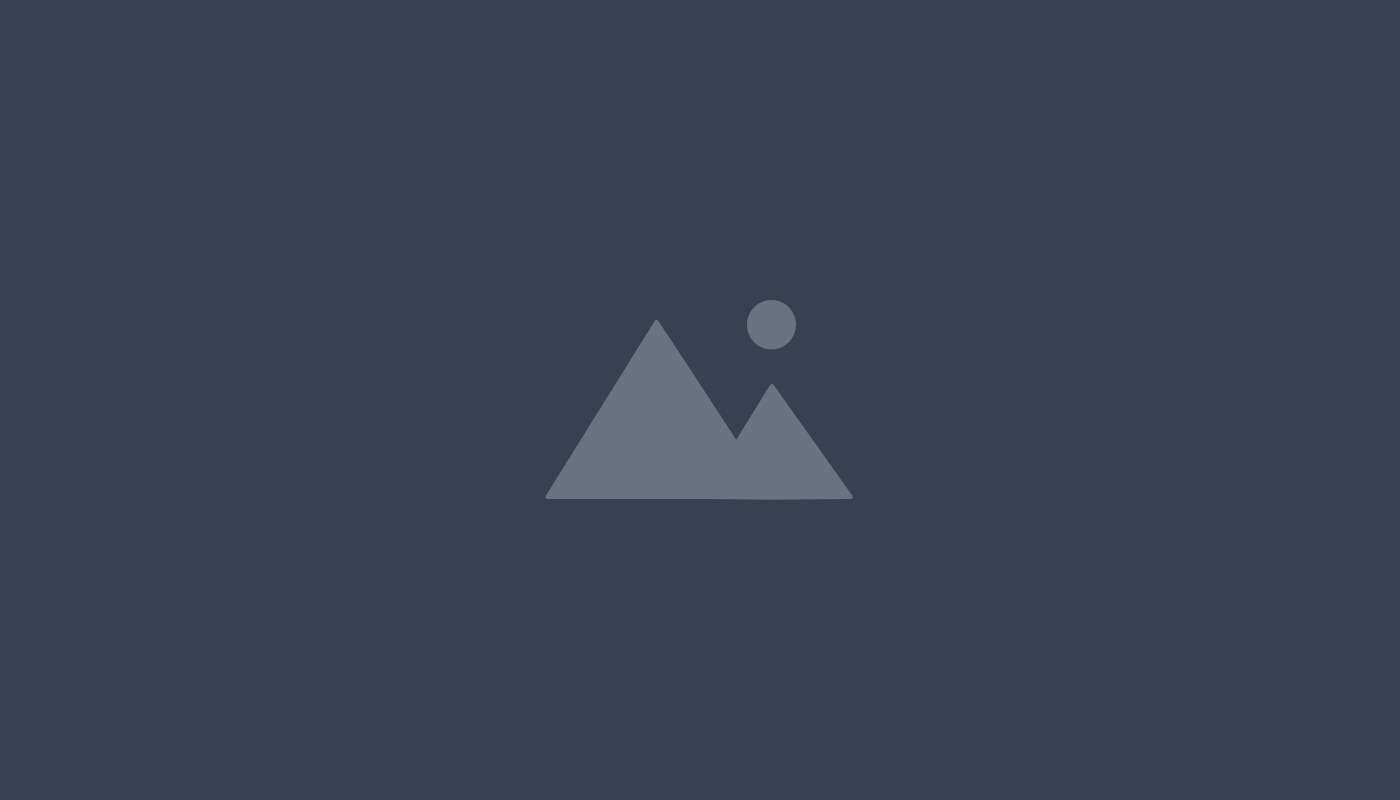
Anonymous
458
Skills
Level 1 Technician
93
Level 1 Technician
93
- Identify and describe the use of personal safety equipment.
- Identify and neutralize shop safety hazards.
- Identify and neutralize equipment hazards.
