using a minimum and maximum range of hours for each major job
function and the successful demonstration of identified competencies.
Composite Technician
National Advanced Manufacturing Partnership (NAMAP)
Work Process Content
On the Job Training
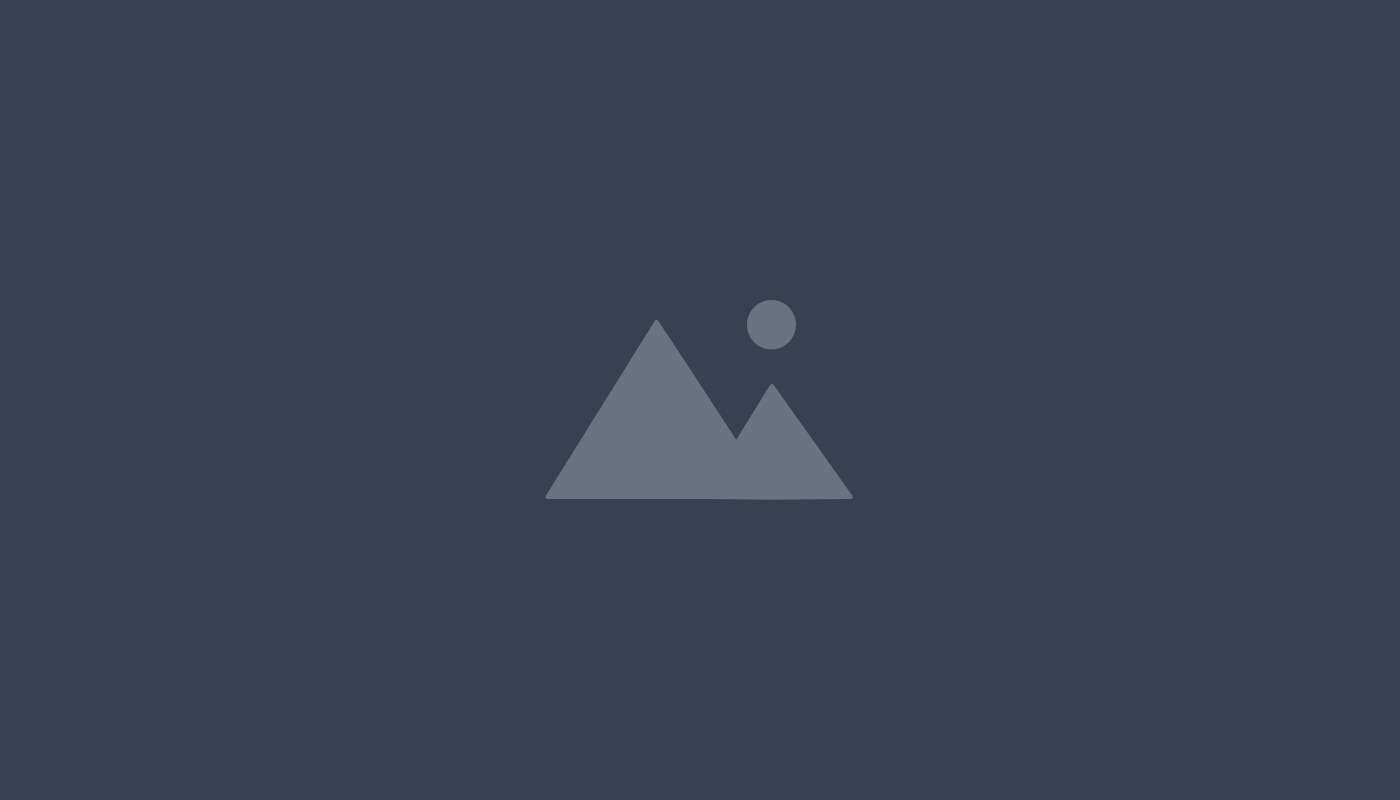
Safety Compliance
10
40
- Demonstrate the ability to adhere to personal grooming and personal protective equipment requirements in the facility.
