in on-the-job training and related instruction.
Tool & Die Specialist
Tesla, Inc.
Work Process Content
On the Job Training
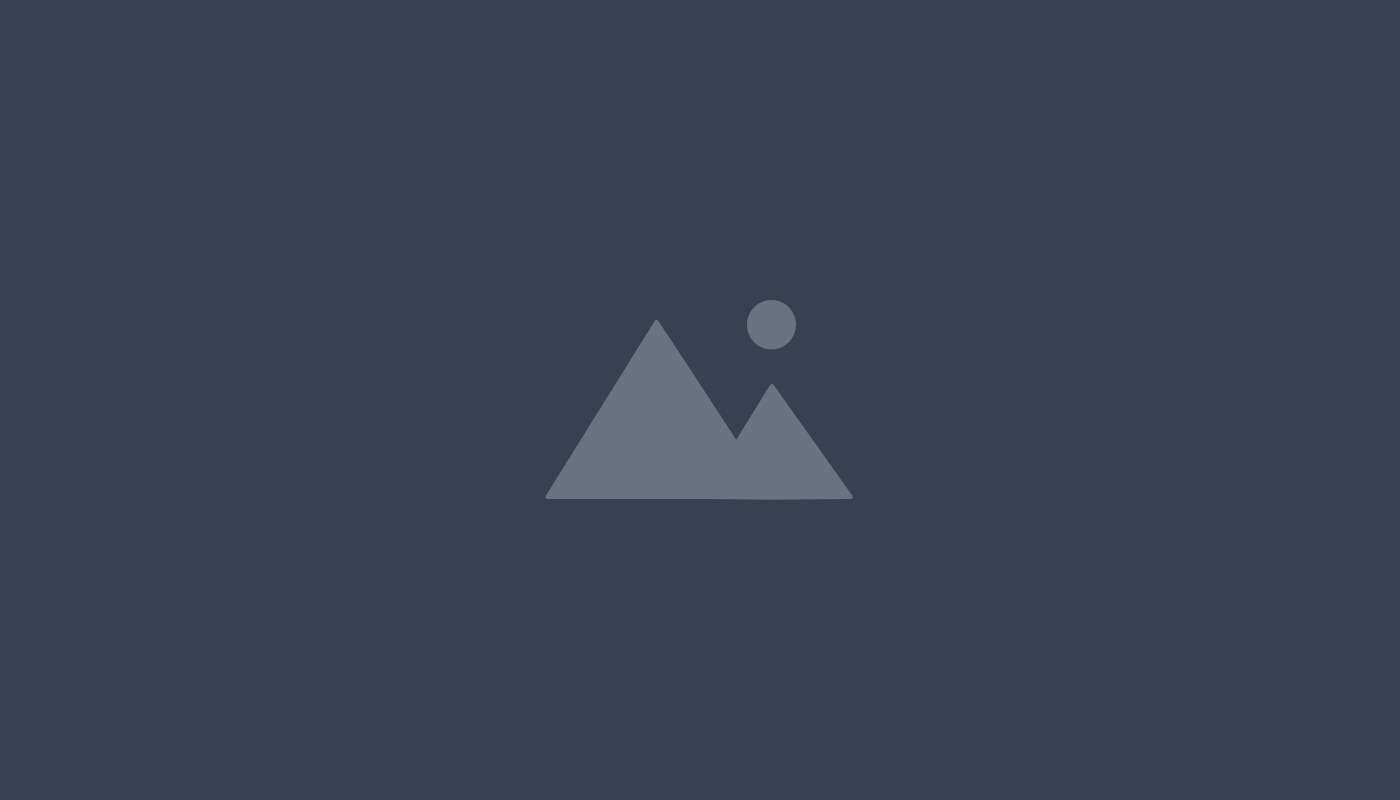
Safety
0
350
• Identify health and safety hazards. • Wear, adjust, and maintain personal protective equipment. • Practice safe work habits. • Operate emergency safety equipment. • Conduct preoperational check of equipment. • Report injuries. • Lock out mechanical equipment for repair. • Handle designated substances. • Operate lifting equipment. • Communicate with co-workers. • Identify and select lifting and rigging equipment.
Perform Bench Work
0
450
• Hand-File. • Hand-saw. • Hand-drill holes. • Hand-tap threaded holes. • Hand-grind. • Practice good housekeeping • Stone and polish.