- Perform Lockout/Tagout on a Forklift
- Lift and Block a Forklift
- Fabricate hydraulic Hoses
- Remove and install forks
- Remove and install an attachment
- Battery maintenance (clean battery)
- Clean a battery
- Demonstrate ability to test battery
- Inspect battery box(es)
- Charge industrial batteries
- Check battery charge
- Remove and install industrial batteries
- Save, move, copy a file
- Create a folder
- Locate parts information
- Create a parts list
- Conduct a search
- Locate performance specs
- Locate schematics
- Locate tool information
- Locate the product fluid capacities and type
- Locate product maintenance interval schedule
- Locate product maintenance procedures
- Locate the product systems and product parts in the parts manual
- Locate product procedures and specs
- Locate product grams and bulletins
- Locate and use the Knowledge Base in contact management
- Demonstrate how to access the “S” Drive
- Dispose oil from a container
- Dispense oil from a container
- Dispose of an oil filter
- Check the engine oil level
- Check the engine coolant level
- Change the engine oil and filter
- Change a primary fuel filter
- Change a secondary fuel filter
- Check the transmission oil level
- Change transmission filter
- Check the oil level in a differential
- Inspect and clean a differential breather element
- Grease a carriage
- Grease a fork truck mast
- Identify all three carriage classes and differences
- Inspect/replace LP tank
- Locate the fuse box or circuit breaker
- Operate a circuit breaker
- Identify the maximum load capacity of a single lifting device
- Lift a load using a chain slight lifting device
- Lift a load using a nylon sling lifting device
- Select, adjust, and position a jack stand under load
- Clean a forklift with a pressure washer
- Clean a part with a solvent parts washer or spray cleaner
- Assemble a hose with a press
- Demonstrate the ability to properly use hand tools
- Tighten a bolt to standard using a torque wrench
- Grease a joint using a manual grease gun
- Measure a part using a steel ruler or tape measure
- Identify thread pitch
- Remove a lip seal using a seal puller
- Remove a piece part using a hydraulic puller
- Direct the operation of a hoist using hand signals
- Identify thread fasteners
- Identify fastener types
- Cut internal threads
- Cut external threads
- Resize a hole
- Repair a thread
- Repair a stud
- Remove and install a rivet
- Remove and install an o-ring seal
- Remove and install a cylinder packing ring
- Remove and install a gasket
- Remove and replace a liquid gasket
- Remove and install a coolant hose
- Remove and install hydraulic hose armor
- Remove and install a solid bearing
- Remove and install a sleeve bearing or bushing
- Install a bearing, utilizing a bearing heater
- Clean a used component for reinstallation
- Protect and store a part to be reinstalled
- Internal combustion (IC) truck operation
- 4-wheel electric operation
- 3-wheel electric operation
- Pallet truck operation
- Reach truck operation
- Order picker operation
- Very narrow aisle operation
- Aerial platform operation
- Trailer spotter operation
- Rail car operation
Level 2 Technician
147
Level 2 Technician
147
- Re-shim carriage
- Remove / install carriage hose(s)
- Remove / install carriage cylinder(s)
- Remove / install attachment(s)
- Check axle for leaks
- Identify axle fluid types and applications
- Check / fill axle fluid level
- Remove / install drive axle shafts
- Remove / install drive axle / differential
- Replace battery and connectors
