in on-the-job training and related instruction.
Machine Operator
USDOL
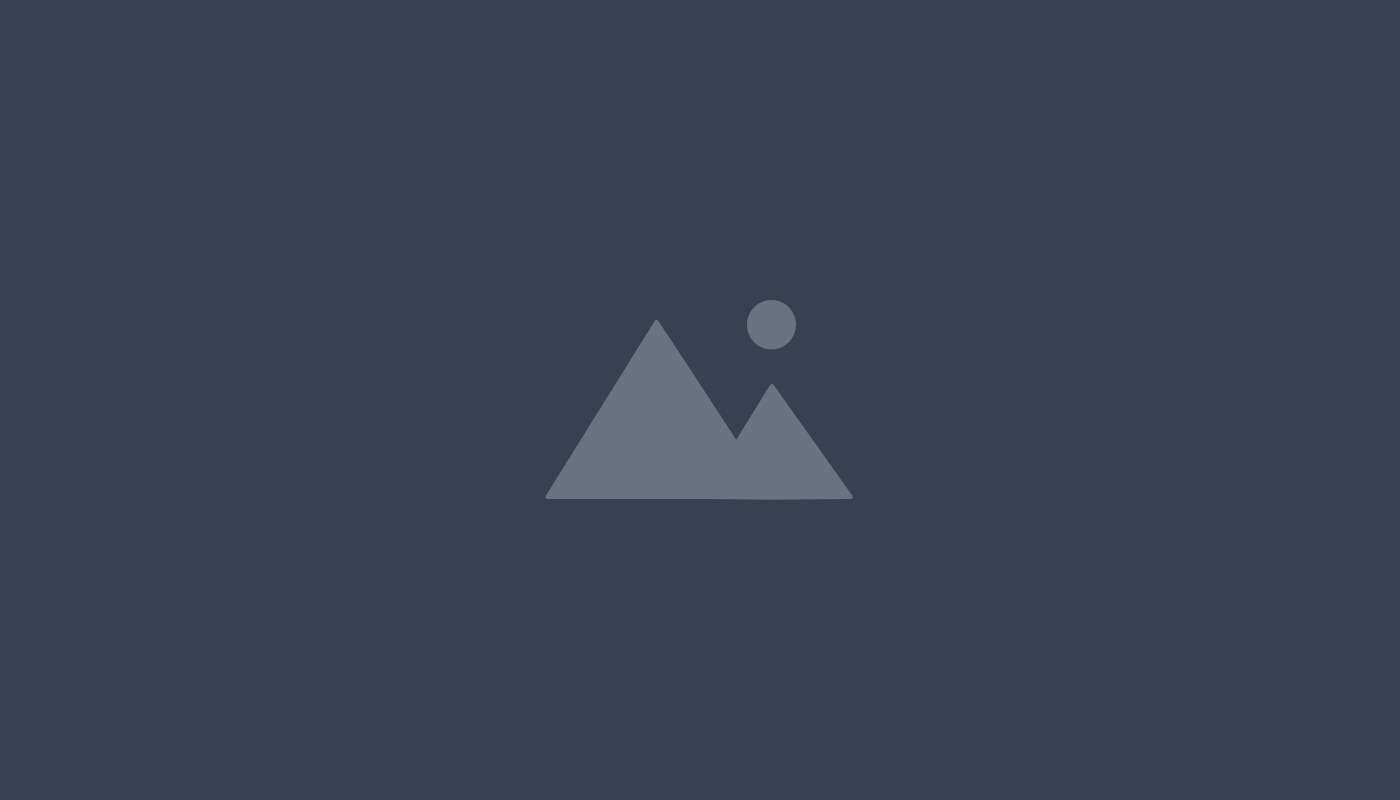
Work Process Content
On the Job Training
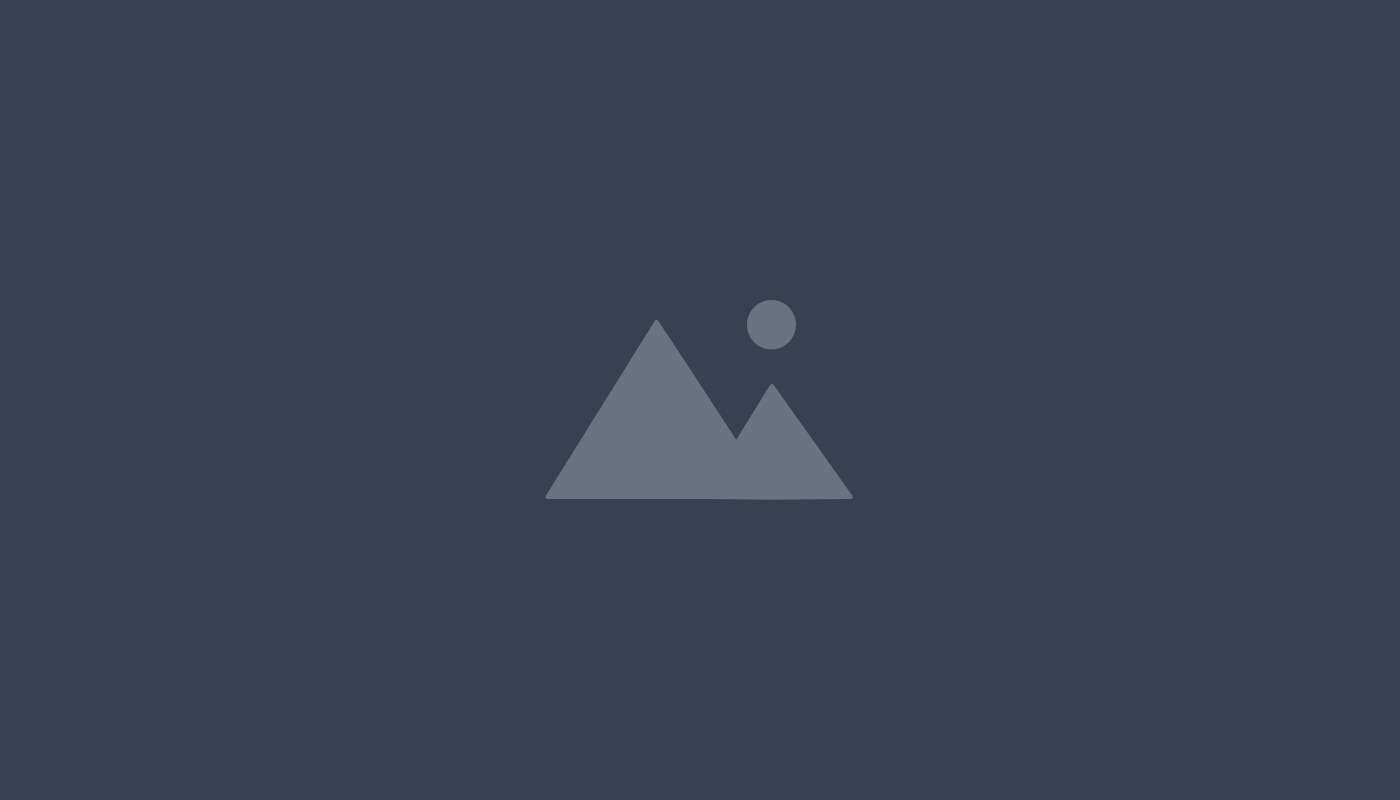
General
59
400
- Demonstrate awareness of employer’s safety policies. Report any that do not fit.