Layout
0
380
• Read and interpret engineering drawings. • Perform calculations for machining operations. • Read and interpret work process documentation • Verify workpiece material. • Identify and select machines. • Identify and check machine controls and systems. • Identify and select tooling. • Identify and prepare cutting tools. • Identify and select measuring instruments and checking devices. • Select machine speeds and feeds. • Lay out features of engineering drawings. • Identify and select workholding devices. • Pick-up datum/starting position.
Saw
0
350
• Make, install, and test-run blade. • Locate and position workpiece in saw. • Select speeds and feeds of saw. • Cut shapes using a vertical bandsaw. • Maintain material identification. • Practice good housekeeping. • Identify and select proper workholding techniques. • Proper blade guarding and adjustments.
Drilling
0
550
• Select drill tooling. • Inspect and prepare cutting tools for drilling. • Locate and position workpiece in drill. • Set-up tooling in the machine. • Select speeds and feeds of cutting. • Layout and make a punch mark. • Drill a hole. • Chamfer a hole. • Ream a hole. • Machine-thread a hole. • Spot-face a hole. • Counter-bore a hole. • Counter-sink a hole. • Perform final inspection. • Practice good housekeeping.
Grinding
0
550
• Select grinding wheel. • Check condition of grinding wheel ring test. • Balance Wheel. • Install grinding wheel. • Dress Wheel. • Surface grind workpiece. • Grind tools and cutters. • Set-up sine plates. • Demagnetize workpiece. • Check ground surfaces. • Perform final inspection. • Locate and position workpiece on magnetic chuck.
Milling
0
950
• Verify machine head and workholding devices are square. • Establish and maintain part datum. • Identify and prepare milling cutting tools. • Select speeds and feeds of mill. • Develop and organize a prototype machining plan. • Square up blocks. • Drill and tap, ream, counter bore, counter sink. • Machine steps, cut-outs, angles, and open slots. • Machine a pocket or slot. • Establish grinding allowance. • Bore holes. • Deburr workpiece. • Indexing, 90 degree plate and rotary table.
Lathe
0
950
• Select lathe cutting tools. • Develop and organize a prototype machining plan. • Locate and position workpiece in lathe. • Establish and maintain part datum. • Set-up lathe cutting tools. • Select speeds and feeds of lathe. • Take a sizing (preliminary) cut. • Establish a reference or starting point (datum). • Face a surface. • Turn an external diameter. • Drill, bore, ream, a hole. • Produce a taper. • Groove and part off. • Knurling. • Cut an internal and external thread. • Offset / eccentric (four jaw chuck)
CNC Machining
0
250
• Identify, select, and set-up numerical control (NC) / Computer Numerical Control (CNC) cutting tools and tool holders. • Identify, select, and set machine parameters. • Position, align, & secure workpiece in NC / CNC machine. • Input and verify part program to NC / CNC machine controls. • Verify tool sequence, tool path, and collision avoidance program. • Monitor NC / CNC machining process. • Make adjustments to tooling and offsets. • Program machines using G-coding
Electrical Discharge Machining (EDM)
0
100
• Identify and select EDM process. • Develop EDM electrodes. • Identify, select, and set-up EDM machining components. • Position, align, and secure workpiece in EDM machine. • Cut the workpiece by EDM machine. * Some Tool & Die Specialties do not require EDM. Hours will be distributed to other work processes.
Tool & Die Processes
0
2K
• Open and close die / mold indicating proper assembly and disassembly. • Preventative maintenance. • Perform die / mold or tool-building related calculations. • Machine components of dies / molds, tools, jigs, or fixtures. • Heat-treat the components. • Mark the die / mold or tooling components. • Final fit sub-assemblies dies / molds, or tooling components. • Perform parting line changes / repairs. • Grinding, Stoning, Polishing. • Spotting. • Inspect die / mold or tooling fit and functions. • Set-up and operate press. • Try out and troubleshoot the die / mold. • Panel Nest. • Prepare and finalize cutting steels. • Set punches. • Perform mold cavity / core / changes / repairs, if applicable. • Texture repair, if applicable. • Basic electrical hot runner repair, if applicable.