- Perform alternator output test
- Perform diagnostics with PCST and/or Dash Display (T)
- Perform IC battery voltage drop test
- Replace battery IC truck
- Identify and troubleshoot battery issues
- Remove / replace forklift brakes
- Troubleshoot forklift brake system
- Fill / bleed forklift brake system
- Replace forklift wheel cylinders
- Replace forklift master cylinder
- Replace forklift brake booster
- Check / adjust forklift hand/ foot brake
- Demonstrate Spectrum Software a. connect to system b. show understanding of the software
- Demonstrate PSI Software a. connect to system b. show understanding of software c. view data log and codes
- Demonstrate ZAPI console or handset a. connect to system b. show understanding of the software c. view data log and codes
- Demonstrate 4G Software a. connect to system b. show understanding of the software c. view data log and codes
- Demonstrate ETACC a. connect to system b. show understanding of the software c. retrieve fault codes
- Demonstrate PCST a. connect to system b. retrieve passwords c. retrieve fault codes d. run truck diagnostics e. retrieve troubleshooting manual
- Demonstrate GCP Software a. connect to system b. show understanding of the software c. view data log and codes
- Demonstrate how to access the S: drive
- Search for a part and part number
- Search for lubrication type and refill capacities
- Search for Grams
- Search for Service Bulletins
- Search for PM schedules
- Convert production part numbers to Hyster / Yale part numbers
- Search for disassembly and assembly procedures
- Search for fork truck specifications
- Email and text a manager/supervisor/trainer
- Create a custom data monitor and strip chart in PCST
- Prepare job service records
- Demonstrate a clean and organized work van / shop work area
- Save a file on a PC
- Create a file on a PC
- Download and install CDF
- Navigate in Microsoft Word
- Navigate in Microsoft Excel
- Drain / refill cooling system
- Check cooling system for leaks
- Inspect / replace water pump
- Check / replace radiator hoses
- Check / replace thermostat
- Inspect / replace fan
- Inspect / replace fan drive
- Check / replace radiator
- Test a diode
- Test a resistor
- Test a fuse
- Check / repair / disassemble wiring harness connector
- Check / replace ignition switch
- Check / replace sensors
- Check / replace switches
- Check / repair display dash
- Check inputs vs. outputs on VSM for operations
- Repair contactor switch assemblies
- Troubleshoot basic control module problems
- Locate and interpret trouble codes
- Identify and troubleshoot ground to frame
- Remove and replace drive motors
- Demonstrate a thorough understanding of an electrical schematic
- Check / repair lights
- Check / repair / replace wiring / wiring harness
- Replace and adjust a potentiometer
- Replace intake gaskets
- Replace exhaust gaskets
- Check / replace O2 sensors
- Check / replace muffler
- Check catalytic converter back pressure and replace as needed
- Remove and install exhaust pipe and gaskets
- Check / run Regen in PCST
- Perform an engine tune up
- Identify engine fluid types and applications
- Check / adjust engine valves
- Check / adjust engine ignition timing
- Remove and install spark plugs and wires
- Test LP lockoff
- Inspect / replace tank
- Fill LP tank
- Check / rebuild / replace LP vaporizer / LP converter / regulator
- pressure
- Replace LP trim valve / injector
- Check / adjust throttle pedal and linkage
- Check / adjust throttle body
- Inspect / replace LP hoses
- Check system for hydraulic leaks