- Identify proper tools and use.
- Demonstrate proper personal lifting techniques.
- Identify and conduct pre-use inspection appropriate task related lifting equipment, such as hoists, straps, lifts, etc.
- Demonstrate proper use of appropriate lifting equipment.
- Obtain proper certification/license for operating a forklift and other lifting devices.
- Demonstrate proper and safe operation of forklift and other motor-operated vehicles.
- If you are trained and able; Identify, ventilate, and enter a confined spaces associated with your tasks (OSHA 1910.146).
- Adhere to employer’s emergency/hazard response procedures.
- Identify location of first-aid materials.
- Follow other applicable OSHA or employer safety regulations that you are trained on and understand.
- Adhere to employer fire-extinguishing procedures.
- Using personal fall arrest equipment when working from an elevated position as part of your tasks, (I.E., elevated loading station.)
- Maintain a safe and organized work area.
- Identify location and demonstrate proper use of Material Safety Data Sheets (MSDS).
- Demonstrate awareness of material moving equipment in area, such as forklifts, tuggers, cranes, hoists, etc.
- Follow employer-specific safety procedures for identifying and addressing potential hazards.
- Demonstrate awareness of employer’s first-aid procedures.
- Demonstrate awareness of employer’s procedures for bloodborne pathogens.
- Display knowledge of materials, methods, and tools involved in production.
- Understand the basic principles of electricity and electrical power circuits, as well as the associated task related risks.
- Interpret electrical diagrams: Read and comprehend blueprints and electrical diagrams; understand electricity theory and task related electronic components.
- Use computer tools to predict performance.
- Understand batteries and battery packs.
- Identify schematic symbols.
- Understand cell capacity.
- Understanding Task related Measurement of battery cell current.
- Understand how cells store energy.
- Understand how electrochemical cells work.
- Explain the charge-discharge process.
- State function and control of EV Batteries.
- Meet deadlines: Ensure operative processes are finished at a previously agreed-upon time.
- Follow necessary procedures to ensure all line moves are made, safely, quickly, and as scheduled.
- Lift raw material, finished product and packed items manually.
- Lift raw material, finished product and packed items using hoist or lift.
- Count finished product to determine if product orders are complete.
- Mark or tag identification on parts.
- Add labels or stencils such as lot numbers or shipping destinations.
- Complete all work according to specifications and codes.
- Complete daily quota of production.
- Ensure proper job is completed.
- Assist other production workers.
- Handle, install, position and move materials.
- Stock and sort product for packaging or filling machine operation.
- Replenish stock and supplies.
- Understand the line of operation to fill for/assist team members.
- Assist with the maintenance of production schedule and quality.
- Communicate with supervisor, peers and subordinates.
- Oversee logistics of finished products: Ensure that the processes of packing, storage and shipment of finished products meet the requirements.
- Display knowledge of principles and procedures for personnel relations.
- Understanding positive example in attitude, behavior, and personal pride.
- Provide guidance and input i.e. setting performance standard and monitoring performance.
- Understanding how to get members of a team/crew to work together to accomplish a task.
- Inspect employee work to ensure quality is maintained.
- Take measures to encourage teamwork.
- Understanding how to direct and lead workers engaged in production line activities.
- Ensure all daily and weekly goals are achieved and make adjustments to achieve positive results.
- Understanding how to meet all production line timelines are met.
- Identify the necessary PPE for use of the machine.
Mixing
50
400
- Identify common safety hazards associated with the machine.
- Understand the machine's built-in safety features.
- Utilize the machine's safety features to turn it off in case of an emergency.
- Apply knowledge of the expected time and conditions for machine tasks so work is completed safely, to know when in cycles the machine requires closer observation, and when new workpieces should be staged.
- Understand using OSHA and employer-specific lockout/tag-out and energy control procedures.
- Add or mix chemicals or ingredients for processing, using hand tools or other devices.
- Compound or process ingredients or dyes, according to formulas.
- Dislodge and clear simple jammed materials or other items from machinery or equipment, using hand tools.
- Examine materials, ingredients, or products visually or with hands to ensure conformance to established standards.
- Mix or blend ingredients by starting machines and mixing for specified times.
- Tend accessory equipment, such as pumps or conveyors, to move materials or ingredients through production processes.
- Transfer materials, supplies, or products between work areas, using moving equipment or hand tools.
- Perform fault analysis on the machine.
- Identify parts of the machine and their use.
- Identify tools used when using the machine.
- Understand operating settings and limits.
- Identify the necessary PPE for use of the machine.
- Identify common safety hazards associated with the machine.
- Understand the machine’s built-in safety features.
- Utilize the machine's safety features to turn it off in case of an emergency.
- Apply knowledge of the expected time and conditions for machine tasks so work is completed safely, to know when in cycles the machine requires closer observation, and when new workpieces should be staged.
- Understand using OSHA and employer-specific lockout/tag-out and energy control procedures.
- Gather necessary supplies in the proper quantity following the designated recipe for mixture.
- Ensure the quality of mixer parts, identifying the need for any replacement before the production run.
- Pour materials into the machine prior to starting production.
- Add or mix chemicals or ingredients for processing, using hand tools or other devices.
- Compound or process ingredients or dyes, according to formulas.
- Dislodge and clear simple jammed materials or other items from machinery or equipment, using hand tools.
- Examine materials, ingredients, or products visually or with hands to ensure conformance to established standards.
- Mix or blend ingredients by starting machines and mixing for specified times.
- Open valves to drain slurry from mixers into storage tanks.
- Operate or tend machines to mix or blend any of a wide variety of materials including explosive ingredients.
- Read work orders to determine production specifications or information.
- Record operational or production data on specified forms.
