Hybrid programs blend both competency- and time-based strategies,
using a minimum and maximum range of hours for each major job
function and the successful demonstration of identified competencies.
using a minimum and maximum range of hours for each major job
function and the successful demonstration of identified competencies.
Industrial Maintenance Technician
Anonymous
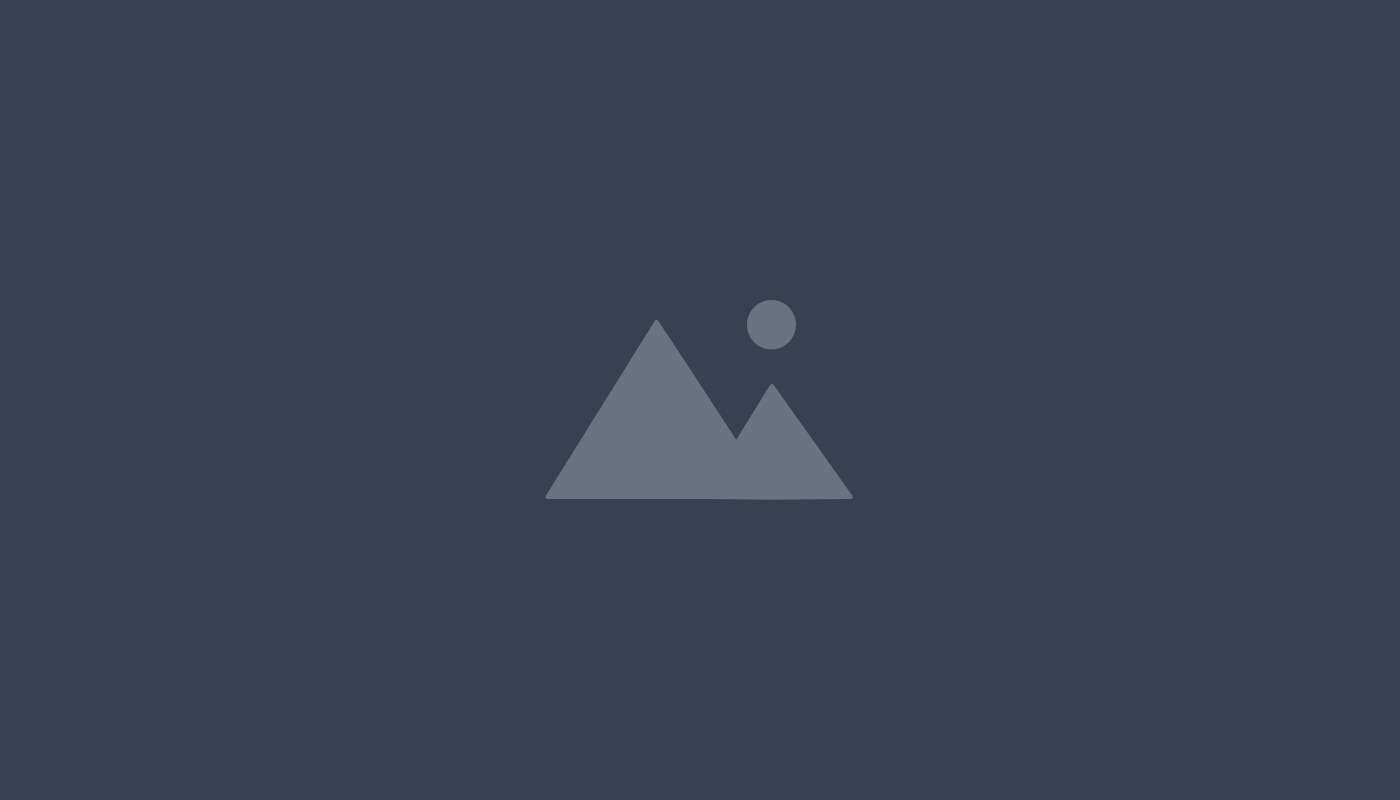
North Carolina (SAA)
Documents
View Redacted Document
Personal and employer info redacted
Individual state requirements may vary. Please contact your local apprenticeship office to ensure this version is suitable to your state’s requirements.