Welding
0
1K
• Perform Metal Inert Gas (MIG), Tungsten Inert Gas (TIG), Oxy Acetylene (OXY), and Arc welding. • Select proper welding materials. • Pad welding techniques. • Perform J-hook technique. • Parting line weld repair, if applicable
Metallurgy
0
130
• Heat-treat the components. • Stress relief. • Normalize. • Temper. • Anneal. • Flame hardening. • Quenching types and process. • Identify materials and their properties.
Related Instruction Content
Training Provider(s):
Engineering Drawings
110
A course designed to provide the fundamental concepts in reading technical drawings required by machine shops, engineering, electrical and welding industries. The course will start with simple prints and proceed to more advanced prints. This course will cover geometric dimensioning and tolerancing concepts. It is designed to clarify the tolerance options and their potential use in the manufacturing process.
Machining – 1
110
Introduces safety procedures, use of bench tools, layout tools, power saws, drill presses, precision measurement tools, rotary tables and indexing devices, lathe and mill cutting tools and tool holding, work holding and machining applications as well as the various hand tools related to the machine shop.
Machining – 2
110
Introduces basic lathe applications which will consists of identifying lathe components and controls, understanding turning safety, calculating speeds and feeds, using various tools and tool holders, identifying basic tool geometry, and the use of common lathe tooling. Apprentices will perform basic lathe operations, which will consist of facing, turning, and drilling. Apprentices will be required to produce specified parts to a tolerance of +/- .004 in. and perform competencies set by manufacturing standards.
Machining – 3
110
Introduces basic milling machine applications which will consist of identifying mill components and controls, understanding milling safety, calculating speeds and feeds, using various tools and tool holders, identifying basic tool geometry, and the use of common milling machine tooling. Apprentices will perform basic milling operations consisting of facing, squaring, slotting, and drilling. Apprentices will be required to produce specified parts to a tolerance of +/- .004 in. and perform competencies set by manufacturing standards.
Intro to Welding (Or intro to MIG / TIG equivalent)
110
This course introduces the learner to the world of welding. The course includes general shop safety and environmental issues; introduction to oxygen/fuel gas supply systems, the oxyfuel cutting process, and the SMAW (Shielded Metal Arc-Welding) process; and an introduction to interpreting basic welding symbols. This course specifically develops basic SMAW skills as striking the arc, maintaining proper arc length, adjusting equipment and manipulating the electrode.
Welding – MIG / TIG 1
110
This course is a continuation of Intro to Welding and emphasizes SMAW vertical and overhead positions and machine oxyfuel gas cutting. In addition, the course introduces GMAW (gas metal arc welding) and air carbon arc cutting. This course satisfies 4 hours of instruction toward completing the embedded human relations curriculum requirements, in accordance with Embedded Curriculum Guidelines Option A. Ample practice time is allocated to perfect skills and complete lab assignments.
Welding – MIG/TIG 2
110
This course is a continuation of Welding – MIG/TIG 1 and places an emphasis on the Gas Tungsten Arc Welding (GTAW) process in all positions on ferrous and nonferrous materials. This course also covers the advanced Flux-Cored Arc Welding (FCAW) process and concentrates on the skills needed to pass the AWS (American Welding Society) certification test in all positions using the FCAW process. The Apprentice at this level of training may opt to develop skills in the welding of pipe using the SMAW or FCAW processes. At this point in training apprentices may also start developing skills necessary to weld pipe using the SMAW or FCAW processes. Ample practice time is allocated to perfect skills and complete lab assignments.
Welding Certification
53
This course prepares a apprentice to obtain the MIG / TIG welding certification.
Tool/Die/Mold 1
100
This course involves internal Tesla instruction to educate die and mold makers to maintain and troubleshoot Tesla specific dies/molds and use machines efficiently to design and fabricate the same. Apprentices learn the fundamentals of maintaining and troubleshooting jigs, molds, dies, and fixtures needed within the Tesla manufacturing process.
Tool/Die/Mold 2
100
This course is a continuation of Tool/Die/Mold 1 and involves internal Tesla instruction to educate die and mold makers to maintain and troubleshoot Tesla specific dies/molds and use machines efficiently to design and fabricate the same. Apprentices learn the fundamentals of maintaining and troubleshooting jigs, molds, dies, and fixtures needed within the Tesla manufacturing process.