- Stop mixing or blending machines when specified product qualities are obtained and open valves and start pumps to transfer mixtures.
- Tend accessory equipment, such as pumps or conveyors, to move materials or ingredients through production processes.
- Transfer materials, supplies, or products between work areas, using moving equipment or hand tools.
- Unload mixtures into containers or onto conveyors for further processing.
- Weigh or measure materials, ingredients, or products to ensure conformance to requirements.
- Mix or blend ingredients by starting machines and mixing for specified times.
- Pause the machine mid-cycle, understanding use of electronic stops
- Shut down the machine, when needed.
- Clean up the machine following a production run.
- Monitor machine for proper operation.
- Observe machine indicator lights and gauges.
- Check viscosity meter during production ensure a value in the proper range.
- Fault analysis on the machine.
- Identify parts of the machine and their use.
- Identify tools used when using the machine.
- Understand operating settings and limits.
Electrode Prep
93
700
- Identify the necessary PPE for use of the machine.
- Identify common safety hazards associated with the machine.
- Understand the machine’s built-in safety features.
- Utilize the machine's safety features to turn it off in case of an emergency.
- Apply knowledge of the expected time and conditions for machine tasks so work is completed safely, to know when in cycles the machine requires closer observation, and when new workpieces should be staged.
- Understand using OSHA and employer-specific lockout/tag-out and energy control procedures.
- Set up machine dies.
- Add slurry mixture to machine.
- Ensure HMI and other monitoring parts are functioning correctly.
- Start the machine.
- Pause the machine mid-cycle, understanding use of electronic stops
- Shut down the machine, when needed.
- Clean up the machine following a production run.
- Monitor machine for proper operation.
- Observe machine indicator lights and gauges.
- Manually adjust dies by hand in response to HMI data.
- Visually monitor machine output for quality.
- Monitor production to avoid contaminates and weakness in the roll.
- Monitor coating thickness during process.
- Monitor moisture levels during process.
- Monitor solvent recovery.
- Perform specified quality samples/checks on materials produced.
- Check completed rolls for consistency of thickness across each roll.
- Perform weight test of a punched piece of roll.
- Test rolls for moisture, streaks, and strength.
- Perform fault analysis on the machine.
- Identify parts of the machine and their use.
- Identify tools used when using the machine.
- Identify the necessary PPE for use of the machine.
- Identify common safety hazards associated with the machine.
- Understand the machine’s built-in safety features.
- Utilize the machine's safety features to turn it off in case of an emergency.
- Apply knowledge of the expected time and conditions for machine tasks so work is completed safely, to know when in cycles the machine requires closer observation, and when new workpieces should be staged.
- Understand using OSHA and employer-specific lockout/tag-out and energy control procedures.
- Ensure drying temperatures are set at the desired level.
- Ensure monitoring parts are functioning correctly.
- Start the machine.
- Pause the machine mid-cycle, understanding use of electronic stops.
- Shut down the machine, when needed.
- Clean up the machine following a production run.
- Monitor machine for proper operation.
- Observe machine indicator lights and gauges.
- Visually monitor machine output for quality.
- Monitor production to avoid contaminates and weakness in the roll.
- Monitor drying temperature is ensure desired level at each drying zone.
- Monitor moisture levels during process.
- Monitor center to edge homogeneity during drying process.
- Check for cracking during process.
- Perform specified quality samples/checks on materials produced.
- Test rolls for moisture, streaks, and strength.
- Fault analysis fault on the machine.
- Identify parts of the machine and their use.
- Identify tools used when using the machine.
- Identify the necessary PPE for use of the machine.
- Identify common safety hazards associated with the machine.
- Understand the machine’s built-in safety features.
- Utilize the machine's safety features to turn it off in case of an emergency.
- Apply knowledge of the expected time and conditions for machine tasks so work is completed safely, to know when in cycles the machine requires closer observation, and when new workpieces should be staged.
- Understand using OSHA and employer-specific lockout/tag-out and energy control procedures.
- Identify any machine parts that need maintenance or replacement.
- Set the depth of the calendaring tool.
- Start the machine.
- Pause the machine mid-cycle, understanding use of electronic stops
- Shut down the machine, when needed.
- Clean up the machine following a production run.
- Monitor machine for proper operation.
- Observe machine indicator lights and gauges.
- Slit electrodes to match final dimensions required for the cell.
- Monitor for burrs align the edges of the electrodes.
- Monitor for loose metallic particles or other contaminates in coating.
- Perform specified quality samples/checks on materials produced.
- Fault analysis fault analysis on the machine.
- Identify parts of the machine and their use.
- Identify tools used when using the machine.
- Identify the necessary PPE for use of the machine.
- Identify common safety hazards associated with the machine.
- Understand the machine’s built-in safety features.
- Utilize the machine's safety features to turn it off in case of an emergency.
- Apply knowledge of the expected time and conditions for machine tasks so work is completed safely, to know when in cycles the machine requires closer observation, and when new workpieces should be staged.
- Understand using OSHA and employer-specific lockout/tag-out and energy control procedures.
- Set the machine blades to the desired positions.
- Identify any blades or other machine parts that need maintenance or replacement.
- Start the machine.
- Pause the machine mid-cycle, understanding use of electronic stops
- Shut down the machine, when needed.
- Clean up the machine following a production run.
- Monitor machine for proper operation.
- Observe machine indicator lights and gauges.
- Slit electrodes to match final dimensions required for the cell.
- Perform specified quality samples/checks on materials produced.
- Fault analysis on the machine.
- Identify parts of the machine and their use.
- Identify tools used when using the machine.
Cylindrical Cell Assembly
111
530
- Identify the necessary PPE for use of the machine.
- Identify common safety hazards associated with the machine.
- Understand the machine’s built-in safety features.
- Utilize the machine's safety features to turn it off in case of an emergency.
- Apply knowledge of the expected time and conditions for machine tasks so work is completed safely, to know when in cycles the machine requires closer observation, and when new workpieces should be staged.
- Understand using OSHA and employer-specific lockout/tag-out and energy control procedures.
- Install tape rolls in machine.
- Install current collector tab reels at the back of the machine.
- Install separators.
- Install cathode electrode.
- Install anode electrode.
- Remove the separator.
- Remove the electrode.
- Start the machine.
- Pause the machine mid-cycle, understanding use of electronic stops
- Shut down the machine, when needed.
- Clean up the machine following a production run.
- Monitor machine for proper operation.
- Observe machine indicator lights and gauges.
- Perform specified quality samples/checks on materials produced.
- Perform fault analysis on the machine.
- Identify parts of the machine and their use.