Work Process Content
On the Job Training
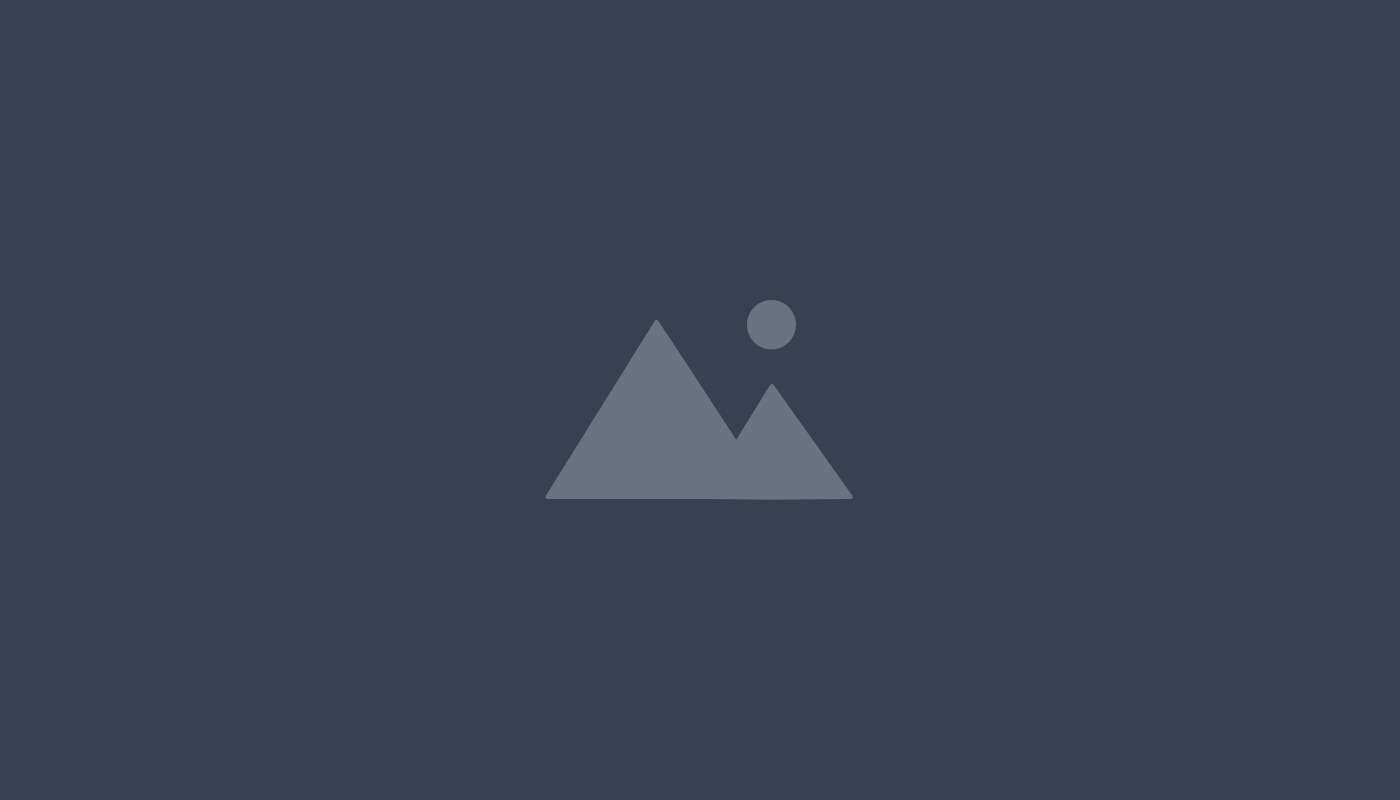
Anonymous
110
Skills
Safety
15
Safety
15
- Lockout/tag out machines power sources by installing lockout devices and voltage testers.
- Wear personal protective equipment (PPE) such as gloves, safety glasses, earplugs, arc flash gear, hot work equipment and steel toe shoes.
- Work safely by using PPE, lockout devices and multimeters.
- Communicate hazardous situations to all team members.
- Respond to machine alarms and support equipment when notified by process technicians or other personnel.
- Set up safety barriers when performing major maintenance on machines.
- Acquire hot work permits prior to performing grinding, torching or welding procedures outside of shop area by requesting from supervisor.
- Demonstrate proper handling and storage of lubrications and chemicals.
- Follow safety procedures for the use of all paints, solvents & other hazardous materials by reading & following MSDS online.
- Demonstrate working knowledge of different types of fire extinguishers and check for proper operating status and send out for recertification if needed.
- Complete annual fire extinguisher training.
- Complete First Responder and CPR training.
- Perform safety audit before working on machines identifying any and all possible safety issues.
- Understand safety precautions and demonstrate knowledge of process fluid systems.
- Complete and demonstrate safe electrical work practices (Arc flash NFPA 70E).
