in on-the-job training and related instruction.
Heating, Air Conditioning, & Refrigeration Installer/Servicer
CMS Mechanical Services, LLC.
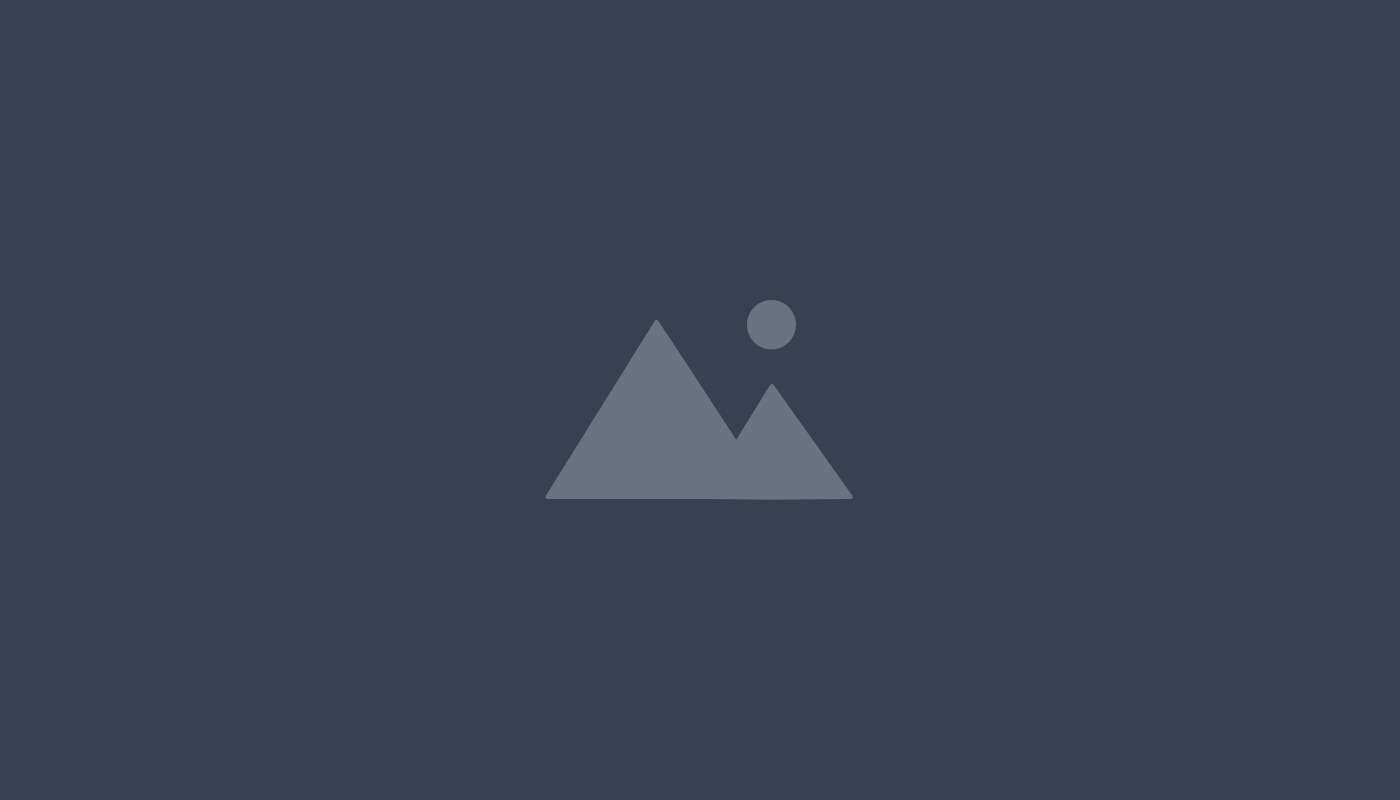
Work Process Content
On the Job Training
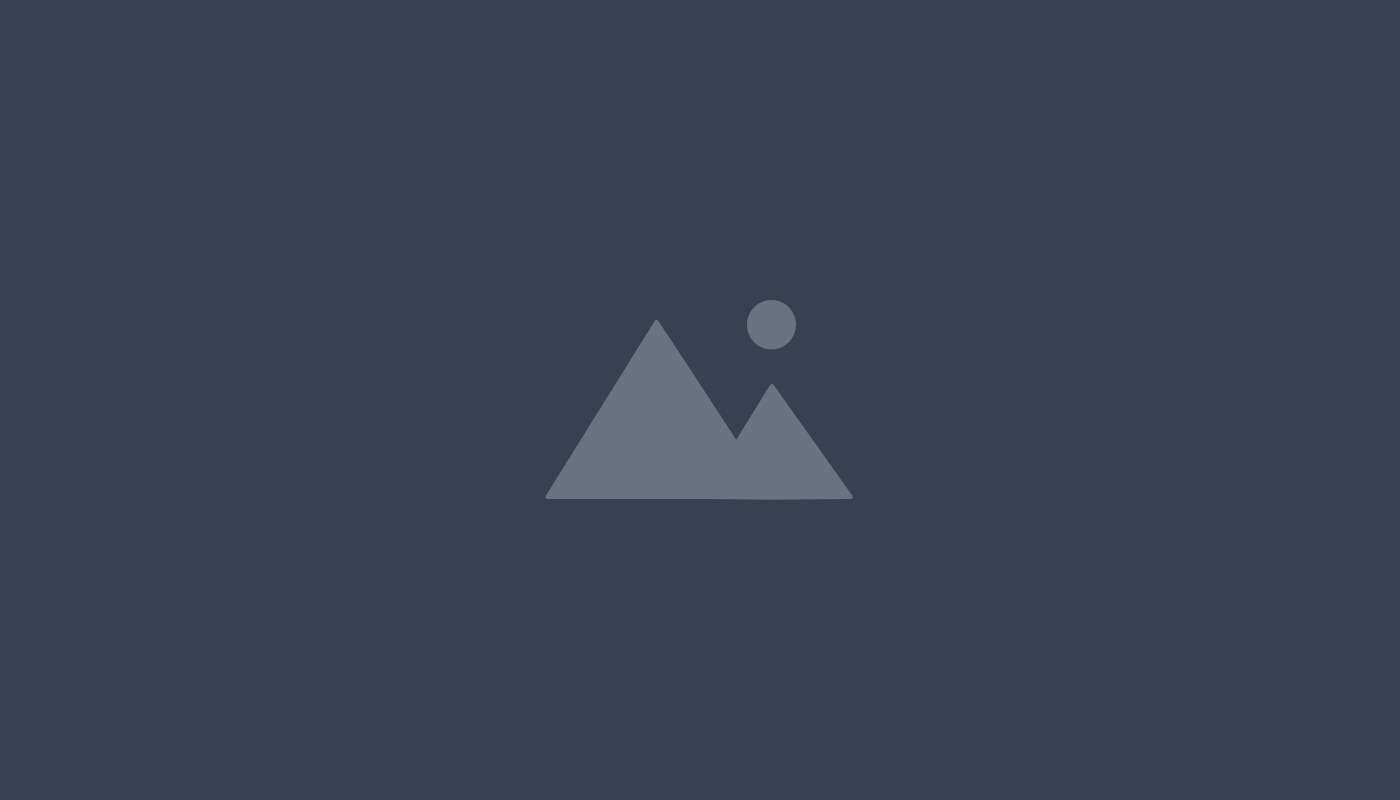
Year 1 - Safety Training PPE-(LOTO, Ladder Safety, Fall Protection, etc.)
0
40
a. Demonstrate basic knowledge of types. b. Demonstrate basic knowledge of safe handling of refrigerants. c. Demonstrate basic knowledge of safe handling of pressurized gasses. d. Demonstrate basic knowledge of safe handling of combustibles. e. Demonstrate basic knowledge of SDS (Safety Data Sheet) information to material. f. Work in a safe and workman-like manner abiding applicable local, state, and federal regulations; EPA (environmental), DOT(environmental), DOT (motor vehicles) and OSHA (worker safety). g. Demonstrate basic knowledge of first aid procedures for occupational hazards. h. Demonstrate basic knowledge of lockout & tag out procedures. i. Demonstrate basic knowledge of safe ladder usage. j. Demonstrate basic knowledge and use of personal fall protection equipment.
Year 1 -Demonstrate basic knowledge and proficiency in performing package /Split A/C Preventative Maintenance.
0
300
Year 1 -Demonstrate basic knowledge and proficiency in performing condenser and evaporator Coil Cleaning.
0
40
Year 1 -Demonstrate basic knowledge and proficiency in the proper installation and replacement of condensate drain lines and p-traps.
0
40
Year 1 -Demonstrate basic knowledge necessary to diagnose/repair/replace crankcase heaters.
0
20
Year 1 -Demonstrate basic knowledge necessary to diagnose/repair/replace a motor pulley/sheave.
0
20
Year 1 -Demonstrate basic knowledge necessary to diagnose/repair/replace an electric heat bank.
0
40
Year 1 -Demonstrate basic knowledge necessary to diagnose/repair/replace a low voltage thermostat.
0
60
Year 1 -Demonstrate basic knowledge necessary to diagnose/repair/replace a packaged gas heat pack.
0
60
Year 1 -Demonstrate basic knowledge necessary to diagnose/repair/replace a control relay.
0
20
Year 1 -Demonstrate basic knowledge necessary to diagnose/repair/replace a contactor.
0
20
Year 1 -Demonstrate basic knowledge necessary to diagnose/repair/replace a capacitor.
0
20
Year 1 -Demonstrate basic knowledge necessary to diagnose/repair/replace a draft inducer motor/assembly.
0
20
Year 1 -Demonstrate basic knowledge necessary to diagnose/replace open electrical fuses.
0
20
Year 1 -Demonstrate basic knowledge necessary to diagnose/repair/replace a low voltage transformer.
0
20
Year 1 -Demonstrate basic knowledge and acquire Universal EPA 608 Certification.
0
80
Year 1 -Demonstrate basic knowledge necessary to diagnose/repair/replace a time delay relay, Freezestat control, and head pressure/fan cycle control.
0
60
Year 1 -Demonstrate basic knowledge necessary to diagnose/repair/replace an evaporator fan motor.