- Check / inspect hydraulic valve
- Check / adjust relief valve
- Check / calibrate mini levers
- Disassemble / assemble hydraulic cylinder
- Perform pressure test on hydraulic pump
- Remove / install hydraulic hoses
- Remove / install hydraulic pump
- Identify fluid type and application
- Fabricate hydraulic hose(s)
- Fill hydraulic cylinder
- Remove / install hydraulic cylinder
- Demonstrate a thorough understanding of a hydraulic schematic
- Inspect fork truck mast
- Service fork truck mast
- Remove / install load chains
- Remove / install load rollers
- Install / repair / replace strobe lights
- Install / repair / replace alarms
- Install / repair / replace lights
- Identify attachment data plates / capacities / applications
- Identify 3 carriage classes and differences
- Identify antifreeze type and use
- Inspect forks
- Inspect fork truck lift chains
- Inspect fork truck tires
- Perform a scheduled PM inspection on an electric truck
- Perform a pre-delivery inspection on an electric truck
- Perform a scheduled PM inspection on an IC truck
- Perform a pre-delivery inspection on an IC truck
- Clean a forklift with a pressure washer
- Clean a part with a solvent parts washer or spray cleaner
- Assemble a hose with a press
- Chock forklift
- Lift and block a forklift
- Check steering system
- Remove and install steering pump and steering motors
- Remove / install steer axle spindles
- Remove / install steer axle wheel bearings
- Remove / install tie rods and bushings
- Remove / install steering wheel
- Remove / install steering cylinder
- Disassemble / assemble steering cylinder
- Remove / install steering hoses
- Remove / install steer axle
- Identify transmission fluid types and application
- Calibrate transmission valve and speed sensor
- Manually service / adjust transmission linkage
- Troubleshoot / repair directional control problems
- Check / fill transmission fluid
- Inspect / repair transmission leaks
- Remove / install transmission oil cooler
- Check / adjust inch / brake overlap electronically
Level 3 Technician
121
Level 3 Technician
121
- Re-shim carriage
- Remove / install carriage hoses
- Remove / install carriage cylinders
- Remove and replace chain and carriage rollers
- Remove and install axle
- Remove and install differential housing
- Replace planetary drives
- Replace ring gear and pinion
- Rail Car Mover: Test / adjust air brake pressure circuit
- Rail Car Mover: Drain moisture from tanks
- Rail Car Mover: locate and read pneumatic schematics to troubleshoot system
- Rail Car Mover: test / adjust the governor cut-in/cut-out pressure for aux air compressor
- Rail Car Mover: locate appropriate service information
- Trailer Spotter: Drain moisture from tanks
- Trailer Spotter: locate appropriate service information
- Trailer Spotter: locate and read pneumatic schematics to troubleshoot system
- Forklift: diagnose / repair electric parking brake system
- Forklift: perform complete overhaul of a brake system
- Repair wat brakes parking linkage (binding)
- Replace wet brakes or hub/wheel seal
- Demonstrate 4G Software a. connect to system b. show understanding of the software c. view data log and codes
- Demonstrate GCP Software a. connect to system b. show understanding of the software c. view data log and codes
- Demonstrate Spectrum Software a. connect to system b. show understanding of the software c. view data log and codes
- Demonstrate ETACC a. connect to system b. show understanding of the software c. retrieve fault codes