- Identify tools used when using the machine.
- Identify the necessary PPE for use of the machine.
- Identify common safety hazards associated with the machine.
- Understand the machine’s built-in safety features.
- Utilize the machine's safety features to turn it off in case of an emergency.
- Apply knowledge of the expected time and conditions for machine tasks so work is completed safely, to know when in cycles the machine requires closer observation, and when new workpieces should be staged.
- Understand using OSHA and employer-specific lockout/tag-out and energy control procedures.
- Start up the unit following protocol.
- Check the machine for any irregularities.
- Shut down the machine, when needed.
- Confirm process steps using the machine's software.
- Understand machine controls.
- Place cell in the machine.
- Align current collector tab to the outside to accommodate the machine needle.
- Confirm process steps using the machine's software.
- Align can in the machine.
- Push the current collector tab down into the can.
- Use machine software to activate the station.
- Remove completed cells from the machine.
- Visually inspect neck grooving.
- Clean up machine following production.
- Monitor machine for proper operation.
- Observe machine indicator lights and gauges.
- Perform specified quality samples/checks on materials produced.
- Fault analysis on the machine.
- Identify parts of the machine and their use.
- Identify tools used when using the machine.
- Identify the necessary PPE for use of the machine.
- Identify common safety hazards associated with the machine.
- Understand the machine’s built-in safety features.
- Utilize the machine's safety features to turn it off in case of an emergency.
- Apply knowledge of the expected time and conditions for machine tasks so work is completed safely, to know when in cycles the machine requires closer observation, and when new workpieces should be staged.
- Understand using OSHA and employer-specific lockout/tag-out and energy control procedures.
- Identify parts of the machine and their use.
- Start up the unit following protocol.
- Check the machine for any irregularities.
- Shut down the machine, when needed.
- Navigate software UI.
- Place lid on the machine.
- Place cell on the machine.
- Start production process.
- Remove cells from the machine.
- Perform visual inspection of cells.
- Reject any cells with incorrect welding.
- Monitor machine for proper operation.
- Observe machine indicator lights and gauges.
- Perform specified quality samples/checks on materials produced.
- Fault analysis on the machine.
- Identify parts of the machine and their use.
- Identify tools used when using the machine.
- Identify the necessary PPE for use of the machine.
- Identify common safety hazards associated with the machine.
- Understand the machine’s built-in safety features.
- Utilize the machine's safety features to turn it off in case of an emergency.
- Apply knowledge of the expected time and conditions for machine tasks so work is completed safely, to know when in cycles the machine requires closer observation, and when new workpieces should be staged.
- Understand using OSHA and employer-specific lockout/tag-out and energy control procedures.
- Identify the necessary PPE for use of the machine.
- Identify common safety hazards associated with the machine.
- Understand the machine’s built-in safety features.
- Utilize the machine's safety features to turn it off in case of an emergency.
- Apply knowledge of the expected time and conditions for machine tasks so work is completed safely, to know when in cycles the machine requires closer observation, and when new workpieces should be staged.
- Understand using OSHA and employer-specific lockout/tag-out and energy control procedures.
- Adjust crimp height on the machine.
- Install the electrolyte canister.
- Replace the electrolyte canister.
- Pre-weigh the empty cells.
- Fill the cell with the machine.
- Visually ensure the cell is filled.
- Place lid on the can.
- Identify parts of the machine and their use.
- Start up the unit following protocol.
- Check the machine for any irregularities.
- Shut down the machine, when needed.
- Set machine to "Crimping" setting.
- Load cell onto the machine.
- When crimping is complete, remove cell.
- Visually check crimp seal.
- Reject any damaged/incorrect cells.
- Weigh sealed cell.
- Clean out machine fill lines.
- Clean up machine following production.
- Record data from a filling/crimping run.
- Monitor machine for proper operation.
- Observe machine indicator lights and gauges.
- Perform specified quality samples/checks on materials produced.
- Fault analysis on the machine.
- Identify parts of the machine and their use.
- Identify tools used when using the machine.
- Understand operating settings and limits.
Prismatic Cell Assembly
155
530
- Identify the necessary PPE for use of the machine.
- Identify common safety hazards associated with the machine.
- Understand the machine’s built-in safety features.
- Utilize the machine's safety features to turn it off in case of an emergency.
- Apply knowledge of the expected time and conditions for machine tasks so work is completed safely, to know when in cycles the machine requires closer observation, and when new workpieces should be staged.
- Understand using OSHA and employer-specific lockout/tag-out and energy control procedures.
- Start up the unit following protocol.
- Check the machine for any irregularities.
- Ensure the machine is loaded with the necessary materials of the correct quality and quantity.
- Ensure machine is free of debris.
- Clean up machine following production.
- Splice in the new electrode reel.
- Validate machine functions.
- Understand the components used in the machine.
- Recall tools and other materials needed to run the machine.
- Monitor machine for proper operation.
- Observe machine indicator lights and gauges.
- Identify the necessary PPE for use of the machine.
- Identify common safety hazards associated with the machine.
- Understand the machine’s built-in safety features.
- Utilize the machine's safety features to turn it off in case of an emergency.
- Apply knowledge of the expected time and conditions for machine tasks so work is completed safely, to know when in cycles the machine requires closer observation, and when new workpieces should be staged.
- Understand using OSHA and employer-specific lockout/tag-out and energy control procedures.
- Start up the unit following protocol.
- Check the machine for any irregularities.
- Ensure the machine is loaded with the necessary materials of the correct quality and quantity.
- Ensure machine is free of debris.
- Clean up machine following production.
- Identify when maintenance is needed.
- Remove an empty separator reel from Z-fold stacking module
- Install a separator reel onto Z-fold stacking module.
- Install the anode tray.
- Install the cathode tray.
- Validate machine functions.
- Understand the components used in the machine.
- Recall tools and other materials needed to run the machine.
- Monitor machine for proper operation.
- Observe machine indicator lights and gauges.
- Check level of anode, cathode, and separator.
- Identify the necessary PPE for use of the machine.
- Identify common safety hazards associated with the machine.
- Understand the machine’s built-in safety features.
- Utilize the machine's safety features to turn it off in case of an emergency.
- Apply knowledge of the expected time and conditions for machine tasks so work is completed safely, to know when in cycles the machine requires closer observation, and when new workpieces should be staged.
- Understand using OSHA and employer-specific lockout/tag-out and energy control procedures.
- Determine the volume of materials to be used in the run.
- Track the materials used in inventory system.
- Record lot, reagent, and other necessary information to track run.
- Start the machine.