Documentation
8
Documentation
8
- Plan and lay out repair work, using diagrams, drawings, blueprints, maintenance manuals, and schematic diagrams.
- Complete job risk analysis or Take 5 White Board exercise when doing new job or one not done in over 6 months. List safety precautions needed.
- Procure parts using SAP and ETSR.
- Inventory machine parts, equipment, and other supplies so that stock can be maintained and replenished.
- Locate part numbers from machine manuals and communicate to procurement.
- Record type of maintenance or repair work and parts used in the corrective maintenance portion of the PM Scheduler.
- Record downtime of production when working on machine for repair, PM, written turnover for all tasks etc.
- Estimate repair costs by obtaining quotes from contractors and forward quotes to department managers for approval.
Installation/Setup
35
Installation/Setup
35
- Determine proper size and weight capacity of chains and straps by referring to known industry standards and rigging handbook.
- Determine size and capacity of relays and controllers by using multi-meter and referring to manufacturer's label.
- Ensure new site location for machine is adequately prepared by determining power sources, proper voltage of power and footing foundation.
- Install adjustable drive systems by calculating torque, size and horsepower requirements.
- Install hose by selecting proper size, classification, type, and hose coupling.
- Install motor switches and controls such as push button, contact blocks, limit switches, plugging switches, pressure switches and float switches by ensuring proper size and rating.
- Install single-phase, three-phase, AC/DC motors by ensuring proper conductor size, power source and alignment.
- Install pneumatic tubing by demonstrating knowledge of size, method, type and maintenance of tubing.
- Mount machine in new location by securing with proper anchoring bolts or leveling pads.
- Install filters, strainers, pressure gauges and traps.
- Protect motors and circuits by using proper overload protection such as fuses and thermal overload protection.
- Install metal pipe by demonstrating knowledge of pipe size, pipe joints, techniques and limitation of pipe.
- Transport machine parts, tools, equipment, and other material between work areas and storage, using cranes, hoists, air bags, or dollies.
- Inspect chains and straps for obvious defects by visual inspection.
- Install and align shafts/pulleys on belt drive systems by properly mounting pulley, belts. Install V-belts, timing and flat belts, sheaves, pulleys by demonstrating proper alignment and belt tension.
- Install chain drives (conveyor) by demonstrating proper sprocket alignment and chain tension.
- Install gears and equipment by setting proper gear mesh.
- Install oil filters in hydraulic systems as needed.
- Wire motor control centers according to National Electrical Code standards.
- De-energize machine by disconnecting all power sources and utilities such as electrical, pneumatic, hydraulic, and water.
- Install, replace, or change machine parts and attachments, according to machine specifications.
- Reconnect power systems to machine such as electrical, hydraulic, pneumatic, and water by utilizing known industrial standards.
- Set up and maintain robots by installing end of arm tooling (eoat), creating and loading program, and editing operational program.
- Set up and operate machines, and adjust controls to regulate operations.
- Adjust functional parts of devices and control instruments, using hand tools, levels, plumb bobs, and straight edges.
- Install and remove auxiliary equipment (i.e. Hydraulics, H2O temp control, conveyors, loaders, air compressors, chillers) from machines as indicated.
- Monitor hydraulic systems ( pumps, nitrogen accumulation systems) by determining pressure, speed and efficiency.
- Prime machine by bleeding off pressure (hydraulic, pneumatic, water) from lines, cylinders and pumps.
- Properly align shaft couplings by using alignment tools such as combination square, straight edge and feeler gages, or dial indicators.
- Build and troubleshoot assembly stations by following specifications from engineering and utilizing knowledge of Assembly process.
- Remove hardened material from machines or machine parts, using abrasives, power and hand tools, air chisels, sledgehammers, or other equipment.
- Evaluate open and closed gear drives by inspecting gear tolerances and lubrication.
- Mount gear drives by determining gearbox configuration, ratios and horsepower ratings.
- Remove and install bearings by determining proper tolerances on housing and shafts and by using proper bearing handling/installation practices.
- Set up assembly line equipment within established parameters.
Corrective/Preventative Maintenance
17
Corrective/Preventative Maintenance
17
- Disassemble machines and parts, and adjust, repair or replace defective parts and materials.
- Read work orders and specifications to determine machines and equipment requiring repair or maintenance.
- Repair or replace defective equipment parts, using hand tools and power tools, and reassemble equipment.
- Calibrate hydraulic pumps using amplifier and pressure gauge to check for pressure and voltage output following documented procedures.
