Apprentices progress at their own pace – they demonstrate
competency in skills and knowledge through assessment tests,
but are not required to complete a specific number of hours.
competency in skills and knowledge through assessment tests,
but are not required to complete a specific number of hours.
Optics Manufacturing Technician
Anonymous
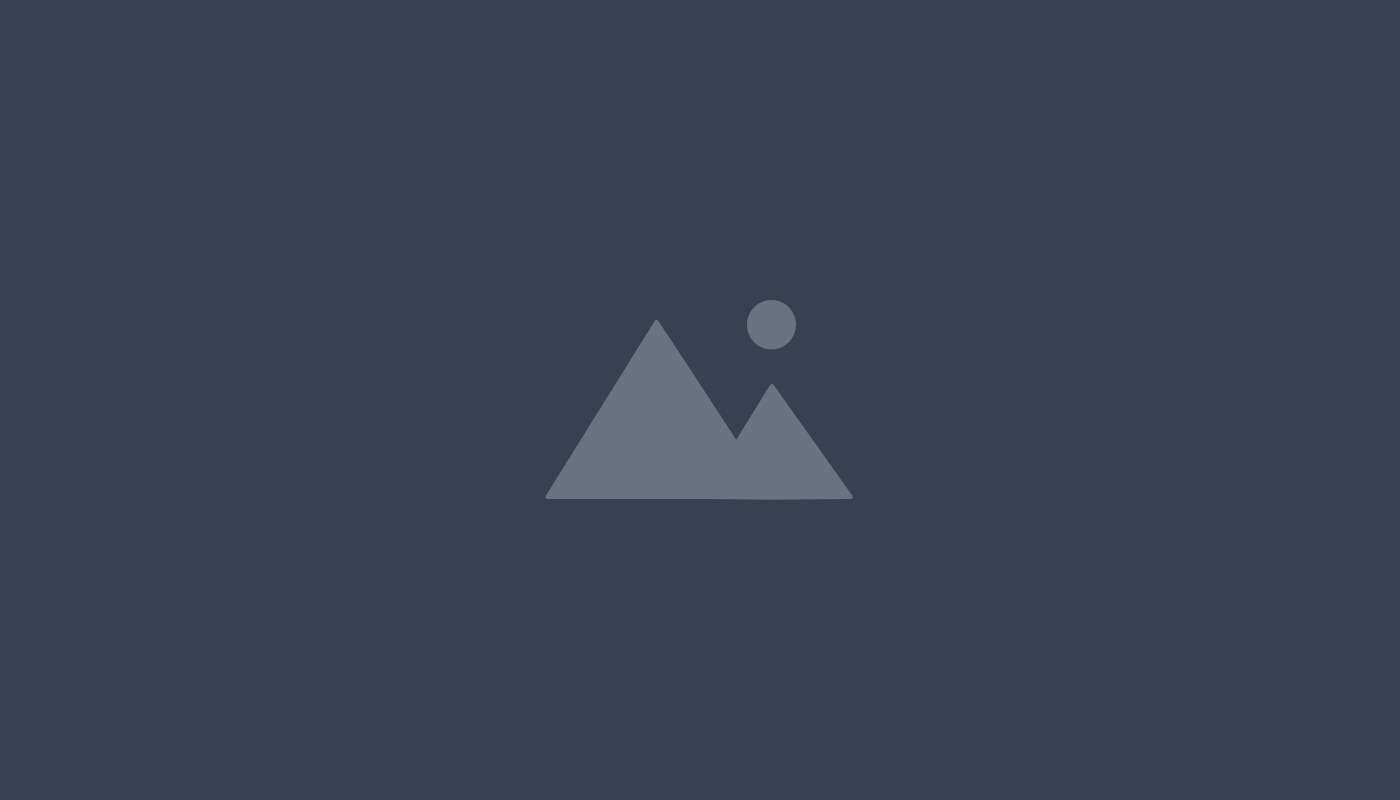
Colorado (OA)
Work Process Content
On the Job Training
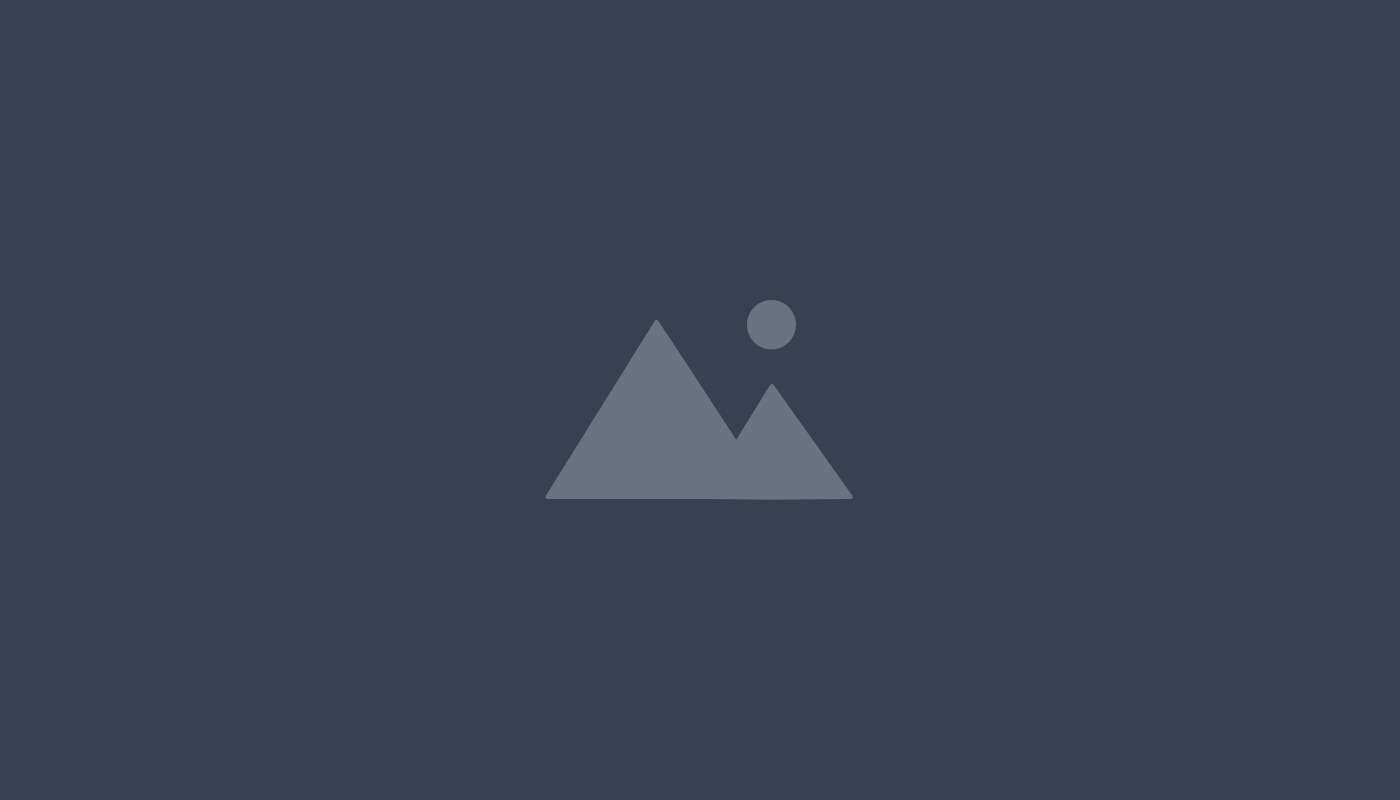
Anonymous
105
Skills
Workplace Safety
4
Workplace Safety
4
- Identify hazards associated with the workplace and record and report in accordance with organizational procedure.
- Understand all workplace safety requirements at all times.
- Understand and maintain all organizational security arrangements and approved procedures.
- Understand and comply with all emergency procedures in accordance with organizational policy.
Critical Work Function 1: Identify, inspect, and qualify materials for manufacturing optical components.
11
Critical Work Function 1: Identify, inspect, and qualify materials for manufacturing optical components.
11
- A. Determine material requirements as defined by blueprint specifications.
- A1. Evaluate physical property of materials for hardness, cleavage, fracturing and chemical stability and assess their relevance to specified manufacturing process.
- A2. Determine optical, chemical, thermal and mechanical properties of selected materials from handbooks, supplier specification sheets, and Internet sources, and assess their relevance to specified manufacturing processes.
- B. Inspect and accurately evaluate material certification sheets to match print specifications.
- B1. Use quality assurance criteria to determine deficiencies in materials and optics using established design specifications.
- B2. Use a loupe to identify bulk material defects such as inclusions, bubbles, striae, and fractures.
- C. Ensure physical safety in handling hazardous materials by marking material containers with appropriate material safety data sheet (MSDS) identifications.
- C1. Identify physical and environmental hazards associated with various optical materials and the solvents used to process them.
- D. Follow material handling procedures to ensure physical safety, avoid contamination, and maintain material inventory and identification.
- D1. Apply chemical safety procedures to chosen optical materials and solvents.