- Pause the machine mid-cycle, understanding use of electronic stops
- Shut down the machine, when needed.
- Clean up machine following production.
- Identify when maintenance is needed.
- Validate machine functions.
- Understand the components used in the machine.
- Recall tools and other materials needed to run the machine.
- Monitor machine for proper operation.
- Observe machine indicator lights and gauges.
- Perform specified quality samples/checks on materials produced.
- Fault analysis on the machine.
- Identify parts of the machine and their use.
- Identify tools used when using the machine.
- Understand operating settings and limits.
- Identify the necessary PPE for use of the machine.
- Identify common safety hazards associated with the machine.
- Understand the machine’s built-in safety features.
- Utilize the machine's safety features to turn it off in case of an emergency.
- Apply knowledge of the expected time and conditions for machine tasks so work is completed safely, to know when in cycles the machine requires closer observation, and when new workpieces should be staged.
- Understand using OSHA and employer-specific lockout/tag-out and energy control procedures.
- Determine the volume of materials to be used in the run.
- Track the materials used in inventory system.
- Record lot, reagent, and other necessary information to track run.
- Start the machine.
- Pause the machine mid-cycle, understanding use of electronic stops
- Shut down the machine, when needed.
- Clean up machine following production.
- Identify when maintenance is needed.
- Validate machine functions.
- Understand the reagents and components used in the machine.
- Recall tools and other materials needed to run the machine.
- Monitor machine for proper operation.
- Observe machine indicator lights and gauges.
- Perform specified quality samples/checks on materials produced.
- Fault analysis on the machine.
- Identify parts of the machine and their use.
- Identify tools used when using the machine.
- Understand operating settings and limits.
- Identify the necessary PPE for use of the machine.
- Identify common safety hazards associated with the machine.
- Understand the machine’s built-in safety features.
- Utilize the machine's safety features to turn it off in case of an emergency.
- Apply knowledge of the expected time and conditions for machine tasks so work is completed safely, to know when in cycles the machine requires closer observation, and when new workpieces should be staged.
- Understand using OSHA and employer-specific lockout/tag-out and energy control procedures.
- Determine the volume of materials to be used in the run.
- Track the materials used in inventory system.
- Record lot, reagent, and other necessary information to track run.
- Start the machine.
- Pause the machine mid-cycle, understanding use of electronic stops
- Shut down the machine, when needed.
- Clean up machine following production.
- Record electrode cutting machine data.
- Identify when maintenance is needed.
- Validate machine functions.
- Understand the components used in the machine.
- Recall tools and other materials needed to run the machine.
- Monitor machine for proper operation.
- Observe machine indicator lights and gauges.
- Perform specified quality samples/checks on materials produced.
- Fault analysis on the machine.
- Identify parts of the machine and their use.
- Identify tools used when using the machine.
- Understand operating settings and limits.
- Identify the necessary PPE for use of the machine.
- Identify common safety hazards associated with the machine.
- Understand the machine’s built-in safety features.
- Utilize the machine's safety features to turn it off in case of an emergency.
- Apply knowledge of the expected time and conditions for machine tasks so work is completed safely, to know when in cycles the machine requires closer observation, and when new workpieces should be staged.
- Understand using OSHA and employer-specific lockout/tag-out and energy control procedures.
- Start up the unit following protocol.
- Check the machine for any irregularities.
- Shut down the machine, when needed.
- Place cans into the machine.
- Begin cycle of degassing.
- Visually inspect the can for defects.
- Clean out debris.
- Record data from a degassing run.
- Monitor machine for proper operation.
- Observe machine indicator lights and gauges.
- Perform specified quality samples/checks on materials produced.
- Fault analysis on the machine.
- Identify parts of the machine and their use.
- Identify tools used when using the machine.
- Understand operating settings and limits.
- Identify the necessary PPE for use of the machine.
- Identify common safety hazards associated with the machine.
- Understand the machine’s built-in safety features.
- Utilize the machine's safety features to turn it off in case of an emergency.
- Apply knowledge of the expected time and conditions for machine tasks so work is completed safely, to know when in cycles the machine requires closer observation, and when new workpieces should be staged.
- Understand using OSHA and employer-specific lockout/tag-out and energy control procedures.
- Start up the unit following protocol.
- Check the machine for any irregularities.
- Shut down the machine, when needed.
- Verify sealing temperature has reached desired level.
- Place cans into the machine.
- Begin cycle of sealing.
- Visually inspect the can for defects.
- Clean out debris.
- Record data from a sealing run.
- Monitor machine for proper operation.
- Observe machine indicator lights and gauges.
- Perform specified quality samples/checks on materials produced.
- Fault analysis on the machine.
- Identify parts of the machine and their use.
- Identify tools used when using the machine.
- Understand operating settings and limits.
Pouch Cell Assembly
147
560
- Identify the necessary PPE for use of the machine.
- Identify common safety hazards associated with the machine.
- Understand the machine’s built-in safety features.
- Utilize the machine's safety features to turn it off in case of an emergency.
- Apply knowledge of the expected time and conditions for machine tasks so work is completed safely, to know when in cycles the machine requires closer observation, and when new workpieces should be staged.
- Understand using OSHA and employer-specific lockout/tag-out and energy control procedures.
- Start up the unit following protocol.
- Check the machine for any irregularities.
- Installing the PET film reel.
- Ensure the machine is loaded with the necessary materials of the correct quality and quantity.
- Form PET film pouches.
- Ensure machine is free of debris.
- Inspect pouches for proper dimensions and seal quality.
- Distribute output of the pouch forming unit.
- Clean up machine following production.
- Record pouch forming unit data.
- Identify when maintenance is needed.
- Validate machine functions.
- Understand the reagents and components used in the machine.
- Recall tools and other materials needed to run the machine.
- Monitor machine for proper operation.
- Observe machine indicator lights and gauges.
- Perform specified quality samples/checks on materials produced.
- Fault analysis on the machine.
- Identify parts of the machine and their use.
- Identify tools used when using the machine.
- Understand operating settings and limits.
- Identify the necessary PPE for use of the machine.
- Identify common safety hazards associated with the machine.
- Understand the machine’s built-in safety features.
- Utilize the machine's safety features to turn it off in case of an emergency.
- Apply knowledge of the expected time and conditions for machine tasks so work is completed safely, to know when in cycles the machine requires closer observation, and when new workpieces should be staged.
- Understand using OSHA and employer-specific lockout/tag-out and energy control procedures.
- Determine the volume of materials to be used in the run.
- Track the materials used in inventory system.
- Record lot, reagent, and other necessary information to track run.