0
40
Year 1 -Demonstrate basic knowledge necessary to diagnose/repair/replace a condenser fan motor.
0
60
Year 1 -Demonstrate basic knowledge necessary to diagnose/repair/replace a high/low pressure switch.
0
20
Year 1 -Demonstrate basic knowledge necessary to diagnose/perform proper refrigerant charging procedures.
0
60
Year 1 -Demonstrate basic knowledge necessary to diagnose/repair/replace a hermetic compressor.
0
60
Year 1 -Demonstrate basic knowledge necessary to diagnose the need for and perform a refrigerant leak check and repair.
0
100
Year 1 -Demonstrate basic knowledge necessary to diagnose/repair/replace a faulty metering device.
0
40
Year 1 -Demonstrate basic knowledge necessary to diagnose proper superheat and sub-cooling.
0
60
Year 1 -Demonstrate basic knowledge necessary to install/repair/replace basic sheet metal and duct board systems.
0
40
Year 1 -Demonstrate basic knowledge necessary to diagnose/repair/replace an electrical disconnect.
0
20
Year 1 -Demonstrate basic knowledge necessary to diagnose/repair/replace a duct smoke detector.
0
20
Year 1 -Demonstrate basic knowledge necessary to measure/diagram/install a curb adapter.
0
20
Year 1 -Demonstrate basic knowledge necessary to diagnose/repair/replace a blower wheel, shaft, and bearings/assembly.
0
40
Year 1 -Demonstrate basic knowledge necessary to install/replace a split system condensing unit.
0
60
Year 1 -Demonstrate basic knowledge necessary to diagnose/repair/replace a condensate drain pan.
0
20
Year 1 -Demonstrate basic knowledge necessary to install/replace a split system air handler.
0
40
Year 1 -Demonstrate basic knowledge necessary to install/replace a packaged rooftop unit.
0
80
Year 1 -Demonstrate basic knowledge necessary to diagnose/repair/replace an EMS sensor (RH, temperature, voltage, or current types).
0
20
Year 1 -Demonstrate basic knowledge necessary to diagnose/perform a repair or replace analysis for a major failure of packaged equipment.
0
40
Year 1 -Demonstrate basic knowledge necessary to diagnose/repair/replace a packaged unit control board.
0
20
Year 1 -Demonstrate basic knowledge necessary to diagnose/repair/replace a packaged economizer system/components.
0
40
Year 1 -Demonstrate basic knowledge necessary to diagnose/repair a basic reach-in type refrigeration unit.
0
80
Year 1 -Demonstrate basic knowledge necessary to diagnose/repair/replace a basic ice machine.
0
100
Year 1 -Demonstrate basic knowledge necessary to install/replace a complete basic split system.
0
60
Year 1 -Demonstrate knowledge necessary to diagnose/repair/replace a compressor burnout.
0
20
Year 2 - Safety Training PPE-(LOTO, Ladder Safety, Fall Protection, etc.)
0
40
a. Demonstrate basic knowledge of types. b. Demonstrate basic knowledge of safe handling of refrigerants. c. Demonstrate basic knowledge of safe handling of pressurized gasses. d. Demonstrate basic knowledge of safe handling of combustibles. e. Demonstrate basic knowledge of SDS (Safety Data Sheet) information to material. use f. Work in a safe and workman-like manner abiding applicable local, state, and federal regulations; EPA (environmental), DOT (motor vehicles) and OSHA (worker safety). g. Demonstrate basic knowledge of first aid procedures for occupational hazards. h. Demonstrate basic knowledge of lockout & tag out procedures. i. Demonstrate basic knowledge of safe ladder usage. j. Demonstrate basic knowledge and use of personal fall protection equipment.
Year 2 - Trade Mathematics
0
60
a. Demonstrate basic knowledge and calculate the volume and area of basic geometric shapes. b. Calculate static head in basic piping systems. c. Demonstrate use of fan laws and calculate fan speed (RPM) required to produce a specified change in volume (CFM). d. Demonstrate knowledge of Ohm’s Laws and solve for various calculations.
Year 2 - Electrical Power
0
400
a. Demonstrate basic knowledge of types of circuits-series, parallel, and series-parallel. b. Develop proficiency and demonstrate knowledge of use of electrical instruments and multi-meters to locate faults and troubleshoot low voltage control circuits. c. Develop proficiency and demonstrate knowledge of use of electrical instruments and multi-meters to locate faults and troubleshoot high/line voltage power circuits. d. Demonstrate knowledge and develop proficiency in reading wiring schematics, pictorial diagrams, and ladder diagrams. e. Demonstrate knowledge and develop proficiency in diagnosing and repairing motor starter circuits and various types of electrical motors. f. Demonstrate knowledge and develop proficiency in troubleshooting overcurrent protection and circuit breakers. g. Demonstrate knowledge and identification of wiring symbols.
Year 2 - Heating Systems
0
340
a. Demonstrate knowledge of and troubleshooting of gas heating pilot systems and flame verification. b. Identify gas heating components and demonstrate ability to troubleshoot common failures. c. Demonstrate proficiency in gas vent sizing, proper draft verification, and solving combustion related issues. d. Demonstrate the use of temperature rise to determine system airflow. e. Identify heating hot water boiler components, safeties, and knowledge of basic system operation.
Year 2 - Cooling Systems
0
800
a. Describe temperature pressure relationships. b. Demonstrate the ability to evaluate cooling systems and determine specific deficiencies and corrective actions required. c. Identify and evaluate various types of compressors and their performance. d. Demonstrate knowledge of cooling system primary controls, safeties, refrigerant control valves, and regulators.
Year 2 - Air Distribution Systems
0
160
a. Demonstrate knowledge of the relationship between pressure, velocity, and volume in distribution systems. b. Utilize a duct calculator and solve for airflow related variables and duct sizing/flow calculations. c. Identify and demonstrate proficiency in the use of air measurement instruments. d. Identify air system design strategies for both warm and cold climates. e. Identify and demonstrate knowledge of duct system components, fittings, support systems, and installation skills. f. Demonstrate knowledge and understanding of energy efficient insulation methods and sealing techniques for duct systems.
Year 2 - Copper, Plastic, and Steel Piping
0
200
a. Demonstrate knowledge and proficiency in the installation, support, soldered/brazed joints, and mechanical/flared connections of various types of copper pipe/tubing. b. Demonstrate knowledge and proficiency in the installation, support, solvent welded and mechanical connections of various types of plastic pipe and tubing. c. Demonstrate knowledge of steel piping techniques, fitting geometry including allowances, methods of joining and d. threading, installation of hangers and other support means for steel pipe. e. Demonstrate knowledge and proficiency in the installation of various types of pipe insulation materials.
Year 3 - Safety Training PPE-(LOTO, Ladder Safety, Fall Protection, etc.)
0
40
a. Demonstrate basic knowledge of types. b. Demonstrate basic knowledge of safe handling of refrigerants. c. Demonstrate basic knowledge of safe handling of pressurized gasses. d. Demonstrate basic knowledge of safe handling of combustibles. e. Demonstrate basic knowledge of SDS (Safety Data Sheet) information to material use. f. Work in a safe and workman-like manner abiding applicable local, state, and federal regulations; EPA(environmental), DOT (motor vehicles) and OSHA (worker safety). g. Demonstrate basic knowledge of first aid procedures for occupational hazards. h. Demonstrate basic knowledge of lockout & tag out procedures. i. Demonstrate basic knowledge of safe ladder usage. j. Demonstrate basic knowledge and use of personal fall protection equipment.
Year 3 - Electrical Motors and Compressors
0
300
a. Demonstrate knowledge of various types of single and three phase motors and wiring methods including multispeed, start relays and start/run capacitors. b. Identify and explain the operation of various types of hermetic and semi-hermetic compressors- reciprocating, rotary, scroll, screw, and centrifical. c. Identify and describe various methods of compressor capacity control. d. Identify and describe compressor failures do to electrical, mechanical, hydraulic, and lubrication issues. e. Identify and explain the operation of compressor protection devices. f. Demonstrate the use of pressure-temperature charts to calculate system superheat and sub cooling. g. Demonstrate the knowledge of refrigerants and compatible oil used in various temperature range applications. h. Describe types and sources of oil contamination. i. Demonstrate knowledge of common refrigerant conversion processes including system cleanup and lubricant changes.
Year 3 - Leak Detection, Evacuation, Recovery and Charging Processes
0
320
a. Demonstrate knowledge of the equipment and procedures used to leak check refrigerant circuits. b. Demonstrate knowledge refrigerant recovery, containment, and system evacuation procedures. c. Demonstrate proper charging techniques using various types of zeotropic and zeotropic refrigerants.
Year 3 - Metering Devices
0
120
a. Identify and demonstrate knowledge of the operation and application of various types of metering devices. b. Describe service issues with common metering devices and demonstrate knowledge of troubleshooting and repair/replacement of the devices.
Year 3 - Heat Pumps
0
100
a. Explain the operation of various types of heat pump systems. b. Demonstrate knowledge of components, controls, and supplemental heat systems. c. Demonstrate knowledge of troubleshooting common service issues and repairs as well as installation methods.
Year 3 - Equipment Maintenance
0
500
a. Identify and describe common seals, bearings, gaskets and packing materials. b. Demonstrate knowledge and use of common lubricants. c. Identify belt drive components and explain how to replace, align, and adjust tension these components. d. Describe and demonstrate the knowledge of inspection and maintenance procedures for common packaged and built-up HVACR systems.
Year 3 - Chimneys, Vents, and Flues
0
100
a. Describe the principles of combustion. b. Identify vented appliance category types and related vent construction. c. Demonstrate the knowledge of natural, power, and induced draft equipment types and the ability to diagnose and correct operational issues. d. Describe installation considerations and vent types for condensing and non-condensing equipment.
Year 3 - Sheet Metal Duct Systems
0
120
a. Identify and describe common types of sheet metal ducts, joining, support and reinforcement methods. b. Describe methods used to internally and externally insulate and attenuate metal duct. c. Identify sheet metal dampers, access doors and other accessories and their installation. d. Demonstrate the knowledge of and proper installation of flexible duct connectors and systems.