- Demonstrate PSI Software a. connect to system b. show understanding of software c. view data log and codes
- Demonstrate ZAPI console or handset a. connect to system b. show understanding of the software c. view data log and codes
- Demonstrate how to access the S: drive
- Download and install CDF
- Demonstrate use of common controls system field service tool
- Demonstrate use of Dana Transmission Software
- Demonstrate use of Parker Node Software
- Demonstrate use of Plus 1 Hydraulic Software
- Demonstrate use of ZF Test Man Software
- Demonstrate use of Class 1 and 2 Field Service Tool
- Demonstrate use of Cummins Insite
- Demonstrate use of JLG/AWP handset
- Drain / refill cooling system
- Inspect / replace water pump
- Check / replace radiator
- Perform a temperature drop test
- Perform a cooling system pressure test
- Perform alternator output test
- Test and replace relay
- Test and replace solenoid
- Check inputs vs. outputs on VSM for operations
- Remove and replace drive motor
- Troubleshoot and repair advanced control panel system
- Test a diode
- Test a fuse
- Test a resistor
- Troubleshoot and repair a wiring harness
- Diagnose and repair electric steering system
- Demonstrate a thorough understanding of an electrical schematic
- Diagnose and repair wire guidance
- Check / run regen in PCST
- Replace intake gaskets
- Diagnose and repair / replace EGR
- Diagnose and repair / replace diesel oxidation catalyst
- Diagnose and repair / replace SCR components
- Perform a complete diagnostic check of a forklift Tier 4 Emission System
- Replace exhaust gaskets
- Check / replace O2 sensors
- Check / replace muffler
- Check catalytic converter back pressure and replace as needed
- Remove and install exhaust pipe and gaskets
- Identify emission fault codes and make recommendations
- Identify blown head gasket failure and repair
- Check / adjust engine valves
- Check / adjust engine ignition timing
- Remove and install spark plugs and wires
- Identify timing belt failure and repair
- Reseal engine oil leaks (oil pan, valve covers, and/or manifold)
- Perform a complete engine tune-up
- Remove and install engine (rebuilt)
- Remove and install flywheel
- Test LP Lockoff
- Replace LP converter / regulator
- Troubleshoot / repair LP fuel system
- Check and drain LP converter
- Replace LP lockoff
- Check / rebuild / replace LP vaporizer / LP converter / regulator pressure
- Replace LP trim valve / injector
- Check / adjust throttle pedal and linkage
- Check / adjust throttle body
- Test and clean LP trim valve / injector
- Check / adjust relief valve
- Perform pressure test on hydraulic pump
- Locate appropriate service information to support diagnosis of a trailer spotter hydraulic system
- Locate appropriate service information to support diagnosis of a rail car mover hydraulic system
- Perform a complete diagnosis of a common hydraulic system
- Perform a complete diagnosis of an e-hydraulic system
- Perform a complete diagnosis of a load sensing swash plate pump
- Demonstrate thorough understanding of a hydraulic schematic
- Measure rail wheels
- Replace rail wheels
- Perform maintenance on trailer spotter fifth wheel
- Identify antifreeze type and use
- Perform MEWP annual inspection
- Perform rail car mover scheduled maintenance
- Perform trailer spotter scheduled maintenance
- Perform MEWP frequent inspection
- Assemble a hose with a press
- Perform lockout/tagout on a forklift
- Lift and block a forklift
- Replace steering gear
- Perform overhaul or multipart replacement of a steering axle
- Set up electric steering and wire guidance system