- Remove the mold.
- Install the mold.
- Install the electrode.
- Splice in the new electrode reel.
- Start the machine.
- Pause the machine mid-cycle, understanding use of electronic stops
- Shut down the machine, when needed.
- Distribute output of the electrode cutting machine.
- Clean up machine following production.
- Record electrode cutting machine data.
- Identify when maintenance is needed.
- Validate machine functions.
- Ship mold for service.
- Understand the reagents and components used in the machine.
- Recall tools and other materials needed to run the machine.
- Monitor machine for proper operation.
- Observe machine indicator lights and gauges.
- Perform specified quality samples/checks on materials produced.
- Fault analysis on the machine.
- Identify parts of the machine and their use.
- Identify tools used when using the machine.
- Understand operating settings and limits.
- Identify the necessary PPE for use of the machine.
- Identify common safety hazards associated with the machine.
- Understand the machine’s built-in safety features.
- Utilize the machine's safety features to turn it off in case of an emergency.
- Apply knowledge of the expected time and conditions for machine tasks so work is completed safely, to know when in cycles the machine requires closer observation, and when new workpieces should be staged.
- Understand using OSHA and employer-specific lockout/tag-out and energy control procedures.
- Remove an empty separator reel from Z-fold stacking module.
- Install a separator reel onto Z-fold stacking module.
- Install the anode pallet tray.
- Install the cathode pallet tray.
- Install the sealing tape.
- Install the USW tape.
- Install the pouch tray.
- Start up the unit following protocol.
- Check the machine for any irregularities.
- Shut down the machine, when needed.
- Confirm process steps using the machine's software.
- Track the supplies used in a production run.
- Log which materials are used in a logbook or an electronic log.
- Verify materials, including type and amount.
- Log what materials are used.
- Check level of anode, cathode, separator, tape, tabs, and pouches.
- Utilize machine software to set up the run.
- Shut down the machine, when needed.
- Distribute the machine's output.
- Clean up machine following production.
- Record data from an ISWS machine run.
- Monitor machine for proper operation.
- Observe machine indicator lights and gauges.
- Perform specified quality samples/checks on materials produced.
- Fault analysis on the machine.
- Identify parts of the machine and their use.
- Identify tools used when using the machine.
- Understand operating settings and limits.
- Identify the necessary PPE for use of the machine.
- Identify common safety hazards associated with the machine.
- Understand the machine’s built-in safety features.
- Utilize the machine's safety features to turn it off in case of an emergency.
- Apply knowledge of the expected time and conditions for machine tasks so work is completed safely, to know when in cycles the machine requires closer observation, and when new workpieces should be staged.
- Understand using OSHA and employer-specific lockout/tag-out and energy control procedures.
- Utilize the machine UI to perform startup.
- Set sealing heat to the desired level.
- Install electrolyte canister.
- Place electrolyte canister inside cabinet.
- Use UT to inject electrolyte into pouch.
- Replace the electrolyte canister.
- Clean out fill lines.
- Start up the unit following protocol.
- Check the machine for any irregularities.
- Shut down the machine, when needed.
- Verify temperature is at the desired level.
- Place pouch into the fixture for filling/sealing.
- Visually inspect sealed pouch.
- Check for damage or leaks.
- Reject cells with damage.
- Clean up machine following production.
- Record data from a production run.
- Monitor machine for proper operation.
- Observe machine indicator lights and gauges.
- Perform specified quality samples/checks on materials produced.
- Fault analysis on the machine.
- Identify parts of the machine and their use.
- Identify tools used when using the machine.
- Understand operating settings and limits.
- Identify the necessary PPE for use of the machine.
- Identify common safety hazards associated with the machine.
- Understand the machine’s built-in safety features.
- Utilize the machine's safety features to turn it off in case of en emergency.
- Apply knowledge of the expected time and conditions for machine tasks so work is completed safely, to know when in cycles the machine requires closer observation, and when new workpieces should be staged.
- Understand using OSHA and employer-specific lockout/tag-out and energy control procedures.
- Start up the unit following protocol.
- Check the machine for any irregularities.
- Shut down the machine, when needed.
- Remove the scrap bin.
- Install the scrap bin.
- Verify sealing temperature has reached desired level.
- Place pouches into the fixture.
- Begin cycle of degassing, trimming, and vacuum heat sealing.
- Visually inspect the pouch to ensure it is trimmed and resealed.4
- Clean out debris.
- Remove and empty scrap bin.
- Record data from a degassing/sealing run.
- Monitor machine for proper operation.
- Observe machine indicator lights and gauges.
- Perform specified quality samples/checks on materials produced.
- Fault analysis on the machine.
- Identify parts of the machine and their use.
- Identify tools used when using the machine.
- Understand operating settings and limits.
Battery Formation
17
180
- Identify the necessary PPE for use of the machine.
- Identify common safety hazards associated with the machine.
- Understand the machine’s built-in safety features.
- Utilize the machine's safety features to turn it off in case of an emergency.
- Apply knowledge of the expected time and conditions for machine tasks so work is completed safely, to know when in cycles the machine requires closer observation, and when new workpieces should be staged.
- Understand using OSHA and employer-specific lockout/tag-out and energy control procedures.
- Monitor machine for proper operation.
- Observe machine indicator lights and gauges.
- Clean up machine following production.
- Record data from a production run.
- Monitor machine for proper operation.
- Observe machine indicator lights and gauges.
- Perform specified quality samples/checks on materials
- Fault analysis on the machine.
- Identify parts of the machine and their use.
- Identify tools used when using the machine.
- Understand operating settings and limits.
Related Instruction Content
Training Provider(s):
Battery Industry Introduction
4
State what a battery is and identify parts of a battery Recall different types of batteries and their applications. Identify common industry career pathways.
Battery Production Overview
4
Identify each stage of battery production and its importance to the overall process, including inputs and outputs for each stage. Utilize PPE in a proper manner and follow all safety guidelines. Recall specific applications of this process and the products created.
Safety in Battery Manufacturing
32
Identify safety best practices for each stage of battery production. Utilize PPE in a proper manner and follow all safety guidelines. Apply safety response guidelines while working in a battery manufacturing environment. Chemical safety and hazard identification Moving and handling chemicals Working with nano particles Lockout tagout Working safely with automation High-voltage safety Battery formation and off-gassing Battery testing safety Working in a dry room safely When to leave the work area
Mixing: Manufacturing Cathodes I
3
Identify the chemicals used in the cathode mixing process. Follow the procedure to create slurry based on a given mixing recipe. Perform quality checks on the mixture for adherence to parameters for viscosity and acidity.