- E. Maintain prescribed documentation of bulk materials using a job jacket or its equivalent.
Critical Work Function 2: Participate in the planning and verification of optical fabrication processes.
17
Critical Work Function 2: Participate in the planning and verification of optical fabrication processes.
17
- A. Use design specifications, technical drawings, and/or government documentation to meet specifications and tolerances.
- A1. Read and interpret technical drawings and specifications.
- A2. Understand and use basic mathematical concepts to include fractions, decimals, ratio, proportion, powers and algebra principles.
- A3. Use and convert metric and English units, and use of scientific notation.
- A4. Use of angle measurements in degrees, radians, minutes, and seconds.
- A5. Apply procedures of geometry and trigonometry to optics.
- A6. Use hand calculators and computers proficiently.
- B. Use basic processing techniques for producing plano, cylindrical, spherical, and aspheric optics.
- B1. Prepare fixtures for mounting starting material as part of the fabrication process.
- B2. Determine the interaction between various material used in high tolerance optics fabrication such as hot pitch and acetone.
- B3. Prepare bevels necessary for suitable optical mounting.
- C. Assist and advise in the selection of fabrication processes and their sequencing.
- C1. Accurately identify the shapes of various optical components and their use in an optical assembly/system.
- D. Recommend process changes to increase quality, improve efficiency, and reduce production costs.
- D1. Use basic cost estimation techniques to determine cost vs benefit factors. D2. Incorporate basic project management strategies in developing production plans.
- E. Identify standard operating and safety procedures of the optics shop and equipment required in the process.
- F. Document process changes and non‐conformances and may identify preventative and corrective actions to improve process control.
Critical Work Function 3: Shape and finish bulk materials to generate optical components.
11
Critical Work Function 3: Shape and finish bulk materials to generate optical components.
11
- A. Determine and perform procedures for measuring, tooling, blocking, generating, shaping, beveling, grinding, polishing, and centering.
- A1. Operate common machine shop equipment for metals such as lathes, band saws, drill presses, and milling machines.
- A2. Operate equipment (e.g., cut‐off and wire saw, abrasive grinding machines, and coring machines) to shape optical materials to specifications.
- A3. Perform basic CNC controller programming functions according to specifications and assess their performance against established specifications.
- A4. Operate grinding and polishing machines to generate plano, spherical, aspherical, cylindrical, and toric optics.
- B. Practice accepted procedure for handling optical materials.
- C. Apply appropriate procedures for processing a variety of optical materials such as glass, crystals, optical ceramics, and plastics.
- C1. Select appropriate abrasives including grit size and composition to achieve design tolerances and specifications for specific materials.
- D. Measure and accurately record dimensionality to ensure adherence to specifications and tolerances.
- D1. Inspect finished optical components to ensure compliance with established specifications.
- E. Properly clean, store, secure, document, package, and transport the finished optical components to ensure their integrity and proper identification.
Critical Work Function 4: Operate, maintain, and calibrate optics manufacturing and testing equipment
10
Critical Work Function 4: Operate, maintain, and calibrate optics manufacturing and testing equipment
10
- A. Use proper procedures to operate all machinery from hand beveling wheels to CNC machines.
- A1. Maintain and prepare pumps and conduits to properly deliver slurry and coolant to work surfaces.
- A2. Use appropriate hand tools (e.g., calipers, micrometers, depth gauges, spherometers) during fabrication and inspection of optical components.
- A3. Optimize fabrication tools and parameters to increase efficiency and quality.
- B. Apply accepted standards to maintain work area cleanliness.
- C. Inspect and maintain equipment, per prescribed schedules, to ensure optimal use and productivity and document these efforts.
- C1. Apply appropriate maintenance instructions from manufacturer’s equipment manuals.
- D. Use the work instruction template to verify set points in the control screens.
- E. Detect malfunctioning equipment and adjust or repair as necessary and/or notify appropriate work personnel.
- F. Identify health hazards associated with specific material and process and use accepted practices to ensure health of self, others, and the environment.
Critical Work Function 5: Conduct optical metrology measurements and inspections for in process work and final distribution.
22
Critical Work Function 5: Conduct optical metrology measurements and inspections for in process work and final distribution.
22
- A. Coordinate with quality assurance to ensure compliance to design specifications and documentation requirements.
- A1. Use quality assurance criteria to determine deficiencies in materials and optics using established design specifications.
- B. Participate in the development of inspection plans that use the appropriate metrology for all measured specifications.
- C. Test finished components by appropriate means including test place or interferometric techniques to ensure compliance with design specifications.