- Inspect or test damaged machine parts, and mark defective areas or advise supervisors of repair needs.
- Relieve hydraulic pressure from system prior to initiating repairs.
- Energize machine and test run to ensure proper machine function.
- Inspect drives, motors, and belts, check fluid levels, replace filters, or perform other maintenance actions.
- Maintain controllers for correct out voltage by using Multi-meter and checking brushes and motor.
- Consult manufacturers manuals to locate checklist to follow when performing preventative maintenance.
- Lubricate or apply other materials to machines, machine parts, or other equipment, according to specified procedures.
- Overhaul pumps such as centrifugal, hydraulic, pneumatic and gear pumps by properly removing, disassembling, and reinstalling pumps.
- Replace chain, gear and rubber shaft couplings by determining proper clearances and alignment.
- Clean machines and machine parts, using cleaning solvents, cloths, air guns, hoses, vacuums, or other equipment as scheduled.
- Clean and lubricate shafts, bearings, gears, and other parts of machinery.
- Conduct monthly inspection on hoists, chains, and straps following printed inspection form.
- Determine type of lubricants required for various applications by understanding classifications, effects of lubricants, viscosity, types of additives.
Troubleshooting
12
Troubleshooting
12
- Determine motor starters and thermal overload by referring to manufacturers label on motor and known industry standards.
- Diagnose mechanical problems and determine how to correct them, checking blueprints, repair manuals, and parts of catalogs as necessary.
- Start machines and observe mechanical operation to determine efficiency and to detect problems.
- Test and troubleshoot electrical systems and circuits for current, resistance, and potential differences by using Multi-meter and Amp meter.
- Troubleshoot relay failures by demonstrating knowledge of timer, counters and relays, such as time delay relays, repeat-cycle timers, voltage sensing relays, phase sequence-sensing relays and NEMA classes of relays.
- Troubleshoot electrical circuits by using voltmeter and amp probe to measure direct and alternating current.
- Check for leaks by observing machine in operation being sure to run through all machine functions.
- Monitor motors for incorrect speed, noise, vibration, temperature and bearing problems.
- Test three phase motors by using Multi-meter to read resistance between any two legs of the three-phase system or from any leg to ground and check for proper rotation.
- Troubleshoot valve, cylinders, motors and piping components by testing procedures, problem diagnosis, and root cause analysis.
- Troubleshoot Inputs/ Outputs using schematics and meters.
- Troubleshoot using PLC/ Ladder Logic.
Facility
14
Facility
14
- Install and maintain plant wide water systems ( tower & chiller, water to machines, etc.).
- Maintain plant wide compressed air systems by completing daily checklist and performing minor repairs when needed.
- Check valves on pipes delivering city water supply monthly by partially closing valve to test functionality.
- Install and repair rapid roll doors to create air locks between production and storage areas.
- Run network cables and data drops for computers and machines.
- Install electronic equipment in conference rooms.
- Paint and repair doors, floors, drywall, concrete, and other parts of building structures.
- Repair loading dock systems ( electrical and hydraulic systems) when needed.
- Maintain lines, pumps and controls for cooling water to machines by checking pressure, leaks, temperatures, etc.
- Repair and maintain electrical systems ( security alarms, electric doors, fire alarms, etc.).
- Maintain lighting systems by installing, changing, repairing and moving fixtures.
- Perform water treatment analysis on cooling towers weekly and make adjustments based on findings.
- Troubleshoot HVAC system and repair or reset minor issues and contact contractor for major issues.
- Fabricate and repair counters, benches, partitions, or other wooden structures, such as sheds and outbuildings.
Miscellaneous
9
Miscellaneous
9
- Collaborate with other workers to repair or move machines, machine parts, or equipment.
- Reads and interprets documents such as technical manuals, blueprints, safety rules, operating instruction and procedure manuals.
- Set up and operate machines tools to repair or fabricate machine parts, jigs and fixtures, and tools.
- Use a variety of basic hand and power tools and equipment including hand drill, bench grinder and band saw.
- Inspect used parts to determine changes in dimensional requirements, using rules, calipers, micrometers, and other measuring instruments.
- Collect and discard worn machine parts and other refuse in order to maintain machinery and work areas.
- Coordinate with production schedules to perform repair or maintenance requiring downtime on machines.
- Maintain a clean, safe work environment by following 5S procedures and good general housekeeping practices.
- Train and demonstrate proficiency in forklifts, aerial boom lifts and scissor lifts.