Mixing: Manufacturing Lithium Anodes I
3
Identify the chemicals used in the anode manufacturing process. Follow the procedure for creating anodes based on a given process. Perform checks on the process and anodes adherence to quality parameters.
Electrode Prep: Coating I
3
Identify the parts of the coating machine and their purpose in the battery production process. Follow the procedure for operating the machine, including loading materials, monitoring production, and adjusting die settings. Perform basic fault analysis of the coating machine.
Electrode Prep: Drying I
3
Identify the parts of the drying machine and their purpose in the battery production process. Follow the procedure for operating the machine, including loading and unloading materials and monitoring production. Perform basic fault analysis of the drying machine.
Electrode Prep: Calendaring I
3
Identify the parts of the calendaring machine and their purpose in the battery production process. Set depth of calendaring based on protocol. Perform basic fault analysis of the calendaring machine.
Electrode Prep: Slitting I
3
Identify the parts of the slitting machine and their purpose in the battery production process. Follow the procedure for operating the slitter, including setting the widths of the cut by moving the blades. Identify the need for blade maintenance or replacement.
Cylindrical Cell Assembly: Winding I
7
Identify the parts of the winding machine and their purpose in the cylindrical cell production process. Set up the winding machine based on a given protocol. Utilize machine software to make adjustments during the winding process. Monitor the winding process in order to identify the need for machine cleaning or maintenance.
Cylindrical Cell Assembly: Deep Can Welding, Necking, & Laser Welding I
7
Identify the parts of the welding and necking units and their purpose in the cylindrical cell production process. Set up the welding and necking units based on given protocol. Utilize machine software to make adjustments during the welding and necking processes. Monitor the welding and necking processes in order to identify the need for machine cleaning or maintenance.
Cylindrical Cell Assembly: E-Fill & Crimping I
7
Identify the parts of the electrolyte fill and crimping machines and their purpose in the cylindrical cell production process. Set up the electrolyte fill and crimping machines based on given protocol. Utilize machine software to make adjustments during the electrolyte fill and crimping processes. Monitor the electrolyte fill and crimping processes in order to identify the need for machine cleaning or maintenance.
Prismatic Cell Assembly: Notching & Stacking I
7
Identify the parts of the notching and stacking units and their purpose in the prismatic cell production process. Set up the notching and stacking units based on given protocol. Utilize machine software to make adjustments during the notching and stacking processes. Monitor the notching and stacking processes in order to identify the need for machine cleaning or maintenance.
Prismatic Cell Assembly: Welding & Can Assembly I
7
Identify the parts of the welding and can assembly units and their purpose in the prismatic cell production process. Set up welding and can assembly units based on given protocol. Utilize machine software to make adjustments during the welding and can assembly processes. Monitor the welding and can assembly processes in order to identify the need for machine cleaning or maintenance.
Prismatic Cell Assembly: E-Fill, Cap Assembly, Degassing, & Sealing I
7
Identify the parts of the electrolyte fill, cap assembly, degassing, and sealing machines and their purpose in the prismatic cell production process. Set up the electrolyte fill, cap assembly, degassing, and sealing machines based on given protocol. Utilize machine software to make adjustments during the electrolyte fill, cap assembly, degassing, and sealing processes. Monitor the electrolyte fill, cap assembly, degassing, and sealing processes in order to identify the need for machine cleaning or maintenance.
Pouch Cell Assembly: Pouch Forming & Electrode Cutting I
7
Identify the parts of the pouch forming and electrode cutting machines and their purpose in the pouch cell production process. Set up the pouch forming and electrode cutting machines based on given protocol. Utilize machine software to make adjustments during the pouch forming and electrode cutting processes. Monitor the pouch forming and electrode cutting processes in order to identify the need for machine cleaning or maintenance.
Pouch Cell Assembly: Stacking & Welding I
7
Identify the parts of the stacking and welding units and their purpose in the pouch cell production process. Set up the stacking and welding units based on given protocol. Utilize machine software to make adjustments during the stacking and welding processes. Monitor the stacking and welding processes in order to identify the need for machine cleaning or maintenance.
Pouch Cell Assembly: E-Fill, Degassing, & Sealing I
7
Identify the parts of the electrolyte fill, degassing, and sealing machines and their purpose in the pouch cell production process. Set up the electrolyte fill, degassing, and sealing machines based on given protocol. Utilize machine software to make adjustments during the electrolyte fill, degassing, and sealing processes. Monitor the electrolyte fill, degassing, and sealing processes in order to identify the need for machine cleaning or maintenance.
Battery Formation, Aging, & Testing I
3
Perform charge and discharge cycles on completed battery cells. Monitor SEI level formed on electrodes. Conduct quality tests of cell during and after the aging process.
Mixing: Manufacturing Cathodes II
5
Ensure the quality of mixer parts, identifying the need for any replacement before the production run. State the operating limits and ideal settings for the machine. Apply knowledge of the expected time and conditions for the process to ensure safety and efficiency. Read work orders to determine production specifications or information. Direct all machine setup and production tasks, including ensuring proper machine function and correct mixing materials. Fault analysis during the cathode mixing process.
Mixing: Manufacturing Lithium Anodes II
5
Ensure the quality of machine parts, identifying the need for any replacement before the production run. State the operating limits and ideal settings for the machine. Apply knowledge of the expected time and conditions for the process to ensure safety and efficiency. Read work orders to determine production specifications or information. Direct all machine setup and production tasks, including ensuring proper machine function and correct mixing materials. Fault analysis during the anode mixing process.
Electrode Prep: Coating II
5
Apply knowledge of the expected time and conditions for the process to ensure safety and efficiency. Apply OSHA and employer-specific lock-out/tag-out procedures. Ensure HMI and other monitoring parts are functioning correctly. Manually adjust dies by hand in response to HMI data. Direct all machine setup and production tasks, including ensuring proper machine function. Fault analysis during the coating process.
Electrode Prep: Drying II
5
Apply knowledge of the expected time and conditions for the process to ensure safety and efficiency. Apply OSHA and employer-specific lock-out/tag-out procedures. Ensure machine parts are functioning correctly. Perform all machine tasks, including shutting down the machine, when needed. Direct all machine setup and production tasks, including ensuring proper machine function. fault analysis during the drying process.
Electrode Prep: Calendaring II
5
Apply knowledge of the expected time and conditions for the process to ensure safety and efficiency. Apply OSHA and employer-specific lock-out/tag-out procedures. Ensure machine parts are functioning correctly. Identify any machine parts that need maintenance or replacement. Set the depth of the calendaring tool, making adjustments based on production results where needed. Direct all machine setup and production tasks, including ensuring proper machine function. Fault analysis during the calendaring process.