- C1. Measure deviations from specifications in dimensionality and surface quality and roughness.
- C2. Inspect materials using birefringence testing via polarimeters and index of refraction testing.
- C3. Measure and analyze homogeneity of materials using interferometry techniques.
- C4. Use polarization measurement techniques to identify internal stress.
- D. Use autocollimators to measure angular error, pyramid error, beam deviation, and dimensional deviations for both in‐process and finished products.
- E. Use collimator or interferometer to measure focal length and on‐axis aberrations.
- F. Inspect surface quality of finished product to comply with appropriate scratch‐and‐dig standards as specified on the component drawing or specification sheet.
- G. Measure surface roughness using white light interferometry or other optical means.
- G1. Measure surface roughness with appropriate equipment (e.g., white light interferometer, laser surface profiler).
- H. Measure the processed surfaces or components using appropriate equipment (e.g., profilometer, optical comparator, coordinate measuring device, micrometer, or drop gage.
- H1. Measure surface quality using appropriate equipment (e.g., scratch‐and‐dig inspection box, microscope, loupe, and magnifiers.
- H2. Measure shapes using appropriate equipment (e.g., profilometers or coordinate measuring devices), and determine deviations from specifications in dimensionality.
- H3. Measures angular errors with appropriate equipment (e.g., autocollimators or interferometers).
- I. Determine and select, using written instructions and specifications, appropriate packaging for protecting, storing and shipping optics.
- I1. Evaluate shipping conditions for finished optics to determine appropriate packaging.
- J. Document final inspection results according to instructions, procedures, and/or specifications to close‐out job jacket or equivalent.
- K. Maintain NIST certified calibration standards and samples, be able to calibrate all optical instruments per proper procedures and maintain a calibration log.
- L. Use statistical process control guidelines for sampling finished components.
Critical Work Function 6: Assemble optical components and systems (e.g., cemented and air-spaced doublets and triplets)
18
Critical Work Function 6: Assemble optical components and systems (e.g., cemented and air-spaced doublets and triplets)
18
- A. Interpret assembly drawings.
- B. Use proper cleanroom and air‐flow workbench procedures. B4. Monitor air flow filtration, room pressure, air velocities, temperature and relative humidity of clean rooms.
- B1. Use established procedures for personnel gowning for clean room operations, including booties and beards.
- B2. Use proper procedures for entering and exiting air locks and door locks in a clean room facility.
- B3. Interpret clean room Class Ratings required in optics fabrication (e.g., Class 100, 1000, and 10,000).
- B4. Monitor air flow filtration, room pressure, air velocities, temperature and relative humidity of clean rooms.
- C. Use proper alignment techniques for assembly process.
- D. Select and/or use appropriate or required optical adhesives or epoxies.
- D1. Use proper procedures in mixing, degassing, applying, and establishing cure times for adhesives and epoxies.
- E. Mount optical components in mechanical assemblies using prescribed methods.
- F. Align elements in cells.
- F1. Align physical and optical centers following specifications.
- G. Measure conformance and performance of optical assembly via mechanical and/or optical means. Determine root cause of any non‐conforming assemblies.
- G1. Measure optical properties using appropriate equipment (e.g., autocollimators).
- G2. Inspect finished products following accepted procedures to ensure compliance with established specifications.
- H. Clean, prepare and inspect optical surfaces prior to assembly per requirements.
- H1. Clean optics to specifications using proper techniques.
- H2. Store optics in appropriate container with environmental controls
Critical Work Function 7: Apply anti‐reflectance coatings to optical components.
12
Critical Work Function 7: Apply anti‐reflectance coatings to optical components.
12
- A. Interpret drawing for coating specifications.
- A1. Identify the function of anti/reflection and protective thin film coatings on optical surfaces.
- A2. Interpret drawings for coating specifications to determine proper coating materials.
- B. Clean and inspect optics for coating using accepted procedures.
- B1. Prepare optics for thin film coatings by cleaning optical surfaces requiring a coating.
- C. Load and properly operate coating equipment to apply thin film coatings using prescribed procedures.
- C1. Select appropriate coating procedures and operate coating equipment.
- C2. Use fixtures for mounting optics in coating chambers.
- C3. Operate vacuum systems used for coating optics.
- C4. Use proper sensors to monitor film properties during coating processes.
- D. Operate spectrometer to test coating performance on witness samples and verify results with drawing specifications.
- D1. Operate spectrometer to test coatings on witness sample.