Year 3 - Fiberglass and Fabric Duct Systems
0
120
a. Describe the standards and application considerations for fiberglass duct systems. b. Demonstrate the knowledge and proficiency in the layout, fabrication, joining, hanging, supporting and sealing of duct components.
Year 3 - Commercial Airside Equipment
0
200
a. Describe commercial airside, ventilation, and exhaust systems. b. Demonstrate the knowledge of constant volume, variable volume and variable volume/temperature (VVT) systems and their applications. c. Describe the operation of various air terminal and delivery equipment. d. Identify the key components, explain the operation, and common service issues pertaining to packaged and split air handling equipment, economizers, air filtration and other common accessories.
Year 3 - Basic Hydronic Equipment
0
80
a. Identify and describe the primary types of hot water heating systems and their components. b. Demonstrate knowledge of hydronic piping configurations and systems. c. Describe the methods and equipment used to select pumps and control water flow in hydronic systems.
Year 4 - Safety Training PPE - (LOTO, Ladder Safety, Fall Protection, etc.)
0
40
a. Demonstrate basic knowledge of types. b. Demonstrate basic knowledge of safe handling of refrigerants. c. Demonstrate basic knowledge of safe handling of pressurized gasses. d. Demonstrate basic knowledge of safe handling of combustibles. e. Demonstrate basic knowledge of SDS (Safety Data Sheet) information to material. f. Work in a safe and workman-like manner abiding applicable local, state, and federal regulations; EPA (environmental), DOT (motor vehicles) and OSHA (worker safety). g. Demonstrate basic knowledge of first aid procedures for occupational hazards. h. Demonstrate basic knowledge of lockout & tag out procedures. i. Demonstrate basic knowledge of safe ladder usage. j. Demonstrate basic knowledge and use of personal fall protection equipment.
Year 4 - Motor and Control Circuit Troubleshooting
0
240
a. Identify and describe how to service electronically commutated motors. b. Describe the selection and setup process for variable frequency drives as well as resolution of common issues. c. Explain how to troubleshoot common control circuits and load components. d. Describe the sequence of operation of common heating and cooling systems. e. Describe the operation, installation, and troubleshooting of temperature controls and various types of thermostats. f. Demonstrate proficiency in the use of ladder and other wiring diagrams necessary to troubleshoot control system failures.
Year 4 - Cooling Systems Troubleshooting
0
580
a. Demonstrate knowledge of the refrigerant cycle and explain in detail how to recognize and remedy specific system faults and failures common to packaged, split and built-up systems. b. Explain how seemingly minor performance issues can result in substantial system failures.
Year 4 - Heat Pump Systems Troubleshooting
0
180
a. Describe the sequence of operation of common heat pump systems in the heating, cooling, and defrost modes. b. Explain the operation of supplemental heat and dual fuel systems in relationship to heat pump systems. c. Demonstrate knowledge and proficiency in the diagnostics and troubleshooting of heat pump systems, controls, and components.
Year 4 - Gas Heating Systems Troubleshooting
0
160
a. Describe the sequence of operation of common gas heating systems and common system/component failures. b. Demonstrate knowledge and proficiency in the diagnostics and troubleshooting of gas heating systems, controls, flame and pilot verification systems, and components.
Year 4 - Oil Heating Systems Troubleshooting
0
40
a. Describe the sequence of operation of common oil heating systems and common system/component failures. b. Demonstrate knowledge and proficiency in the diagnostics and troubleshooting of oil heating systems, controls, ignition and flame verification systems, and components.
Year 4 - Air Handler and Furnace Accessories Troubleshooting
0
240
a. Describe the sequence of operation of common airside accessories- humidifiers, electronic air cleaners, economizers, UV lighting systems, and heat recovery ventilators/systems. b. Demonstrate knowledge of identifying faults, troubleshooting and repair of common accessories.
Year 4 - Zoning, Ductless and Variable Refrigerant Flow (VRF) Systems
0
180
a. Describe the sequence of operation of common zoning, damper & VAV/VVT systems and common system/component failures. b. Demonstrate knowledge and proficiency in the diagnostics and troubleshooting of zoning, damper, and VAV/VVT systems. c. Demonstrate knowledge of service and installation of ductless and VRF systems.
Year 4 - Commercial Hot and Chilled Water Systems
0
120
a. Describe the sequence of operation of common heating hot water and chilled water systems and common failures. b. Demonstrate knowledge and proficiency in the diagnostics and troubleshooting of heating and cooling plant components, controls, and related systems including boilers, air and water-cooled chillers, pumps, valves, cooling towers and evaporative condensers.
Year 4 - Retail Refrigeration Systems
0
180
a. Describe the sequence of operation of retail refrigeration applications of various temperatures including defrost methods. b. Demonstrate knowledge and proficiency in the diagnostics and troubleshooting of reach-in, merchandising, and walk-in systems as well as their components.
Year 4 - Customer Relations
0
40
a. Explain the technician’s role in positive customer relations. b. Explain the basic process and conduct when responding to a service call.
Year 5 -Safety Training PPE-(LOTO, Ladder Safety, Fall Protection, etc.)
0
40
a. Demonstrate basic knowledge of types. b. Demonstrate basic knowledge of safe handling of refrigerants. c. Demonstrate basic knowledge of safe handling of pressurized gasses. d. Demonstrate basic knowledge of safe handling of combustibles. e. Demonstrate basic knowledge of SDS (Safety Data Sheet) information to material. f. Work in a safe and workman-like manner abiding applicable local, state, and federal regulations; EPA (environmental), DOT (motor vehicles) and OSHA (worker safety). g. Demonstrate basic knowledge of first aid procedures for occupational hazards. h. Demonstrate basic knowledge of lockout & tag out procedures. i. Demonstrate basic knowledge of safe ladder usage. j. Demonstrate basic knowledge and use of personal fall protection equipment.
Year 5 - Water Treatment
0
80
a. Describe common issues related to water quality and inherent properties. b. Explain how to test and identify specific water/fluid related issues. c. Identify types of water filtration and treatment equipment and strategies. d. Identify and describe how to treat specific issues in hydronic based systems for open and closed loop systems as well as steam heating/process systems.
Year 5 - Indoor Air Quality (IAQ)
0
120
a. Demonstrate knowledge of IAQ issues and effects on occupants. b. Explain how acceptable IAQ can be achieved. c. Identify IAQ based HVAC equipment and their use to maintain acceptable IAQ.
Year 5 - Energy Conservation Systems
0
80
a. Identify and demonstrate knowledge of operation of energy recycling and reclamation equipment including heat recovery ventilators, air-to-air heat exchangers, condenser heat recovery systems, heat pipe exchangers, twin-tower enthalpy recovery loops, and flue gas heat recovery systems. b. Identify and explain the operation of utility demand reduction systems and thermal storage systems.
Year 5 - Building Management Systems (BMS)
0
320
a. Demonstrate the knowledge of the architecture of BMS networks, their components, interworking’s of input/output devices and other related systems and hardware. b. Explain common BMS control strategies. c. Demonstrate knowledge and use of user interfaces and software platforms.
Year 5 - Air Balancing
0
220
a. Demonstrate knowledge of the properties of air and psychometrics as related to human comfort and maintaining conditioned spaces. b. Demonstrate knowledge of the air balancing process and proficiency in the use of tools and instruments to test and balance HVAC systems.
Year 5 - System Startup and Shutdown
0
120
a. Describe the process for the shutdown, inspection, and startup of hot water and steam systems including wet and dry processes. b. Describe the process for the shutdown, inspection, and startup of chilled water, cooling tower and related equipment.
Year 5 - Construction Drawings
0
80
a. Demonstrate the knowledge of reading plans and specifications including symbols, schedules, details and proficiency in locating specific information. b. Show proficiency in the use of the takeoff method to formulate estimates.
Year 5 - Heating and Cooling System Design
0
120
a. Demonstrate knowledge of the use of plans and site data to perform load estimates. b. Explain how to select equipment based on load calculations. c. Demonstrate knowledge in the design and implementation of air duct/distribution systems.
Year 5 - Commercial and Industrial Refrigeration Systems
0
580
a. Describe the methods used to freeze and store food products. b. Describe the sequence of operation of various commercial and industrial refrigeration systems. c. Identify and describe the function of various system components and controls. d. Identify the common defrost systems, components, and sequences of operation.
Year 5 - Specialized Heating and Systems
0
240
a. Demonstrate knowledge of the operation of and proficiency in the repair of critical cooling systems (CRAC). b. Demonstrate knowledge of the operation of and proficiency in the repair of makeup air systems including direct fired. c. Demonstrate knowledge of the operation of various specialized heating and cooling systems.
Related Instruction Content
Training Provider(s):
Chapter 1: Careers and Certification
1
a. Understand career clusters and career pathways. b. Evaluate HVACR career options. c. Determine which exams and corresponding certifications are most suited for achieving your career goals. d. Understand the tools needed for success in the workplace. e. Understand the value of an accredited HVACR program. f. Explain the value of continuing education and training. Understand EPA regulations as they relate to air conditioning and refrigeration. g. Become involved in HVACR service organizations and trade associations.
Chapter 2: Safety
3
a. Describe OSHA and its purpose. b. Properly assess electrical, fire, temperature, pressure, refrigerant, chemical, and breathing hazards. c. Explain the components of a safety data sheet (SDS). d. Discuss the need for personal protective equipment (PPE) for head, hearing, eye, and respiratory protection. e. Exercise safe practices when lifting, using a ladder or scaffold, for fall protection, in confined spaces, and for hand and power tools.
Chapter 3: Service Calls
1
a. Describe three general categories of HVACR service. b. Explain the steps in a standard troubleshooting procedure. c. Evaluate a problem in a logical and systematic sequence. d. Select a remedy for a problem using a three-step procedure. e. Explain how a technician’s appearance and conduct affects customer relations. f. Understand the basics for writing service estimates and service contracts.
Chapter 4: Energy and Matter
3
a. Differentiate between matter and energy. b. Summarize the relationship between force, work, and power. c. Differentiate between the Fahrenheit, Celsius, Rankine, and Kelvin temperature scales. d. Use the appropriate formulas to calculate enthalpy, specific enthalpy, and changes in heat for a given substance. e. Compare the radiation, convection, and conduction methods of heat transfer. f. Illustrate the differences between the three states of matter. g. Differentiate between sensible heat and latent heat. h. Predict the effect of a drop-in temperature or an increase in pressure on a saturated vapor. i. Summarize the relationships between mass, weight, and density.