- Demonstrate the safe use of hand and power tools.
- Demonstrate the correct way to clean machines and floor area.
- Demonstrate the proper use of cleaning materials and fluids.
- Demonstrate OSHA lifting techniques.
- Identify all pinch points on primary and supportive machine tools and the proper placements of guards.
- Demonstrate both emergency and standard shut down of all required equipment.
- Demonstrate the proper use of a fire extinguisher.
- Demonstrate a working knowledge of the hazards associated with handling and machining of advanced composite materials, as well as the hazards associated with the exposure and storage of the materials.
- Demonstrate a working knowledge of lightning strike protection.
Matrix and Fiber Technologies
3
200
- Demonstrate the ability to mix resins, adhesives and potting compounds.
- Demonstrate a working knowledge of best practices for reinforcement of weave patterns.
- Demonstrate the ability to select necessary reinforcements and fabric weaves.
Handling Hazardous Materials
3
16
- Demonstrate the ability to handle and store hazardous materials as assigned, while adhering to safe practices in accordance with Occupational Safety and Health Administration (OSHA) and Environmental Protection Agency (EPA) requirements and guidelines, including completing the required documentation.
- Demonstrate how to identify and recognize hazardous situations and apply proper procedures (includes following guidelines to prevent spread of blood borne pathogens and spill control).
- Demonstrate how to locate a material Safety Data Sheet (SDS) and describe how you interpret the information.
Core Materials
3
200
- Demonstrate a working knowledge of sandwich fabrication.
- Demonstrate a working knowledge of vacuum bagging techniques.
- Demonstrate a working knowledge of co-cure and co-bonding of skins on core materials (honeycomb, polymeric etc.).
Molding Methods and Practices for Advanced Composites
11
400
- Demonstrate the ability to cut prepreg material.
- Demonstrate a working knowledge of the fundamentals of vacuum bag debulks.
- Demonstrate the ability to check for vacuum leaks to control quality.
- Demonstrate the ability to calculate out time, working life and shelf life best practices.
- Demonstrate the ability to use scale and taring.
- Demonstrate a working knowledge of resin mix ratios and best practices for mixing resins.
- Demonstrate a working knowledge of pot life and storage life.
- Demonstrate a working knowledge of best practices for fiber wet-out.
- Demonstrate the ability to compare fabric types.
- Demonstrate a working knowledge of ovens, vacuum bagging and autoclaves.
- Demonstrate a working knowledge of potting compounds and their uses.
Shop Practices
9
40
- Demonstrate the ability to know the jobs assigned to you.
- Demonstrate a working knowledge of the company policy manual.
- Demonstrate a dedication to the trade and to the quality and professional standards set forth by the company.
- Demonstrate an ability to show up on time every day with a desire to work hard and add value to the company.
- Demonstrate the ability to follow instructions laid out by your supervisor.
- Demonstrate the ability to maintain safe work habits in the exhibition of both one's personal responsibility for safety practices and displaying a continuous consideration of safety practices in the protection of one's fellow worker.
- Demonstrate the ability to maintain a clean orderly and safe work area.
- Identify the steps involved in 5S.
- Demonstrate how to perform a preventive maintenance procedure for a given machine to extend machine life and minimize downtime in accordance with company-approved maintenance specifications and overall program goals.
Shop Mathematics
6
80
- Demonstrate how to convert fractions to decimals form.
- Demonstrate how to convert dimensions to metric equivalent.
- Demonstrate how to calculate a missing angle from a triangle.
- Demonstrate how to solve missing measurements in right angles.
- Demonstrate how to calculate the area of a circle.
- Demonstrate how to solve for the unknown hypotenuse of a right triangle using the Pythagorean Theorem.
Blueprint Reading
4
100
- Demonstrate the ability to identify symbols, notations, and lines to industry standards.