- Troubleshoot steering system
- Replace steering pump
- Replace steering valve
- Replace or rebuild steering cylinders
- Troubleshoot / repair directional control problems
- Calibrate transmission valve and speed sensor
- Troubleshoot trailer spotter Allison transmission
- Troubleshoot Dana transmission
- Troubleshoot ZF transmission
- Pressure test transmission with PCST and dash
- Reseal transmission control valve
- Remove and install transmission
- Demonstrate proper operation rail car
- Demonstrate proper operation rail car sander system
Level 4 Technician
97
Level 4 Technician
97
- Perform battery voltage drop test
- Troubleshoot and repair starting system
- Perform diagnostics with PCST and/or dash display
- Identify and troubleshoot battery issues
- Forklift Air Brake System: locate appropriate service information
- Forklift Air Brake System: drain moisture from tanks
- Forklift Air Brake System: test/adjust governor cut-in / cut-out pressure for engine air compressor
- Forklift Air Brake System: locate and read pneumatic schematics to troubleshoot system
- Forklift Air Brake System: operationally test the pneumatic system to verify compressor cycles and correctly purge air dryer
- Forklift Air Brake System: test / adjust air brake pressure circuit
- Rail Car Air Brake System: locate appropriate service information
- Rail Car Air Brake System: drain moisture from tanks
- Rail Car Air Brake System: locate and read pneumatic schematics to troubleshoot system
- Rail Car Air Brake System: operationally test the pneumatic system to verify compressor cycles and correctly purge air dryer
- Rail Car Air Brake System: test / adjust air brake pressure circuit
- Rail Car Air Brake System: test / adjust governor cut-in / cut-out pressure for the aux air compressor
- Rail Car Air Brake System: test / adjust governor cut-in / cut-out pressure for the engine air compressor
- Trailer Spotter Air Brake System: locate appropriate service information
- Trailer Spotter Air Brake System: drain moisture from tanks
- Trailer Spotter Air Brake System: locate and read pneumatic schematics to troubleshoot system
- Trailer Spotter Air Brake System: operationally test the pneumatic system to verify compressor cycles and correctly purge air dryer
- Trailer Spotter Air Brake System: test / adjust air brake pressure circuit
- Trailer Spotter Air Brake System: test / adjust governor cut-in / cut-out pressure for the engine air compressor
- Forklift: perform complete overhaul of a brake system
- Forklift: diagnose / repair parking brake system
- Demonstrate 4G Software a. connect to system b. show understanding of the software c. view data log and codes
- Demonstrate GCP Software a. connect to system b. show understanding of the software c. view data log and codes
- Demonstrate ETACC a. connect to system b. show understanding of the software c. retrieve fault codes
- Demonstrate use of common controls system field service tool
- Demonstrate use of Dana Transmission software
- Demonstrate use of Plus 1 Hydraulic software
- Demonstrate use of ZF Test Man software
- Demonstrate use of Class 1 and Class 2 field service tool
- Demonstrate use of Parker Node software
- Perform a radiator temperature drop test
- Perform a cooling system pressure test
- Check CANbus
- Check / repair display dash
- Check inputs vs. outputs on VSM for operations
- Repair contactor switch assemblies
- Troubleshoot and repair advanced control panel system
- Troubleshoot basic control module problems
- Locate and interpret trouble codes