Chapter 5: Gases
3
a. Describe the effect on gas pressure and temperature when its volume is increased or decreased. b. Describe Pascal’s law and provide examples of it in the HVACR industry. c. Illustrate the effect of pressure and heat on the three states of matter. d. Differentiate between gauge pressure and absolute pressure. e. Understand how the concepts of Boyle’s law, Charles’ law, Gay-Lussac’s law, and the combined gas law explain the behavior of refrigerant in the operation of a mechanical refrigeration system. f. Describe Dalton’s law and explain how it can be applied to HVACR work. g. Explain the significance of saturated vapors in a refrigeration system. h. Describe how the processes of air exchange, pressure change, and state change provide a cooling effect.
Chapter 6: Basic Refrigeration Systems
3
a. Explain how phase changes are used in refrigeration systems to transfer heat. b. Describe how phase change is possible through pressure change or the addition or removal of heat. c. Summarize the four phases of the compression refrigeration cycle. d. Identify the components that divide the low and high sides of a compression refrigeration system. e. Understand the purpose of each of the components in a compression refrigeration system.
Chapter 7: Tools and Supplies
3
a. Explain how to use various hand tools. b. Select the appropriate hand tool for a specific task. c. Select the appropriate power tool for a specific task. d. Monitor temperature with various thermometers. e. Identify different types of fastening methods and devices. f. Compare cleaning methods and the use of various solvents. g. Identify basic supplies needed on a typical installation or service call. h. Follow approved safety procedures.
Chapter 8: Working with Tubing and Piping
2
a. Distinguish among the various types of tubing and piping used in refrigeration work. b. Explain the uses of the various types of tubing and piping in refrigeration work. c. Perform tube cutting and bending procedures using proper methods. d. Complete various tubing and piping connecting procedures using approved methods. e. Use safe and accepted soldering and brazing techniques. f. Follow approved safety procedures.
Chapter 9: Introduction to Refrigerants
3
a. Recognize the effect of halogenated refrigerants on the ozone layer. b. Summarize Environmental Protection Agency regulations governing refrigerants. c. Differentiate between CFC, HCFC, HFC, and blended refrigerants. d. Identify refrigerants according to their series number and cylinder color code. e. Interpret pressure-temperature curves, pressure-enthalpy tables, and pressure-enthalpy diagrams. f. Summarize the properties and common applications of different refrigerants. g. Identify which types of refrigerants are compatible with which lubricants.
Chapter 10: Equipment and Instruments for Refrigerant Handling and Service
2
a. Distinguish between the different types of refrigerant cylinders and identify the proper use of each type. b. Identify the different kinds of pressure gauges and how they are used. c. Recognize the various types of service valves used on refrigeration systems. d. Understand the purpose, construction, and operation of a gauge manifold. e. List the types of leak detection methods and their advantages and disadvantages. f. Explain the purpose for using a vacuum pump. g. Describe the types of equipment used for refrigerant recovery and recycling.
Chapter 11: Working with Refrigerants
3
a. Check refrigerant charge by determining a system’s superheat or sub-cooling. b. Implement both passive and active refrigerant recovery procedures. c. Charge a system with an inert gas to pressure test for leaks. d. Carry out refrigeration system leak repairs using either epoxy resin or brazing. e. Evacuate a refrigeration system using both deep vacuum and triple evacuation methods. f. Charge a specific amount of refrigerant into a system as either a liquid or vapor. g. Follow approved safety procedures when recovering and charging refrigerant.
Chapter 12: Basic Electricity
2
a. Identify the parts of an atom. b. Use Ohm’s law to explain the mathematical relationship among voltage, current, and resistance. c. Contrast the properties and applications of static electricity, direct current, and alternating current. d. Summarize the three types of materials used in electrical and electronic parts and systems. e. Design diagrams of series, parallel, and series-parallel circuits. f. Use formulas to calculate the voltage drop across an electrical load. g. List the components of an electromagnet and factors that affect the strength of its magnetic field.
Chapter 13: Electrical Power
2
a. Use mathematical formulas to calculate root mean square values, apparent power, and power factor. b. Summarize how resistance, inductive reactance, and capacitive reactance cause power loss and affect power factor in electrical circuits. c. Understand the difference between single-phase and three-phase power. d. Define a Class 2 circuit and identify the types of electrical connections an HVACR technician is permitted to make. e. Recall wire size terminology and connect wires using wire terminals and crimping. f. Explain the importance of properly grounding and bonding an electrical system. g. Describe the purpose and operation of various overcurrent protection devices used in circuits. h. Identify the different types and causes of common electrical problems.
Chapter 14: Basic Electronics
2
a. Discuss how electrons and holes move through a semiconductor based on the principle of hole flow. b. Explain how forward biased and reverse biased diodes affect the flow of current in a circuit. c. Define a control circuit and distinguish between electronic and electrical devices used in a control circuit. d. Summarize the operation of various electronic semiconductor devices and how they are used in HVACR systems. e. Understand the purpose of microprocessors and computers in HVACR.
Chapter 15: Electric Motors
3
a. Identify the basic parts of a motor. b. Explain how a motor operates based on the codependent relationship of magnetism and electricity. c. Calculate a motor’s synchronous speed and explain how it is different than the motor’s full-load speed. d. Compare how motor windings and capacitors are used to start single-phase motors. e. Summarize the different starting and running characteristics of various single-phase motors. f. Understand the structure and basic operation of a three-phase motor. g. Identify the differences between electronically commutated motors and ac motors. h. Select the proper motor for an application by analyzing standard motor data found on motor nameplates. i. Identify the different applications of motors in HVACR systems.
Chapter 16: Electrical Control Systems
3
a. Understand the difference between pictorial and ladder circuit diagrams. b. Describe how range and differential adjustments are used to calibrate temperature and pressure controls. c. Identify the various types of temperature-sensing devices used in motor controls. d. Compare the operation of various electromagnetic and electronic motor starting relays.
Chapter 17: Servicing Electric Motors and Controls
3
a. Use different testing instruments to measure electrical variables in a circuit b. Test motor winding insulation using a megohmmeter and perform maintenance based on the measured resistance. c. Determine the cause of motor trouble by checking a motor’s current draw, start and run capacitors, and internal temperature. d. Measure a three-phase motor’s voltage and winding resistance to test it for single phasing. e. Use an ohmmeter to take measurements on a hermetic compressor motor and determine whether it has a shorted winding, an open winding, or a short to ground. f. Start a stuck hermetic compressor motor by connecting a hard start kit to the compressor terminals. g. Service fan motors by identifying connection problems, fan problems, and electronically commutated motor trouble codes. h. Properly lubricate motor bearings and install belts connecting external motors to belt-driven units. i. Troubleshoot and replace faulty control system components, such as thermostats and motor starting relays.
Chapter 18: Compressors
2
a. Summarize the design differences between open-drive compressors, fully hermetic compressors, and semi-hermetic compressors. b. Identify the components of a reciprocating piston compressor and summarize their functions. c. Understand how a Scotch yoke type of reciprocating compressor works. d. Explain how a rotary compressor works. e. Summarize the differences between rotating vane and stationary blade rotary compressors. f. Understand how a scroll compressor works. g. Explain how a screw compressor works. h. Identify the components of a centrifugal compressor and summarize their functions. i. Identify and explain the purpose of compressor cooling and lubrication systems, mufflers, and crankcase heaters.
Chapter 19: Compressor Safety Components
2
a. Explain ideal compressor operating conditions and requirements. b. Describe the use and operation of compressor protection devices, such as overcurrent protection devices, overload devices, crankcase pressure regulators, discharge line pressure switches, and discharge line thermostats. c. Explain the role an accumulator plays in a system and how it accomplishes its purpose. d. Understand the components that maintain proper oil and refrigerant flow to the compressor. e. Explain the operation of oil separators, oil reservoirs, oil level regulators, and oil safety control. f. Summarize the purpose of vibration absorbers and the techniques for installing them. g. Explain the purpose and operation of crankcase heaters.
Chapter 20: Metering Devices
4
a. Summarize the purpose of metering devices. b. Categorize metering devices as modulating or fixed. c. Summarize the design and function of capillary tube and fixed-orifice metering devices. d. Explain the design and function of common types of thermostatic expansion valves (TXVs). e. Summarize the design and function of automatic expansion valves (AXVs). f. Explain the design and function of common types of electronic expansion valves (EEVs). g. Understand the differences between high-side float (HSF) refrigerant controls and low-side float (LSF) refrigerant controls.
Chapter 21: Heat Exchangers
3
a. Compare and contrast air-cooling and liquid-cooling evaporators. b. Explain the construction of fin-and-tube, plate, and microchannel evaporators. c. Compare and contrast domestic, air-conditioning, and commercial refrigeration evaporators. d. Summarize the operation of evaporator defrost controls and defrosting methods. e. Describe the different types of water-cooled condensers. f. Explain the modes of operation of evaporative condensers. g. Compare and contrast domestic, air-conditioning, and commercial refrigeration condensers.
Chapter 22: Refrigerant Flow Components
3
a. Explain the two primary functions of refrigerant loop components. b. Describe the purpose and uses of liquid receivers. c. Differentiate between the distinct duties of filters and driers. d. Explain the function of suction line and liquid line filter-driers. e. Explain how sight glasses can be used to indicate the amount of moisture in a refrigeration system. f. Describe the operation and use of refrigerant line valves, shutoff valves, service valves, check valves, solenoid valves, hot-gas defrost valves, hot-gas bypass valves, and liquid injection valves. g. Explain the operation and purpose of crankcase pressure regulators (CPRs). h. Compare the operation of the different types of evaporator pressure regulators (EPRs). i. Compare and contrast the different types of relief valves available. j. Describe the different head pressure control valves and condenser arrangements and explain how they operate to maintain head pressure.