- Demonstrate the ability to determine dimensions, critical features and tolerances on machine drawing.
- Demonstrate the ability to interpret pictorial drawings to industry standards.
- Demonstrate the ability to interpret multi-view drawings to industry standard.
Design Considerations
5
200
- Demonstrate the ability to use process modeling, design software and specification tools.
- Demonstrate a working knowledge of hand lay-up best practices.
- Demonstrate a working knowledge of balanced laminate.
- Demonstrate a working knowledge of residual stress.
- Demonstrate the knowledge of composite industry history and the development of advanced composites.
Metrology
8
300
- Demonstrate the ability to interpret part drawing specifications through working with blueprints (dimensions, layout, material, surface finish, countersinks, tolerances, threading, etc.).
- Demonstrate the use of a steel rule.
- Demonstrate the use of ID and OD micrometers.
- Demonstrate the use of a height gauge.
- Demonstrate the use of a vernier/dial caliper.
- Demonstrate the use of a measuring scale.
- Demonstrate the use of a radius gage.
- Demonstrate the use of a tape measure.
Inspection and Testing
2
100
- Demonstrate the ability to detect and rate damaged and defective parts
- Demonstrate the ability to complete and record non-destructive inspection (NDI)
Measuring and Improving Work
1
50
- Demonstrate the ability to identify a production problem, propose a remedy, having been given the authorization to implement the process improvement and carry it out.
Problem Solving
4
150
- Demonstrate the tracing of defects to the originating section of their root cause.
- Demonstrate the use of cause mapping when performing Root Cause Analysis.
- Demonstrate the ability to perform daily, weekly and monthly preventive maintenance responsibilities.
- Demonstrate the ability to conduct a triage level of troubleshooting and communicate findings to maintenance technician.
Manual Operations Tools and Techniques
11
160
- Demonstrate the safe and proper use of a bench vise.
- Demonstrate the safe and proper use of a ball-peened hammer.
- Demonstrate the safe and proper use of a soft-faced hammer.
- Demonstrate the safe and proper use of a standard screwdriver.
- Demonstrate the safe and proper use of a phillips screwdriver.
- Demonstrate the safe and proper use of an offset screwdriver.
- Demonstrate the safe and proper use of a hand hacksaw.
- Demonstrate the safe and proper use of a machinist's file.
- Demonstrate the safe and proper use of precision files.
- Demonstrate the safe and proper use of a combination square set.
- Demonstrate the safe and proper use of a vernier height gauge.
Composites
28
1.9K
- Demonstrate how to locate the SDS for all composite chemicals and review their potential hazards.
- Demonstrate consistent adherence to all personal protective equipment (PPE) practices relevant for a composite repair technician while working in the field.
- Demonstrate the ability to identify and select the proper materials for processing.
- Demonstrate the ability to properly store material, determine its shelf life and properly dispose of outdated material.
- Demonstrate the ability to design and prepare mold tools.
- Demonstrate the ability to mix wet resins at the proper mix ratios.
- Demonstrate the ability to prepare surfaces for co-bonding and join the surfaces following correct procedures.
- Demonstrate a working knowledge of composite-composite and composite-metallic adhesive bonding and mechanical fastening
- Demonstrate the ability to verify that the surfaces have cured and are properly joined.
- Demonstrate the ability to gather all relevant equipment and materials for hot bonding.
- Demonstrate the ability to operate the equipment to bond surfaces together.
- Demonstrate the ability to follow a job sheet for a particular composite part and gather all relevant tooling.
- Demonstrate the ability to operate drilling equipment to process composites.
- Demonstrate the ability to identify and perform the installation of the core.
- Demonstrate the ability to perform bagging and debagging of assemblies.
- Demonstrate the ability to perform material cutting and apply fabrics and adhesives.
- Demonstrate the ability to perform lateral and bi-lateral lay-up techniques.
- Demonstrate the ability to perform the cure of composites (oven, autoclave, etc.).