- Identify and troubleshoot ground to frame
- Remove and replace drive motors
- Diagnose and repair electric steering system
- Replace and adjust a potentiometer
- Diagnose and repair wire guidance system
- Check and replace regen components (DPF)
- Diagnose and repair / replace EGR
- Diagnose and repair/replace diesel oxidation catalyst
- Diagnose and repair / replace SCR components
- Perform a complete Diagnostic Check of a forklift Tier 4 emission system
- Check / replace O2 sensors
- Check catalytic converter back pressure and replace as needed
- Remove and install exhaust pipe and gaskets
- Identify emission fault codes and make recommendations
- Identify blown head gasket failure and repair
- Identify timing belt failure and repair
- Remove and install engine (rebuilt)
- Remove and install flywheel
- Test LP lockoff
- Replace LP converter/regulator
- Troubleshoot / repair LP fuel system
- Check and drain LP coverter
- Replace LP lockoff
- Check, rebuild, replace LP vaporizer, LP converter, regulator pressure
- Replace LP trim valve/injector
- Check and adjust throttle pedal and linkage
- Check and adjust throttle body
- Test LP converter / regulator pressure
- Test and clean LP trim valve / injector
- Test boom cylinder performance and adjust to specs to support diagnosis of trailer spotter hydraulic system
- Locate and interpret hydraulic schematic and trace system circuits to support diagnosis of trailer spotter hydraulic system
- Test and list main pump pressure and GPM, adjust to specs to support diagnosis of trailer spotter hydraulic system
- Locate appropriate service information to support diagnosis of trailer spotter hydraulic system
- Drain hydraulic system, replace fluid and filters, and prime system prior to start to support diagnosis of rail car mover hydraulic system
- Locate and interpret hydraulic schematics to trace system circuits to support diagnosis of rail car mover hydraulic system
- Properly raise and support unit (prior to getting under) to support diagnosis of rail car mover hydraulic system
- Release static hydraulic pressure from system to support diagnosis of rail car mover hydraulic system
- Test and adjust and list max system pressure to support diagnosis of rail car mover hydraulic system
- Test and adjust and list stand-by pressure to support diagnosis of rail car mover hydraulic system
- Locate appropriate service information to support diagnosis of rail car mover hydraulic system
- Perform a scheduled PM inspection on an electric truck
- Perform rail car mover scheduled maintenance
- Perform trailer spotter scheduled maintenance
- Perform a pre-delivery inspection on an electric truck
- Perform a scheduled PM inspection on an IC truck
- Perform a pre-delivery inspection on an IC truck
- Assemble a hose with a press
- Perform lock-out/tag-out on a forklift
- Lift and block a forklift
- Diagnose/test TISS and TOSS
- Calibrate speed sensor
- Calibrate transmission valve
- Pressure test transmission with PCST and dash
- Run strip chart or custom data monitor for transmission diagnostics
Related Instruction Content
Training Provider(s):
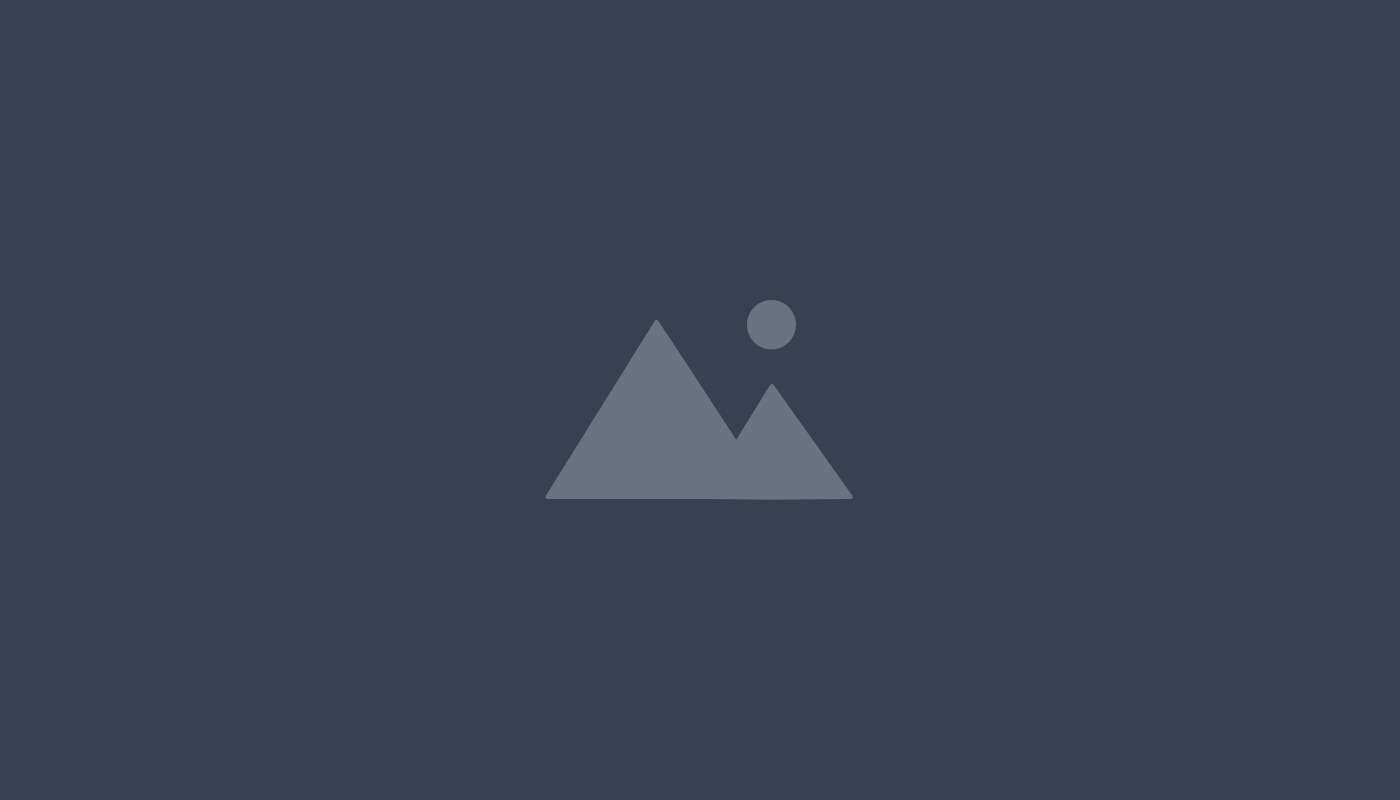
LiftOne
Apprenticeship Orientation
Apprenticeship Orientation
Level 1 Technician: Maintenance Technician Certification
Level 1 Technician: Maintenance Technician Certification
Level 2 Technician: Service Technician Certification
Level 2 Technician: Service Technician Certification
Level 3 Technician
Level 3 Technician
Level 4 Technician
Level 4 Technician
Level 5 Technician
Level 5 Technician