Chapter 23: Overview of Domestic Refrigerators and Freezers
3
a. Summarize the differences between domestic refrigeration systems and commercial refrigeration systems. b. Recall the causes of food spoilage and explain how domestic refrigeration systems minimize spoilage. c. Summarize the operation of an automatic defrost system in a frost-free freezer. d. Illustrate airflow patterns in top, bottom, and side-by-side refrigerator-freezer units. e. Explain how refrigerator and freezer cabinets are constructed. f. Identify the features of gaskets used in refrigerator and freezer doors. g. Identify available and innovative refrigeration and freezer units.
Chapter 24: Systems and Components of Domestic Refrigerators and Freezers
3
a. Explain the function of the basic components in a domestic compression refrigerator-freezer. b. Understand how common cooling controls maintain the desired conditions inside a domestic refrigerator-freezer. c. Describe how dampers are used to control temperatures in frozen food and fresh food compartments of a domestic refrigerator-freezer. d. Understand the operation of common defrost systems used in domestic refrigerator-freezers. e. Explain the purpose of condensation controls in domestic refrigerator-freezers and describe their operation. f. Describe the methods used to control conditions inside crispers and humidity-controlled drawers.
Chapter 25: Installation and Troubleshooting of Domestic Refrigerators and Freezers
2
a. Check domestic compression refrigerators for proper installation. b. Use the proper procedure for starting a domestic refrigerator-freezer. c. Interpret common symptoms of system malfunction. d. Use proper procedures to test a domestic refrigerator-freezer’s auxiliary circuits. e. Explain the use of piercing valves, pinching tools, and valve adapters. f. Interpret temperature and pressure conditions inside a refrigeration system to determine points of failure. g. Summarize common symptoms of internal component failure and their possible causes.
Chapter 26: Service and Repair of Domestic Refrigerators and Freezers
3
a. Apply the proper techniques to clean a condenser and compressor in a domestic refrigerator. b. Explain the steps required to prepare a domestic refrigerator or freezer for internal service. c. Summarize the steps required to return a domestic refrigerator or freezer to service after a motor burnout. d. Apply the proper procedure to remove and replace a compressor in a domestic refrigerator or freezer. e. Use the proper procedures to repair leaks in condensers and evaporators. f. Apply the proper procedures to clean or replace a capillary tube. g. Summarize the procedure for selecting, removing, and installing filter-driers. h. Compare the different methods of charging a small hermetic refrigeration system. i. Summarize different methods of calibrating, testing, and adjusting thermostatic controls in refrigerator-freezers. j. Explain considerations to take when removing system components from a cabinet. k. Summarize the steps required to properly discard or store a domestic refrigerator or freezer.
Chapter 27: Air Movement and Measurement
3
a. Understand the concepts of climate and weather. b. Summarize the purpose of air-conditioning systems. c. Identify the layers of the atmosphere and the primary components of air. d. Understand the relationships between humidity, relative humidity, and dew point. e. Use a hygrometer to measure moisture in the air. f. Differentiate between wet-bulb and dry-bulb temperatures. g. Explain the principles of psychometry and the use of psychrometric charts. h. Summarize the range of air conditions that fall within the human comfort range. i. Understand how air movement affects human comfort. j. Use anemometers, pitot tubes, and manometers to measure air velocity. k. Identify external factors that affect indoor air conditions.
Chapter 28: Air Quality
3
a. Identify the agencies and standards that regulate indoor air quality. b. Categorize indoor air pollutants as solid or gas pollutants and provide examples of each. c. Recall the factors that affect indoor air quality. d. Recognize the main sources of pollutants that adversely affect residential and commercial indoor air quality. e. Summarize the processes used to assess residential and commercial indoor air quality. f. Summarize the steps that can be taken to prevent indoor air quality problems. g. Differentiate between sick building syndrome, building-related illness, and multiple-chemical sensitivity. h. Compare the different types of air filters available. i. Summarize the different air cleaning methods used to improve indoor air quality. j. Explain the operation and maintenance of ultraviolet air treatment system. k. Differentiate between heat recovery ventilators (HRVs) and energy recovery ventilators (ERVs).
Chapter 29: Air Distribution
4
a. Recall the properties of air that affect air distribution system design or installation. b. Categorize air circulation systems. c. Determine the basic ventilation requirements for a given space. d. Identify the basic types of air duct systems. e. Explain the relationships between air distribution and duct sizing and design. f. Understand the procedure for correctly sizing ducts.
Chapter 30: Ventilation System Service
2
a. Recall the various methods for checking airflow and air leakage. b. Explain how to identify, isolate, and correct duct noise problems. c. Use proper equipment and techniques to clean a duct system. d. Apply knowledge of airflow to balance a duct system. e. Recall methods of removing odors from the air. f. Summarize periodic maintenance tasks that must be performed on fans. g. Explain procedures for inspecting and servicing various types of air filters.
Chapter 31: Ductless Air-Conditioning Systems
2
a. Explain the purpose of comfort cooling systems b. Describe the cooling and dehumidifying process of an air-conditioning system and show the relationship of dry-bulb temperature, moisture content, and relative humidity on a psychrometric chart. c. Summarize the characteristics of window and wall-mounted room air conditioners. d. Install and service window and wall-mounted room air conditioners. e. Discuss the operation and application of packaged terminal air conditioners and console air conditioners f. Identify the characteristics and uses of portable air conditioners. g. Explain the operation, components, and arrangement of ductless split systems. h. Install and service ductless split systems.
Chapter 32: Residential Central Air-Conditioning Systems
3
a. Identify the characteristics of a central air-conditioning system. b. Explain the differences between unitary and field-erected air-conditioning systems. c. Identify the characteristics of a split air-conditioning system. d. Identify the types of controls commonly used in central air-conditioning systems. e. Summarize the steps required to install central air-conditioning. f. Identify the areas of a central air-conditioning system that must be periodically inspected. g. Explain the tasks that must be completed as part of central air-conditioning system service. h. Understand the operation of variable refrigerant flow (VRF) as it is used in residential heating and cooling systems.
Chapter 33: Commercial Air-Conditioning Systems
4
a. Summarize the features of rooftop units and packaged outdoor air-conditioning units. b. Identify the types of controls commonly used in commercial air-conditioning systems. c. Explain how variable refrigerant flow is incorporated into commercial air-conditioning applications. d. Explain the basic operation of a chiller system. e. Compare the different types of compressors that can be used in chiller systems. f. Explain the basic function and operation of a cooling tower.
Chapter 34: Absorption and Evaporative Cooling Systems
2
a. Explain the absorption refrigeration cycle and process. b. Identify the heat sources that can be used to operate an absorption air-conditioning system. c. Summarize the operation of residential and commercial absorption chillers. d. Compare direct-fired and indirect fired absorption systems. e. Understand the difference between single-effect and double-effect absorption chillers. f. Explain the differences in operation between ammonia and lithium bromide absorption systems. g. Understand how multiple absorption units can be combined in a multiple unit load system. h. Summarize the energy efficiency advantages of an absorption air-conditioning system. i. Explain the basic concepts behind evaporative cooling. j. Understand how a roof pond works. k. Summarize the function of a roof mist cooling system. l. Summarize the steps involved in absorption cooling system service.
Chapter 35: Humidity Control
2
a. Understand the basics of relative humidity (rh), moisture content in the air, and the effect of dry-bulb temperature on humidity levels. b. Summarize the design and operation of a typical dehumidifier. c. Understand the steps involved in humidifier installation and service.
Chapter 36: Thermostats
4
a. Describe how a thermostat can function in different roles in HVACR systems. b. Explain the operating principles of different temperature-reactive components and the switching components used in thermostats. c. List the features and options available in modern thermostats. d. Understand the differences among heating, cooling, combination, and multistage thermostats. e. Understand the purpose and operation of anticipators in thermostats. f. Summarize the operations and applications of line-voltage, low-voltage, and millivolt thermostats. g. Identify and explain the operation of line-voltage thermostats. h. Explain the operation of low-voltage thermostats. i. Understand the use and operation of millivolt thermostats in standing-pilot heating systems. j. Explain the use and operation of wireless and power-stealing thermostats. k. Program and set up a programmable thermostat l. Identify thermostat wiring terminals by their letters. m. Arrange free cooling through the use of an air-side economizer in a forced-air HVAC system. n. Evaluate a building to determine suitable locations for thermostats and remote sensing devices. o. Diagnose an HVAC system that is not operating properly by using its thermostat. p. Diagnose a high current draw on a step-down transformer used with a low-voltage thermostat. q. Understand the operation and purpose of the various components used in a forced-air zoned system. r. Troubleshoot forced-air zoned system that is not operating properly.
Chapter 37: Heating and Cooling Loads
4
a. Understand the principles of heat loss and heat gain. b. Compare the sources of heat loads for heating and heat loads for cooling. c. Explain the relationship between a material’s K-value, C-value, U-value, and R-value and the rate at which heat is transferred through the material. d. Summarize the use of indoor and outdoor design temperatures in calculating heat loads. e. Understand the relationship between surface area and heat transfer rate. f. Compare the techniques for finding a building component’s heat transfer rate using the component’s C-values, K-values, U-value, and R-values. g. Explain how heat load calculations differ depending on whether the building is built on a basement, a slab, or a crawl space. h. Understand infiltration and exfiltration and explain their effects on heat load. i. Summarize the effect of sunlight on cooling loads and methods of reducing sun loads. j. Understand heat lag and its effect on heat loads. k. Identify miscellaneous smaller heat loads within a building that affect the calculation of total heating or cooling loads. l. Use a worksheet or computer program to properly calculate total heating and cooling loads for a building.
Chapter 38: Forced-Air Heating Fundamentals
2
a. Identify the basic components of a forced-air heating system and explain their functions. b. Understand the difference between a condensing and a noncondensing furnace. c. Describe the different types of indoor blower and combustion blower arrangements. d. Compare and contrast upflow, downflow, and horizontal furnaces. e. Summarize the operation of two-stage furnaces and modulating furnaces. f. Explain how makeup air units improve system efficiency and prevent negative pressure from developing in a house. g. Understand how blower function can be controlled using time-delay controls and thermostatic controls. h. Summarize the design and purpose of unit heaters.