- Demonstrate the ability to select equipment and materials best suited for the particular repair and work environment.
- Demonstrate the ability to scarf out the damaged section of a component that has been identified as requiring repair and prepare the surface for repair.
- Demonstrate how to verify the finished part meets specifications.
- Demonstrate how to apply nondestructive testing methods to a given a composite component to accurately determine if the part requires repair.
- Demonstrate how to properly dispose of cured, uncured and partially cured material.
- Demonstrate a working knowledge of laminating (monolithic and sandwich).
- Demonstrate how to complete tooling repairs.
- Demonstrate the ability to identify layers, scarfing and ply counting.
- Demonstrate the ability to remove damage, scarfing and repair best practices.
- Demonstrate the ability to do field repairs/hot bonding operations.
Workplace Communications
1
20
- Demonstrate the ability to apply effective interpersonal skills to interact with supervisors, production personnel, vendors and colleagues.
Related Instruction Content
Training Provider(s):
Health and Safety
28
Health & safety - Occupational Safety and Health Administration (OSHA) and proper safety practices Health & safety - Machine guarding Health & safety - Blood borne pathogen exposure Health & safety - Confined spaces Health & safety - Fire safety and prevention measures Health & safety - Hazard communication Health & safety - Heat stress Health & safety - Industrial ergonomics Health & safety - Pedestrian safety Health & safety - Fall protection Health & safety - Walking and working surfaces Health & safety - Power hand tools Health & safety - Hearing conservation Health & safety - Respiratory protection Lock-out/Tag-out - Lock-out/Tag-out procedures Handling hazardous materials - Hazardous materials handling and storage
Foundations in Manufacturing
80
Shop practices - Apprenticeship expectations Shop practices - Housekeeping Shop practices - 5S Shop practices - Manufacturing costs Shop mathematics - Basic arithmetic operations Shop mathematics - Fractions, decimals and percentages Shop mathematics - Basic algebra Shop mathematics - Geometry Shop mathematics - Trigonometry Blueprint reading - Blueprint fundamentals Blueprint reading - Interpreting blueprints Blueprint reading - Part tolerancing Blueprint reading - Geometric dimensioning & tolerancing (GD&T) Blueprint reading - Computer-aided design (CAD), computer-aided manufacturing (CAM), and use of a coordinate measuring machine (CMM) Metrology - Units of measurement Metrology - Basic measurement Metrology - Applied Inspection Measuring and improving work - Quality programs Measuring and improving work - Continuous process improvement Measuring and improving work - Lean manufacturing Measuring and improving work - Statistics Measuring and improving work - Statistical Process Control (SPC) Problem solving - Total Productive Maintenance (TPM) program Problem solving - Root Cause Analysis Problem solving - Troubleshooting Industry onboarding - Optional customization
Technical Expertise
160
Manual operations tools and techniques - Bench work and layout Manual operations tools and techniques - Hand tools Composites - Composites processing safety Composites - Adhesives Composites - Resins (Polyester, Epoxy, Bio-resins) Composites - Matrix systems Composites - Handling and storage Composites - Material manufacturing (semi-finished, woven, pre-forms) Composites - Material science Composites - Structural design Composites - Tooling Composites - Molding Composites - Laminating Composites - Curing Composites - Inspection and Repair Composites - Hand lay-up (open molding, spray lay-up) Composites - Automated lay-up (automated fiber placement, automated tape lay-up)
People Skills
20
Workplace communications - Making a great first impression Workplace communications - Building good work relationships Workplace communications - Verbal and non-verbal communication Workplace communications - Active listening Workplace communications - Resolving conflict in the workplace Workplace communications - Writing effective emails Workplace communications - Getting your message across to audiences Workplace communications - Giving and receiving feedback Leading others - Conflict resolution Leading others - Team building Leading others - Leading and working in a diverse workplace Leading others - Delivery of on-the-job training Leading others - Mentoring Employee compliance - Optional customization