Electrode Prep: Slitting II
5
Apply knowledge of the expected time and conditions for the process to ensure safety and efficiency. Apply OSHA and employer-specific lock-out/tag-out procedures. Ensure machine parts are functioning correctly. Set the machine blades to the desired positions. Identify any blades or other machine parts that need maintenance or replacement. Direct all machine setup and production tasks, including ensuring proper machine function. Fault analysis during the slitting process.
Cylindrical Cell Assembly: Winding II
13
Apply knowledge of the expected time and conditions for the process to ensure safety and efficiency. Apply OSHA and employer-specific lock-out/tag-out procedures. Ensure machine parts are functioning correctly. Direct all machine setup and production tasks, including ensuring proper machine function. Fault analysis during the winding process.
Cylindrical Cell Assembly: Deep Can Welding, Necking, & Laser Welding II
13
Apply knowledge of the expected time and conditions for the process to ensure safety and efficiency. Apply OSHA and employer-specific lock-out/tag-out procedures. Ensure machine parts are functioning correctly. Direct all machine setup and production tasks, including ensuring proper machine function. Fault analysis during the necking and welding processes.
Cylindrical Cell Assembly: E-Fill & Crimping II
13
Apply knowledge of the expected time and conditions for the process to ensure safety and efficiency. Apply OSHA and employer-specific lock-out/tag-out procedures. Ensure machine parts are functioning correctly. Direct all machine setup and production tasks, including ensuring proper machine function. Fault analysis during the electrolyte fill and crimping processes.
Prismatic Cell Assembly: Notching & Stacking II
13
Apply knowledge of the expected time and conditions for the process to ensure safety and efficiency. Apply OSHA and employer-specific lock-out/tag-out procedures. Ensure machine parts are functioning correctly. Validate machine functions. Confirm all components used in the machine. Direct all machine setup and production tasks, including ensuring proper machine function. Fault analysis during the notching and stacking processes.
Prismatic Cell Assembly: Welding & Can Assembly II
13
Apply knowledge of the expected time and conditions for the process to ensure safety and efficiency. Apply OSHA and employer-specific lock-out/tag-out procedures. Ensure machine parts are functioning correctly. Validate machine functions. Confirm all components used in the machine. Recall tools and other materials needed to run the machine. Direct all machine setup and production tasks, including ensuring proper machine function. Fault analysis during the welding and can assembly processes.
Prismatic Cell Assembly: E-Fill, Cap Assembly, Degassing, & Sealing II
13
Apply knowledge of the expected time and conditions for the process to ensure safety and efficiency. Apply OSHA and employer-specific lock-out/tag-out procedures. Ensure machine parts are functioning correctly. Validate machine functions. Confirm the reagents and components used in the machine. Recall tools and other materials needed to run the machine. Direct all machine setup and production tasks, including ensuring proper machine function. Fault analysis during the electrolyte fill, cap assembly, degassing, and sealing processes.
Pouch Cell Assembly: Pouch Forming & Electrode Cutting II
13
Apply knowledge of the expected time and conditions for the process to ensure safety and efficiency. Apply OSHA and employer-specific lock-out/tag-out procedures. Ensure machine parts are functioning correctly. Identify when pouch forming mold needs service. Confirm the reagents and components used in the machine. Recall tools and other materials needed to run the machine. Direct all machine setup and production tasks, including ensuring proper machine function. Fault analysis during the pouch forming and electrode cutting processes.
Pouch Cell Assembly: Stacking & Welding II
13
Apply knowledge of the expected time and conditions for the process to ensure safety and efficiency. Apply OSHA and employer-specific lock-out/tag-out procedures. Ensure machine parts are functioning correctly. Confirm the reagents and components used in the machine. Recall tools and other materials needed to run the machine. Direct all machine setup and production tasks, including ensuring proper machine function. Fault analysis during the stacking and welding processes.
Pouch Cell Assembly: E-Fill, Degassing, & Sealing II
13
Apply knowledge of the expected time and conditions for the process to ensure safety and efficiency. Apply OSHA and employer-specific lock-out/tag-out procedures. Ensure machine parts are functioning correctly. Confirm the reagents and components used in the machine. Recall tools and other materials needed to run the machine. Clean out fill lines when needed. Direct all machine setup and production tasks, including ensuring proper machine function. Fault analysis during the electrolyte fill, degassing, and sealing processes.
Battery Formation, Aging, & Testing II
5
Apply knowledge of the expected time and conditions for the process to ensure safety and efficiency. Apply OSHA and employer-specific lock-out/tag-out procedures. Ensure machine parts are functioning correctly. Confirm the components used in the machine. Recall tools and other materials needed to run the machine. Direct all machine setup and production tasks, including ensuring proper machine function. Assess testing results and make machine adjustments accordingly. Fault analysis during the formation and aging processes.
Professional Communication
2
Practice effective communication strategies in a battery production environment. Ask clarifying questions when necessary. Use three-part communication to effectively communicate with supervisors and peers.
Problem Solving & Critical Thinking
2
Define the problem-solving process. Describe problem-solving skills, including the importance of time management. Discuss problem-solving and critical thinking best practices.
Positive Workplace Culture
2
Describe the difference between growth and fixed mindset. Identify best practices to adopt a positive mental attitude (PMA) in the workplace. Discuss concepts of cultural competence and respect in workplace scenarios.
Conflict Resolution
2
Explain pros and cons of conflict. Describe causes of conflict in a manufacturing environment. Use effective strategies to resolve conflicts.
Professional Goal Setting
2
Describe the benefits of setting and achieving goals. Discuss barriers in goal setting. Create a detailed long-term goal, short-term goals, and action steps. Use goal setting worksheet to think through goals strategically.
Resumes & Cover Letters
3
Define the purpose of a resume and discuss how employers use resumes in the hiring process. Create a resume and cover letter targeting jobs in battery production. Identify resume writing best practices and common resume writing errors to avoid. Identify cover letter writing best practices and common errors to avoid.
Interviewing
3
State best practices for interviewing for battery production machine operator positions. Identify ways to send positive signals and encourage employers to make positive assumptions during an interview. Use the STAR strategy to answer difficult behavior-based interview questions.
Job Retention Strategies
2
Identify and evaluate on-the-job behaviors and strategies that support job retention. Understand the importance of job retention for the employee and the employer. Understand codes of conduct and employer expectations. Identify strategies for long-term professional success.