Chapter 39: Hydronic Heating Fundamentals
3
a. List the basic components of a hydronic system and explain their functions. b. Explain the purpose of hydronic system water treatment. c. Describe the different types of hydronic system designs. d. Summarize the different methods for installing radiant heating systems. e. Identify various controls used in hydronic systems and explain their functions. f. Perform regular maintenance and service on a steam heating system. g. Explain how to balance a hydronic system and prepare it for initial start-up. h. Troubleshoot boiler and water circulation problems in a hydronic system. i. List the steps required to purge series loop systems, one-pipe systems, and zoned systems.
Chapter 40: Heat Pumps
2
a. Describe the basic operation of a heat pump in heating mode and in cooling mode. b. Summarize the difference between ground-source heat pumps and air-source heat pumps. c. Identify a heat pump system’s principal components. d. Explain how a reversing valve operates and how it controls the direction of refrigerant flow through a heat pump. e. Compare and contrast different types of coils and loops used in heat pump systems. f. List two common methods used to defrost heat pumps. g. Understand how auxiliary heat is used in conjunction with heat pumps. h. Summarize how heat pumps can be combined with solar heating systems. i. Perform routine maintenance and service on heat pump systems.
Chapter 41: Gas-Fired Heating Systems
3
a. Identify the components necessary for and products of combustion. b. Understand how the ratio of air to fuel affects combustion efficiency. c. Describe the differences in design between medium-efficiency and high-efficiency gas furnaces. d. Classify the different types of materials used for chimneys and flue pipes.
Chapter 42: Oil-Fired Heating Systems
3
a. Summarize the basic operation of an oil furnace. b. Identify the characteristics of fuel oil. c. Perform several tests to check the combustion efficiency of an oil-fired heating system. d. Compare the advantages and disadvantages of using a one-pipe or two-pipe fuel delivery system. e. Describe the functions of different fuel line components. f. Identify oil burner components and explain their purposes. g. Explain how stack relays and cad cell relays are used to detect the presence of a flame. h. Describe the difference between interrupted and intermittent ignition. i. Define the various functions of a primary j. Follow code requirements for installing fuel lines and storage tanks for an oil-fired heating system. k. Bleed an oil-fired heating system’s fuel lines and perform other routine maintenance and service procedures. control unit.
Chapter 43: Electric Heating Systems
3
a. Identify the advantages and disadvantages of electric heating systems compared to combustion heating systems. b. Calculate an electric heating system’s heat production when given the system’s wattage or voltage and amperage values. c. Describe the three types of electric heating elements. d. List examples and applications of convection electric heating systems. e. Compare and contrast direct and indirect radiant heating systems. f. Explain the purpose of sequencers and different contactors used in electric heating systems and how they function. g. Describe the operation of airflow and safety control devices in electric heating systems. h. Explain how controls are used in electric baseboard heating and some of their requirements. i. Install, maintain, test, and troubleshoot electric heating systems.
Chapter 44: Solar Power and Thermal Storage
3
a. Understand the nature of solar energy. b. Compare flat-plate collectors, evacuated tube collectors, and concentrating collectors. c. Characterize passive, active, and hybrid solar energy systems. d. Describe the operation of air-based and liquid-based solar heating systems. e. Recall applications for solar heating systems. f. Explain how solar heating can be combined with various supplemental heating sources. g. Describe how solar energy is converted to electricity. h. Explain the operating principles of sensible and latent thermal energy storage.
Chapter 45: Energy Management
4
a. Identify factors affecting heat gain, heat loss, and building energy consumption. b. Explain the purpose of a building control system. c. Understand the energy audit process. d. Describe the three general types of building system controllers. e. Explain the purpose of building control protocols, such as BACnet. f. Summarize principles of control system diagnostics and repair.
Chapter 46: Energy Conservation
2
a. Explain how the construction of a building relates to its heating and cooling efficiency. b. Describe how the degree-day method can be used to estimate heating and cooling costs. c. Differentiate among the various efficiency ratings used to evaluate furnaces, air conditioners, and heat pumps. d. List individual components that can be changed or added to an existing HVAC system to increase energy efficiency. e. Describe alternative systems and solutions that may be used to increase energy conservation. f. Explain the role of the HVACR technician in energy conservation.
Chapter 47: Overview of Commercial Refrigeration Systems
3
a. Recognize the types of commercial refrigeration systems and their applications. b. Explain how and why ice banks are used in certain refrigeration systems. c. Describe the two types of water coolers. d. Describe the different types of evaporators in commercial ice machines. e. List some of the industrial applications of refrigeration systems.
Chapter 48: Special Refrigeration Systems and Applications
2
a. Identify the different types of refrigerant metering devices, evaporators, compressors, and condensers used in transportation refrigeration systems. b. Summarize the operation of various expendable refrigeration systems. c. Explain how thermoelectric couples produce heating and cooling using electricity. d. Summarize the operation of vortex tubes, steam jet systems, and refrigerant jet systems. e. Describe the operation of a basic Sterling refrigeration system.
Chapter 49: Commercial Refrigeration System Configurations
2
a. Explain the difference between packaged and split commercial refrigeration systems. b. Understand the operation and purpose of various components used in sophisticated commercial refrigeration systems. c. Identify applications for multiple-evaporator systems. d. Summarize the different methods of achieving variable capacity in modulating refrigeration systems. e. Explain the refrigeration cycle in compound and cascade systems. f. Describe the purpose and operation of secondary loop refrigeration systems.
Chapter 50: Understanding Heat Loads and System Thermodynamics
3
a. Understand the relationship between total heat load, service heat load, and heat leakage load. b. Compute a system’s heat leakage load. c. Calculate a system’s service heat load manually and by using manufacturer’s tables. d. Use heat leakage load, service heat load, and all applicable miscellaneous heat loads to calculate a system’s total heat load. e. Compute the total heat load for a water cooler. f. Summarize the thermodynamic principles at work in the basic refrigeration cycle. g. Identify the various lines on a pressure-enthalpy diagram. h. Interpret the graphs of different refrigeration cycles on pressure-enthalpy diagrams.
Chapter 51: Commercial Refrigeration Component Selection
2
a. Identify the factors that affect compressor sizing. b. Calculate a compressor’s required capacity based on its total heat load and operating cycle. c. Summarize the factors that affect the heat transfer rates of evaporators and condensers. d. Use tables from manufacturers to size compressors, condensers, and evaporators. e. List the basic criteria that must be considered when sizing refrigerant lines.
Chapter 52: Installing Commercial Systems
2
a. Summarize some of the basic regulations found in most codes. b. Identify procedures for locating and mounting condensing units and evaporators. c. Determine where to mount thermostatic expansion valve sensing bulbs based on suction line tubing size. d. Install various components, such as valves, filter-driers, and sight glasses, along refrigerant lines. e. Properly mount and install open-drive compressor motors and also hermetic compressors. f. Test a refrigeration installation for leaks by using leak detection devices, a standing pressure test, and a standing vacuum test. g. Charge a system with refrigerant using either the low-side method or the high-side method.
Chapter 53: Troubleshooting Commercial Systems—System Diagnosis
2
a. Recognize the effects of an undercharged refrigeration system b. Recognize the effects of an overcharged refrigeration system. c. Recognize the effects of non-condensable in a refrigeration system d. Identify causes of suction line pressure drop. e. Summarize the effects of having moisture in a refrigeration system f. Check a commercial refrigeration system’s refrigerant charge. g. Differentiate among the different causes of high head pressure. h. Analyze a refrigeration system that runs continuously to determine its root cause. i. Evaluate a refrigeration system that produces little or no cooling. j. Analyze a refrigeration system that will not run to determine its root cause. k. Troubleshoot basic problems in ice machines.
Chapter 54: Troubleshooting Commercial Systems—Component Diagnosis
2
a. Test the components of a system to determine what causes it to short cycle. b. Identify and distinguish the various causes of abnormal noises created by commercial refrigeration systems before implementing a remedy. c. Identify restrictions and pressure drops in various inline components using a temperature survey.
Chapter 55: Servicing Commercial Systems
3
a. Properly pump down or move the refrigerant charge for system service. b. Perform atmospheric balancing (pressure equalizing) before opening a system to atmosphere for service. c. Safely remove a compressor from a system for replacement. d. Safely replace an external electric motor. e. Safely service a refrigeration system with a motor burnout in a hermetic compressor. f. Add refrigerant oil to a refrigerant system using several different methods. g. Safely remove, repair, and install air-cooled and water-cooled condensers. h. Diagnose and repair or replace water valves. i. Perform basic cooling tower maintenance. j. Remove, repair, and install expansion valves. k. Adjust the setting of a thermostatic expansion valve (TXV). l. Diagnose, repair, install, and adjust evaporator pressure regulators (EPRs) and hot-gas valves. m. Remove and replace service valves and solenoid valves.
Construction Industry Outreach Training Program
10
The 10-hour Construction Industry Outreach Training Program is intended to provide an entry-level construction worker’s general awareness on recognizing and preventing hazards on a construction site. The training covers a variety of construction safety and health hazards which a worker may encounter at a construction site. OSHA recommends this training as an orientation to occupational safety and health. Workers must receive additional training on hazards specific to their job. Training should emphasize hazard identification, avoidance, control and prevention, not OSHA standards. Instructional time must be a minimum of 10 hours. Breakdown of topics is as follows: a. Mandatory – 4 Hours: Four topics to be taught, ranging from one-half to two hours each (Introduction to OSHA; OSHA Focus Four Hazards; Personal Protective and Lifesaving Equipment; Health Hazards in Construction). b. Elective – 2 Hours: Choose at least two of these topics for a minimum of one-half hour each. Must cover at least two hours. c. Optional – 4 Hours: Learn any other construction industry hazards or policies and/or expand on the mandatory or elective topics, minimum of one-half hour each.