Related Instruction Content
Training Provider(s):
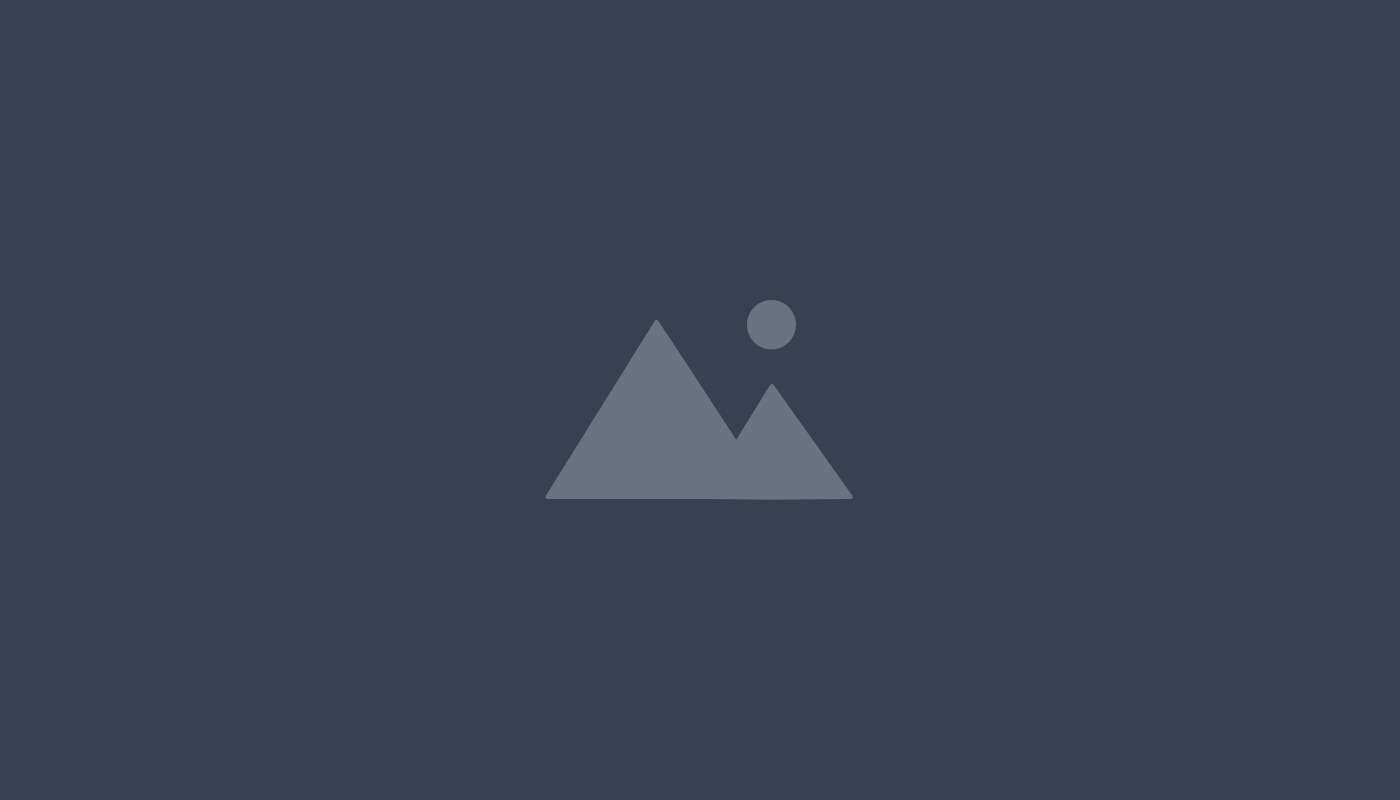
Front Range Community College
550
RI hours
Quality Assurance of Precision Optics
68
Quality Assurance of Precision Optics
68
Lab Operations
68
Lab Operations
68
Technical Mathematics
60
Technical Mathematics
60
Introduction to PC Application
40
Introduction to PC Application
40
Fabrication of Precision Optics
90
Fabrication of Precision Optics
90
Advanced Fabrication of Precision Optics
90
Advanced Fabrication of Precision Optics
90
Introduction to Manufacturing Technologies
68
Introduction to Manufacturing Technologies
68
Metrology of Optical Systems
68
Metrology of Optical Systems
68
Similar Programs
Precision Optics Manufacturing Technician
Time
•
51-2099.00
Fiber Optic Technician (2064CBV1) Competency-Based
Competency
•
49-2021.00
OPTICAL DISPENSER
Competency
•
29-2081.00
F.O.N.D (Fiber Optics Network & Data) Technician
Hybrid
•
49-9052.00
IT Lab Technician (Optical/Electrical Diagnostics)
Competency
•
17-3023.01