Related Instruction Content
Training Provider(s):
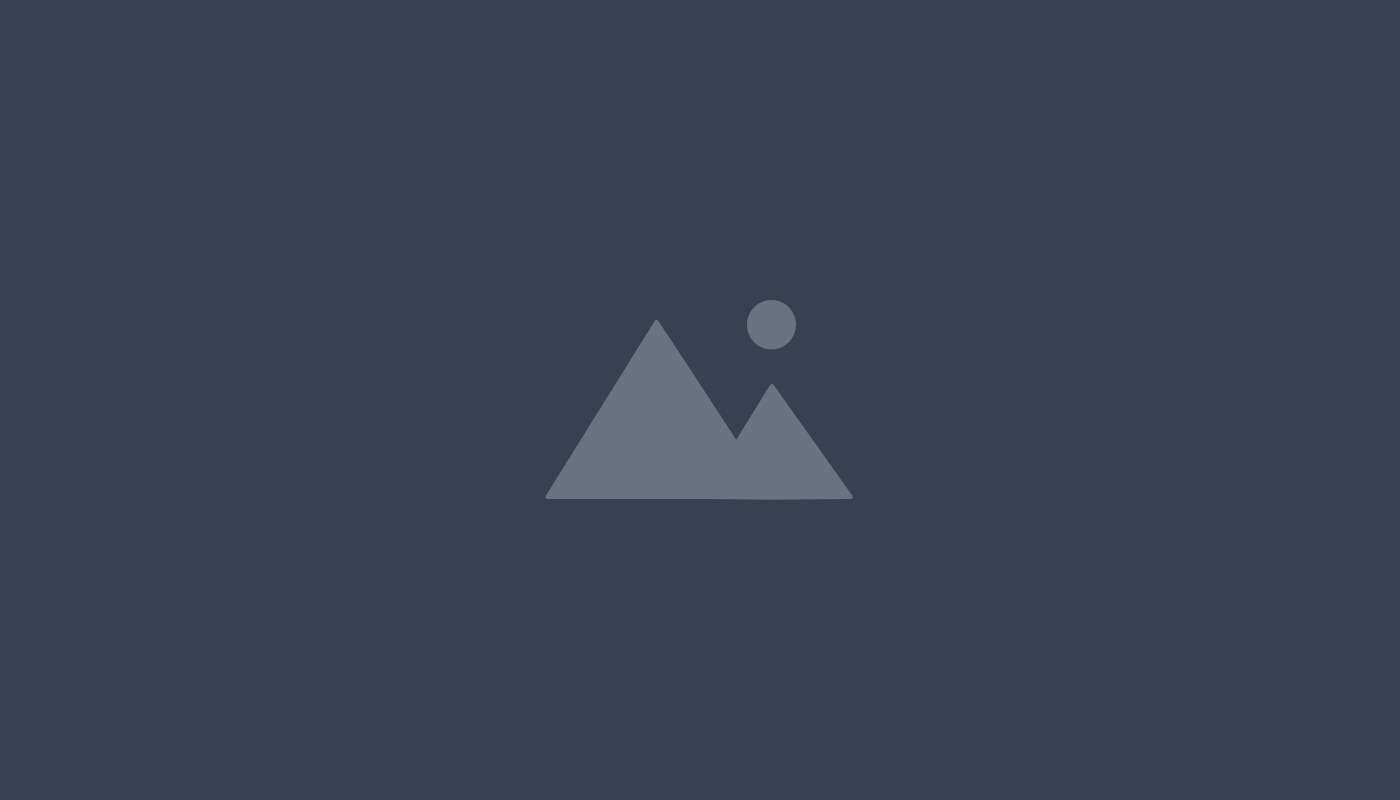
Wilkes Community College
Blue Print Reading
Blue Print Reading
Hydraulics/Pneumatics I
Hydraulics/Pneumatics I
Basic Welding Processes
Basic Welding Processes
Metalworking Processes
Metalworking Processes
Mechanical Industrial Systems
Mechanical Industrial Systems
Introduction to PLC
Introduction to PLC
Basic CAD
Basic CAD
Introduction to Automation
Introduction to Automation
Appl Software for Tech
Appl Software for Tech
Industrial Equipment Troubleshooting
Industrial Equipment Troubleshooting
Circuit Analysis I
Circuit Analysis I
Workplace Safety
Workplace Safety
Intro to GD&T
Intro to GD&T
Metrology
Metrology
CNC Turning
CNC Turning
CNC Milling
CNC Milling
Lean Manufacturing
Lean Manufacturing