Construction Industry Requirement Course Topics
10
a. Introduction to OSHA – One Hour • OSH Act, General Duty Clause, Employer and Employee Rights and Responsibilities, Whistleblower Rights, Recordkeeping basics. • Inspections, Citations, and Penalties. • General Safety and Health Provisions, Competent Person, Subpart C. • Value of Safety and Health. b. OSHA Website, OSHA 800 number and available resources. c. OSHA Focus Four Hazards – Two Hours (must cover all four areas – minimum 15 minutes on each): • Fall Protection, Subpart M (e.g., floors, platform, roofs) • Electrical, Subpart K (e.g., overhead power lines, power tools and cords, temporary wiring, grounding) • Struck by (e.g., falling objects, trucks, cranes) • Caught in/between (e.g., trench hazards, equipment) d. Personal Protection and Lifesaving Equipment – 30 Minutes, Subpart E. e. Health Hazards in Construction – 30 Minutes (e.g., noise, hazards communication and crystalline silica). f. Electives. Choose at least two of the following topics – must add up to at least two hours, minimum one-half hour each: • Materials Handling, Storage, Use and Disposal, Subpart H • Tools – Hand and Power, Subpart I • Scaffolds, Subpart L • Cranes, Derricks, Hoists, Elevators, and Conveyors, Subpart N • Excavations, Subpart P • Stairways and Ladders, Subpart X
Introduction to HVAC
8
Covers the basic principles of heating, ventilating, and air conditioning, career opportunities in HVAC, and how apprenticeship programs are constructed. Basic safety principles, as well as trade licensure and EPA guidelines, are also introduced.
Trade Mathematics
10
Explains how to solve HVAC/R trade related problems involving the measurement of lines, area, volume, weights, angles, pressure, vacuum, and temperature. Also includes a review of scientific notation, powers, roots, and basic algebra and geometry.
Basic Electricity
13
Introduces the concept of power generation and distribution, common electrical components, AC and DC circuits, and electrical safety as it relates to the HVAC field. Introduces reading and interpreting wiring diagrams.
Introduction to Heating
15
Covers the fundamentals of heating systems and the combustion process. The different types and designs of gas furnaces and their components, as well as basic procedures for their installation and service, is provided.
Introduction to Cooling
30
Explains the fundamental operating concepts of the refrigeration cycle and identifies both primary and secondary components found in typical HVAC/R systems. Common refrigerants are introduced as well. Describes the principles of heat transfer and the essential pressure temperature relationships of refrigerants. Basic control concepts for simple systems are also introduced.
Introduction to Air Distribution Systems
15
Describes the factors related to air movement and its measurement in common air distribution systems. The required mechanical equipment and materials used to create air distribution systems are also presented. Basic system design principles for both hot and cold climates are introduced.
Basic Copper and Plastic Piping Practices
10
Explains how to identify types of copper tubing and fittings used in the HVAC/R industry and how they are mechanically joined. The identification and application of various types of plastic piping, along with their common assembly and installation practices, are also presented.
Soldering and Brazing
10
Introduces the equipment, techniques, and materials used to safely join copper tubing through both soldering and brazing. The required PPE, preparation, and work processes are covered in detail. The procedures for brazing copper to dissimilar materials are also provided.
Basic Carbon Steel Piping Practices
10
Explains how to identify various carbon steel piping materials and fittings. The joining and installation of threaded and grooved carbon steel piping systems is covered, with detailed coverage of threading and grooving techniques included.
Universal Certification for EPA under Section 608
24
a. Ozone Depletion • Destruction of ozone by chlorine. • Presence of chlorine in CFC and HCFC refrigerants. • Identification of CFC, HCFC, and HFC refrigerants (not chemical formulas, but idea that R-12 is a CFC, R-22 is an HCFC, R-134 is an HFC, etc.). • Idea that CFCs have higher ozone-depletion potential (ODP) than HCFCs, which in turn have higher ODP than HFCs. • Health and environmental effects of ozone depletion. • Evidence of ozone depletion and role of CFCs and HCFCs. b. Clean Air Act and Montreal Protocol • CFC phase-out date. • Venting prohibition at servicing. • Venting prohibition at disposal. • Venting prohibition on substitute refrigerants in November 1995. • Maximum penalty under CAA. • Montreal Protocol (international agreement to phase out production of ozone-depleting substances). c. Section 608 Regulations • Definition/identification of high- and low-pressure refrigerants. • Definition of system-dependent vs. self-contained recovery/recycling equipment. • Identification of equipment covered by the rule (all air-conditioning and refrigeration equipment containing CFCs or HCFCs, except motor vehicle air conditioners). • Need for third-party certification of recycling and recovery equipment manufactured after November 15, 1993. • Standard for reclaimed refrigerant (ARI 700). d. Substitute Refrigerants and Oils • Absence of "drop-in" replacements. • Incompatibility of substitute refrigerants with many lubricants used with CFC and HCFC refrigerants and incompatibility of CFC and HCFC refrigerants with many new lubricants (includes identification of lubricants for given refrigerants, such as esters with 134; alkyl benzenes for HCFCs). • Fractionation problem—tendency of different components of blends to leak at different rates. e. Refrigeration • Refrigerant states (vapor vs. liquid) and pressures at different points of refrigeration cycle; how/when cooling occurs. • Refrigeration gauges (color codes, ranges of different types, proper use). f. Three R's • Recover. • Recycle. • Reclaim. g. Recovery Techniques • Need to avoid mixing refrigerants. • Factors affecting speed of recovery (ambient temperature, size of recycling or recovery equipment, hose length and diameter, etc.). h. Dehydration Evacuation • Need to evacuate system to eliminate air and moisture at the end of service. i. Safety • Risks of exposure to refrigerant (e.g., oxygen deprivation, cardiac effects, frostbite, long-term hazards). • Personal protective equipment (gloves, goggles, self-contained breathing apparatus—SCBA—in extreme cases, etc.). • Reusable (or "recovery") cylinders vs. disposable cylinders (ensure former DOT approved, know former's yellow and gray color code, never refill latter). • Risks of filling cylinders more than 80 percent full. • Use of nitrogen rather than oxygen or compressed air for leak detection. • Use of pressure regulator and relief valve with nitrogen. j. Shipping • Labels required for refrigerant cylinders (refrigerant identification, DOT classification tag). k. TYPE 1 (Small Appliances) • Recovery Requirements. i. Definition of "small appliance." ii. Evacuation requirements for small appliances with and without working compressors using recovery equipment manufactured before November 15, 1993. iii. Evacuation requirements for small appliances with and without working compressors using recovery equipment manufactured after November 15, 1993. • Recovery Techniques i. Use of pressure and temperature to identify refrigerants and detect non-condensable. ii. Methods to recover refrigerant from small appliances with inoperative compressors using a system-dependent or "passive" recovery device (e.g., heat and sharply strike the compressor, use a vacuum pump with non-pressurized recovery container). iii. Need to install both high and low side access valves when recovering refrigerant from small appliances with inoperative compressors. iv. Need to operate operative compressors when recovering refrigerant with a system-dependent or "passive" recovery device. v. Should remove solderless access fittings at conclusion of service vi. 134a as likely substitute for 12. • Safety i. Decomposition products of refrigerants at high temperatures (HCl, HFl etc.) l. TYPE 2 (High-Pressure) • Leak Detection i. Signs of leakage in high-pressure systems (excessive superheat, traces of oil for hermetics). ii. Order of preference for leak test gases (nitrogen alone best, but nitrogen with trace quantity of 22 better than pure refrigerant). • Leak Repair Requirements i. Allowable annual leak rate for commercial and industrial process refrigeration. ii. Allowable annual leak rate for other appliances containing more than 50 lbs. of refrigerant. • Recovery Techniques i. Recovering liquid at beginning of recovery process speeds up process. ii. Other methods for speeding recovery (chilling recovery vessel, heating appliance or vessel from which refrigerant is being recovered). iii. Methods for reducing cross-contamination and emissions when recovery or recycling machine is used with a new refrigerant. iv. Need to wait a few minutes after reaching required recovery vacuum to see if system pressure rises (indicating that there is still liquid refrigerant in the system or in the oil). • Recovery Requirements i. Evacuation requirements for high-pressure appliances in each of the following situations: Disposal; Major vs. non-major repairs; Leaky vs. non-leaky appliances; Appliance (or component) containing less vs. more than 200 lbs.; Recovery/recycling equipment built before vs. after November 15, 1993. ii. Definition of "major" repairs. iii. Prohibition on using system-dependent recovery equipment on systems containing more than 15 pounds of refrigerant. • Refrigeration i. How to identify refrigerant in appliances. ii. Pressure-temperature relationships of common high-pressure refrigerants (may use standard temperature-pressure chart—be aware of need to add 14.7 to translate psig to psia). iii. Components of high-pressure appliances (receiver, evaporator, accumulator, etc.) and state of refrigerant (vapor vs. liquid) in them. • Safety i. Should not energize hermetic compressors under vacuum. ii. Equipment room requirements under ASHRAE Standard 15 (oxygen deprivation sensor with all refrigerants). m. TYPE 3 (Low-Pressure) • Leak Detection i. Order of preference of leak test pressurization methods for low-pressure systems (first: hot water method or built-in system heating/pressurization device such Prevac; second: nitrogen). ii. Signs of leakage into a low-pressure system (e.g., excessive purging). iii. Maximum leak test pressure for low-pressure centrifugal chillers. • Leak Repair Requirements i. Allowable annual leak rate for commercial and industrial process refrigeration. ii. Allowable annual leak rate for other appliances containing more than 50 lbs. of refrigerant. • Recovery Techniques i. Recovering liquid at beginning of recovery process speeds up process. ii. Need to recover vapor in addition to liquid. iii. Need to heat oil to 130°F before removing it to minimize refrigerant release. iv. Need to circulate or remove water from chiller during refrigerant evacuation to prevent freezing. v. High-pressure cut-out level of recovery devices used with low-pressure appliances. • Recharging Techniques i. Need to introduce vapor before liquid to prevent freezing of water in the tubes. ii. Need to charge centrificals through evaporator charging valve. • Recovery Requirements i. Evacuation requirements for low-pressure appliances in each of the following situations: Disposal; Major vs. non-major repairs; Leaky vs. non-leaky appliances; Appliance (or component) containing less vs. more than 200 lbs.; Recovery/recycling equipment built before vs. after November 15, 1993. ii. Definitions of "major" and "non-major" repairs. iii. Allowable methods for pressurizing a low-pressure system for a non-major repair (controlled hot water and system heating/pressurization device such as Prevac). iv. Need to wait a few minutes after reaching required recovery vacuum to see if system pressure rises (indicating that there is still liquid refrigerant in the system or in the oil). • Refrigeration i. Purpose of purge unit in low-pressure systems. ii. Pressure-temperature relationships of low-pressure refrigerants. • Safety i. Equipment room requirements under ASHRAE Standard 15 (oxygen deprivation sensor with all refrigerants) ii. Under ASHRAE Standard 15, need to have equipment room refrigerant sensor for 123.
Alternating Current
10
Module One (03206-13) presents the basic concepts of alternating current generation and use. It also discusses how single- and three-phase alternating current is used to power resistive and inductive circuits in HVAC/R equipment. Various types of transformers used in HVACR systems are identified. The basic operation of single- and three-phase motors is explained. In addition, the process of safely testing AC-powered devices is covered.
Compressors
12
Module Two (03302-13) presents refrigerant compressors. Since the compressor is considered the heart of any HVAC system, its good health and well-being are crucial to overall system performance and reliability. Compressors can take many forms, but they all perform the same basic function. They create the pressure differential in the system that allows refrigerant to move through the metering device and through the condenser and evaporator coils where heat is exchanged. Because the compressor is the most expensive component in most HVACR systems, it is important that technicians be able to correctly diagnose and correct problems that can affect compressor operation to avoid a costly compressor replacement.
Refrigerants and Oils
12
Module Three (03301-13) discusses the refrigerants and oils used in modern refrigeration and air conditioning systems. Today, new technologies and stringent environmental laws are driving changes in the HVAC industry. Older refrigerants that damage the environment are being phased out and replaced with more environmentally-friendly refrigerants. These new refrigerants often require new compressor lubricating oils. These modern refrigerants and oils also have new handling and service requirements with which technicians must be familiar.
Leak Detection, Evacuation, Recovery, and Charging
30
Module Four (03205-13) provides trainees with guidance related to servicing the refrigerant circuit of HVAC systems. The four essential service tasks—leak detection, evacuation, recovery, and charging—are covered in detail. In addition, information related to the US EPA’s requirements for provide these services in an environmentally sound manner are also provided. Developing the necessary skills to provide these services are vital to the future success of trainees in the HVAC/R trade. To that end, a significant amount of this module is devoted to hands-on practice and the successful completion of its required performance tasks.
Metering Devices
12
Module Five (03303-13) introduces metering devices used in the mechanical refrigeration cycle. The primary function of metering devices is presented, along with related components such as the distributor. The operation of capillary tube, fixed-orifice, and expansion-type metering devices is explored in detail. In addition, the process of selecting and installing thermal expansion valves specifically is covered.
Heat Pumps
20
Module Six (03211-13) introduces heat pumps, a very efficient form of electric heat. Compared pumps can consistently operate at higher energy efficiency. This module presents the operation of heat pump systems in detail with additional emphasis on the most common form of supplemental heat, electric resistance heating elements. The installation considerations of both split and packaged heat pumps systems are also reviewed.
Basic Maintenance
20
Module Seven (03215-13) introduces trainees to the common tasks associated with basic maintenance activities. Specific tasks, such as lubrication and belt installation, are reviewed in detail. In addition, the module pro- vides detailed coverage of the tasks required to complete thorough maintenance inspections of gas furnaces and common cooling/heat pump systems.
Chimneys, Vents and Flues
5
Module Eight (03202-13) covers the chimneys, vents, and flues that are used with fuel-burning furnaces and boilers. All fuel-burning appliances must have adequate air for complete combustion and must have a means to safely remove the products of combustion. Different types of fuel-fired furnaces and boilers have different and unique requirements for venting the products of combustion.
Sheet Metal Duct Systems
10
Module Nine (03213-13) covers sheet metal duct systems. While other materials can be used to fabricate air ducts, sheet metal has been and continues to be one of the most popular materials for this purpose. Major advantages of sheet metal ducts systems include low resistance to airflow, strength, and durability. In addition to using time-tested assembly methods, modern sheet metal duct systems need to be sealed to prevent leakage of conditioned air, and insulated to prevent heat loss or heat gain through the walls of the duct.
Fiberglass and Fabric Duct Systems
7
Module Ten (03214-13) reviews the application and methods of fabricating fiberglass duct systems. In addition, the installation guidelines for installing a fiberglass system are presented, along with the methods to repair damaged components. The module concludes with coverage of fabric-based duct systems, which have become increasingly popular in a variety of applications.
Commercial Airside Systems
12
Module Eleven (03201-13) introduces the air distribution systems used in commercial structures such as schools and office buildings that are divided into comfort heating and cooling zones. The module covers the various types of systems, as well as the air terminals and air source equipment used in these systems. Accessories commonly used with commercial systems are also covered.
Air Quality Equipment
5
Module Twelve (03204-13) introduces the factors related to indoor air quality and human comfort. Since humidity is a common comfort factor for all types of buildings, the equipment used to control humidity is presented in detail. The module also covers the air filtration materials and the introduction of outside air into the indoor environment.
Introduction to Hydronic Systems
12
Module Thirteen (03203-13) introduces hydronic heating systems. In hydronic heating systems, fluids (typically water) are used to transfer heat. Fuels such as gas or oil are used to heat the water in a boiler. Pumps then circulate that heated water throughout the structure where terminal devices such as radiators release the heat into different areas.
Fasteners, Hardware, and Wiring Terminations
10
(Module ID 03313-13) Covers a variety of fasteners, hardware, and wiring terminations used in HVAC systems including the installation of these components.
Control Circuit and Motor Troubleshooting
30
(Module ID 03314-13) Provides information and skills to troubleshoot control circuits and electric motors found in heating and cooling equipment.
Troubleshooting Cooling
20
(Module ID 03210-13) Provides guidance related to troubleshooting cooling systems.
Troubleshooting Heat Pumps
12
(Module ID 03311-13) Provides a thorough review of heat pump systems, operating cycle and troubleshooting procedures for components.
Troubleshooting Gas Heating
12
(Module ID 03209-13) Covers information and skills needed to troubleshoot gas-fired furnaces and boilers.
Troubleshooting Oil Heating
12
(Module ID 03310-13) Describes the construction and operation of oil-fired heating systems and their components. Includes servicing and testing of oil furnaces and procedures for isolating and correcting oil furnace malfunctions.
Troubleshooting Accessories
7
(Module ID 03312-13) Delivers information and skills needed to troubleshoot various air treatment accessories used with heating and cooling equipment.
Zoning, Ductless, and Variable Refrigerant Flow Systems
12
(Module ID 03315-13) Introduces the information and skills needed to troubleshoot and repair zoned, ductless, and variable refrigerant flow systems.
Commercial Hydronic Systems
10
(Module ID 03305-13) Reviews basic properties of water and describes how water pressure is related to the movement of water through piping systems. Describes various types and components of commercial hot-water heating and chilled-water cooling systems, and examines how those systems function.
Steam Systems
10
(Module ID 03306-13) Focuses on the use of steam for storing and moving energy in HVAC systems. Reviews the fundamentals of water that relate to steam and describes the basic steam system cycle; Discusses a steam system’s operational components–steam boilers and their accessories and controls; steam system loads, including heat exchangers/converters and terminal devices. Steam system valves and piping are covered in detail, including common types of piping arrangements, the components of a condensate return/feedwater system, steam and condensate pipe sizing; and pressure-reducing valves and thermostatic valves.
Retail Refrigeration System
15
(Module ID 03304-13) Covers the applications, principles, and troubleshooting of retail refrigeration systems.
Customer Relations
5
(Module ID 03316-13) Presents the importance of establishing good relations with customers and provides guidance on how to achieve that goal. Focuses on ways for a technician to make a good first impression and describes how to communicate in a positive manner with customers. The elements of a service call and dealing with different types of problem customers are also covered.
Water Treatment
12
(Module ID 03308-13) Explains water problems encountered in heating and cooling systems and identifies water treatment methods and equipment. Covers basic water testing procedures and chemistry.
Indoor Air Quality
10
(Module ID 03403-13) Defines the issues associated with indoor air quality and its effect on the health and comfort of building occupants. Provides guidelines for performing an IAQ survey and covers the equipment and methods used to monitor and control indoor air quality.
Energy Conservation Equipment
7
(Module ID 03404-13) Covers heat recovery/reclaim devices, as well as other energy recovery equipment used to reduce energy consumption in HVACR systems.
Building Management Systems
12
(Module ID 03405-13) Explains how computers and microprocessors are used to manage zoned HVAC systems. Provides coverage of various network protocols and systems controllers, and introduces apprentices to the various means of connection and system interface.
System Air Balancing
15
(Module ID 03402-13) Covers air properties and gas laws, as well as the use of psychrometric charts. Describes the tools, instruments, and procedures used to balance an air distribution system.
System Startup and Shutdown
15
(Module ID 03406-13) Presents the procedures for startup, shutdown of hot water, steam heating, chilled water, and air handling systems, typical cooling towers and packaged HVAC units. The procedures for both short- and long-term shutdowns are included.
Construction Drawings and Specifications
12
(Module ID 03401-13) Teaches how to interpret drawings used in commercial construction, including mechanical drawings, specifications, shop drawings, and as-built’ s. Explains how to perform takeoff procedures for equipment, fittings, ductwork, and other components.
Heating and Cooling System Design
25
(Module ID 03407-13) Identifies factors that affect heating and cooling loads. Explains the process by which heating and cooling loads are calculated, and how load calculations are used in the selection of heating and cooling equipment. Covers basic types of duct systems and their selection, sizing, and installation requirements.
Commercial and Industrial Refrigeration Systems
20
(Module ID 03408-13) Expands on the study of product and process refrigeration equipment by describing systems used in cold storage and food processing applications, as well as transportation refrigeration. Various types of defrost systems are covered in detail.
Alternative and Specialized Heating and Cooling Systems
10
(Module ID 03409-13) Describes alternative devices used to reduce energy consumption, including wood, coal, and pellet-fired systems, waste-oil heaters, geothermal heat pumps, solar heating, in-floor radiant heating, and direct-fired makeup units. Also introduces application-specific computer room environmental and air turnover systems.
Fundamentals of Crew Leadership
20
(Module ID 46101-11) Outlines the duties of the crew leader including assessing hazards, OSHA reporting of accidents, encouraging production while maintaining a high quality of work, holding safety meetings and training, adherence to DOT and other job-related rules and regulations, planning for job continuity, and encouraging and mentoring of the crew.